Corrosión galvánica
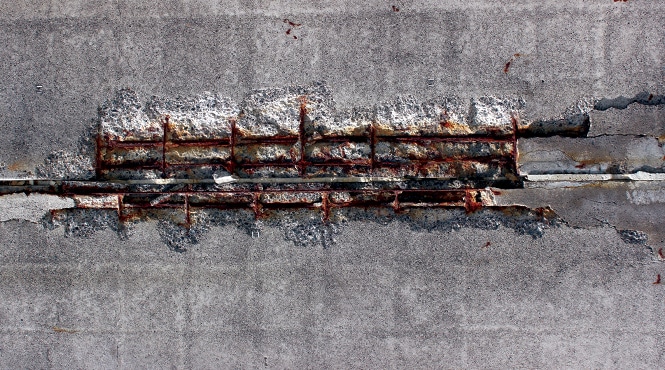
El hormigón armado está compuesto por áridos y una armadura que de manera reticular, da la resistencia solicitada al conjunto. El material más utilizado para la construcción de las armadoras, es el acero. Para ello, usualmente usado en forma de varillas coarrugadas, para mejorar su adhesión al árido.
La vida útil esperada de una estructura de hormigón armado es superior a los 100 años, por lo que, todos los elementos que intervienen deben soportar bien el paso del tiempo incluido, claro está, el acero de la armadura.
Para conseguirlo, la dosificación del hormigón debe ser la estrictamente correcta y necesaria, para que el recubrimiento de las armaduras sea el adecuado y el propio hormigón confiera al conjunto, la protección que necesitan todos sus componentes, frente a los ataques de los agentes exteriores. Este estado se configura, a grandes rasgos, durante la fase de hidratación del cemento, en la cual se genera cal hidratada, responsable de crear un ambiente altamente alcalino. Por lo tanto, las barras de acero de la armadura se encuentran, de origen, en un ambiente «pasivo» que las protege
Oxidación
Sin embargo, ya sea debido al proceso de carbonatación, en el que el hormigón pierde su alto nivel alcalino, o bien debido a la presencia de cloruros, las armaduras de acero pierden su condición pasiva, comenzando el proceso de corrosión. Estos aspectos son el resultado, por ejemplo, de ejecutar la estructura con unos recubrimientos inferiores a los necesarios según el ambiente de exposición, a la mala compactación o falta de curado del propio hormigón, etc.
La corrosión del acero en el hormigón se genera por un efecto electroquímico, presentándose en la zona anódica. Para ello, es necesaria que se de que:
- Exista una pérdida de la capa pasivadora (bien sea por la carbonatación del hormigón o la presencia de cloruros).
- Se encuentre en un ambiente húmedo y éste afecte a los poros.
- Exista oxígeno en la posición de las armaduras.
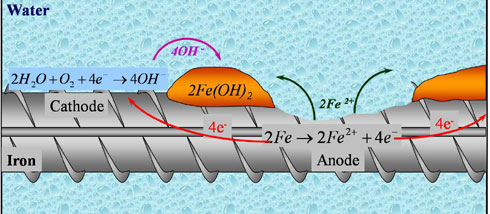
PROTECCIÓN CATÓDICA
La protección catódica de las estructuras de hormigón armado se rige por la norma UNE-EN ISO 12696:2017.
Fundamentos
En la publicación del blog dedicada a la corrosión, se vio como se producía la corrosión entre diferentes metales, en función de su «nobleza». De la misma manera, la protección catódica de las barras de acero se basa en la disposición de un metal menos noble que el acero, mediante su conexión eléctrica a las barras en el interior del hormigón. De esta forma, las armaduras se encontrarán protegidas frente a la corrosión siempre y cuando exista una corriente electroquímica entre la zona anódica (la cual se sacrificará en favor del acero) y la armadura de acero (la cual actúa como cátodo). El material más comúnmente empleado para actuar como ánodo de sacrificio es el zinc, que ya mimos en la anterior publicación que, éste era un metal «protector» del acero, por su condición y constitución.
El par galvánico formado, corresponde con una batería convencional de zinc/aire. La primera aplicación conocida de esta tecnología de protección data de 1977, en el tablero de un puente en Illinois. Tras años y esfuerzos en investigación y desarrollo se ha llegado a poder ofrecer, para el más sencillo de los sistemas, una eficacia durante una vida útil de más de 20 años. A día de hoy existen varios sistemas de protección catódica disponibles, y que son los siguientes:
- Ánodos embebidos en áreas de reparaciones efectuadas mediante parcheo y/o dispuestos fuera del área.
- Sistema híbrido de ánodos embebidos y corriente impresa.
- Sistemas aplicados en superficie.
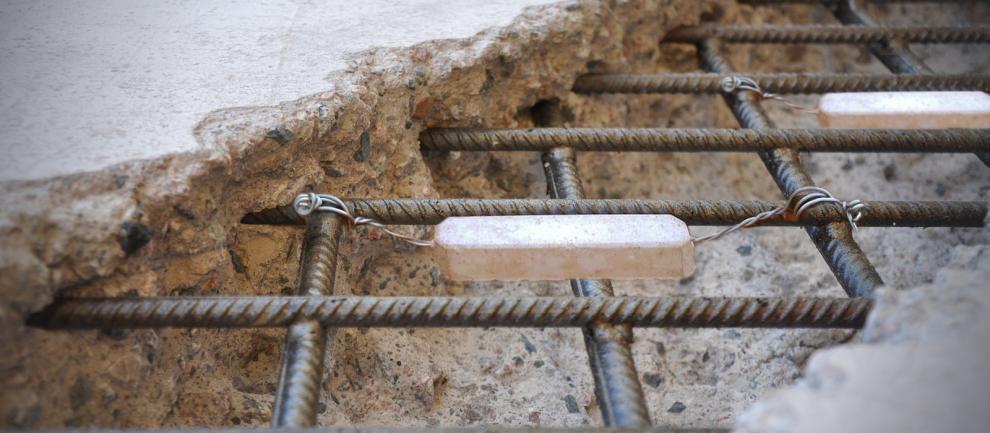
Ánodos embebidos (efecto ánodo incipiente)
Cuando se utilizan morteros de reparación con el objetivo de reconstruir zonas en las se han producido daños por corrosión de las armaduras debido a la presencia de cloruros, la zona previamente anódica se vuelve catódica debido a la alta alcalinidad del mortero fresco. Por lo tanto, la zona catódica anterior se vuelve anódica y debido a la presencia de cloruros y humedad, si no se proporciona ningún otro medio de protección o prevención, aparecerá corrosión en el área circundante de la reparación a un ritmo más acelerado de lo ocurrido hasta entonces. Este fenómeno se conoce como efecto ánodo incipiente, o también, «efecto halo«. Esta es una de las principales causas de fallo prematuro de las reparaciones efectuadas en hormigón en ambientes con cloruros. Gran parte de las reparaciones en estructuras de hormigón exhiben signos de este efecto, en los primeros 5 años después de la realización de los trabajos de reparación.
Con el objetivo de evitar el efecto ánodo incipiente, los ánodos de sacrificio se colocan en el parche (o en sus proximidades). Esta solución presenta un inconveniente que limita su empleo, ya que los ánodos colocados en las áreas de parcheo requieren estar embebidos en un mortero con una alta resistividad, lo que, por lo general, suele estar reñido con el resto de propiedades de los morteros. Sin embargo, disponiendo los ánodos en el perímetro del parche, pero fuera de la zona a rellenar con mortero posteriormente, pueden ser reparados con morteros de reparación de la calidad que la estructura requiera en cada caso, ya que únicamente el taladro en el que se embebe el ánodo deberá rellenarse con un mortero de alta resistividad.
Sistema híbrido
Esta tecnología proporciona una protección durable frente a la corrosión, así como medible y cuantificable a lo largo de la vida útil del sistema de ánodos diseñado para cada estructura. El sistema híbrido recoge las ventajas de los sistemas anteriormente descritos, añadiendo los que nos ofrece el hecho de aplicar corrientes, de forma externa. Para ello, durante un periodo de tiempo inicial, (normalmente una o dos semanas dependiendo de la corriente empleada), se aplica una corriente al sistema de ánodos, utilizando una fuente de alimentación. Con esta corriente inicial se detiene el proceso de corrosión ocasionada por la degradación del medio en el que se encuentra la armadura. Tras la fase inicial, los ánodos se mantienen conectados al acero, lo que consigue y mantiene una situación de acero pasivo durante los años de vida de los ánodos. En esta fase se retira la fuente de alimentación una vez se comprueba que los circuitos de ánodos mantienen la intensidad suficiente, lo que abarata tanto la instalación como el mantenimiento del sistema durante la vida útil de la estructura.
Las principales ventajas de este sistema, son:
- Protección a largo plazo contra la corrosión.
- Mínimo mantenimiento.
- Bajos costes.
- No requiere conexión a largo plazo de fuentes de alimentación (lo que supone una ventaja en estructuras en las que el acceso es un inconveniente).
- Puede estar dirigido a áreas específicas o sobre una estructura completa (asegurando la protección con un ajuste económico para cada caso).
- Puede emplearse en estructuras de hormigón pretensadas ya que no causa fragilización por hidrógeno.
- La durabilidad del sistema viene determinada por la cantidad de zinc de los ánodos y la velocidad de estos para corroerse en cada estructura y ambiente. Conociendo la densidad de los metales y la carga eléctrica suministrada a los ánodos puede obtenerse el consumo de los ánodos, y con ello, su vida útil.
- Períodos de protección de 20 a 50 años.
CONCLUSIONES
A día de hoy, el sistema más efectivo para evitar el efecto de ánodo incipiente es el que consiste en disponer ánodos de sacrificio en el interior de la reparación, si bien su colocación en el perímetro de los parches (fuera de los mismos en planta) permite no interferir con la calidad de los mortero de reparación y protección a emplear en las siguientes fases.
El sistema híbrido de protección catódica permite controlar el avance de la corrosión, y diseñar sistemas de protección de la estructura frente a la corrosión en periodos de 20 a 50 años, siendo el que ofrece mejores prestaciones para ese periodo de tiempo con unos costes de instalación y mantenimiento más asequibles que otros sistemas.