
Introducción
En anteriores publicaciones, hemos tratado los diferentes tipos de corrosión y las causas que las generan. También hemos podido ver que, algunos metales se auto-protegen de la corrosión. Entre ellos, se encuentras los aceros resistentes a la corrosión, más conocidos como «aceros inoxidables», aunque como veremos, eso no es cierto.
En esta publicación, trataremos más extensamente no sólo de los aceros resistentes a la corrosión atmosférica y a los ácidos y álcalis, que son comúnmente conocidos como «inoxidables», sino también de los aceros refractarios resistentes a la oxidación en caliente, y los empleados en la construcción de determinadas piezas, que deben resistir la corrosión de las sustancias circundantes a ellos y a las condiciones extremas a las que se les somete.
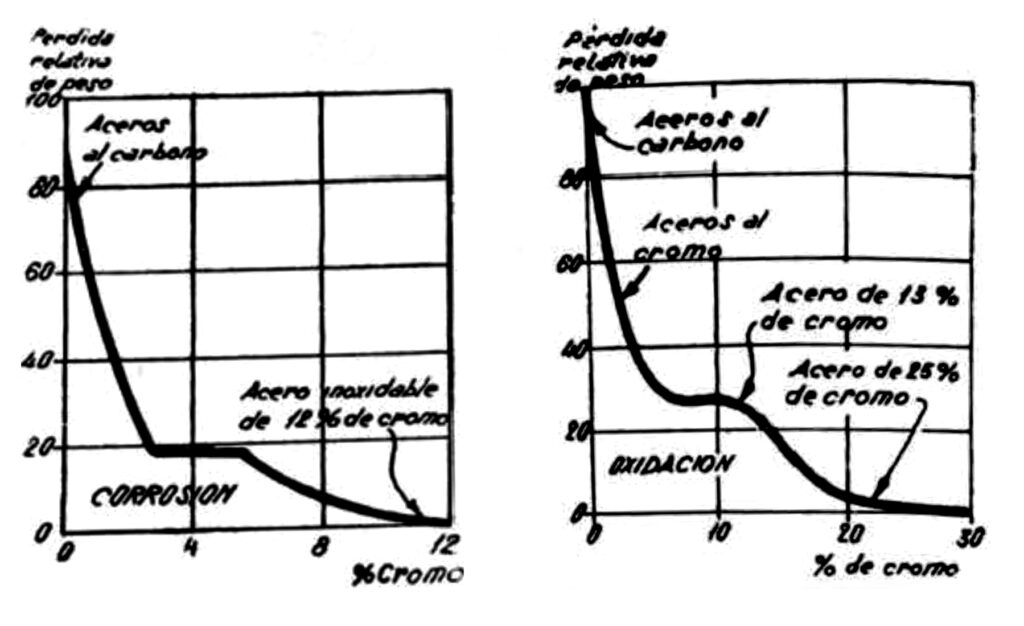
Como podremos ver, el elemento aleado que más influye en la resistencia a la corrosión y oxidación de los aceros es el cromo, atribuyéndose su influencia en este sentido a la formación de una capa de óxido de cromo muy fina que protege el interior de la pieza e impide que prospere la corrosión y la oxidación. Un porcentaje de un 12% de cromo impide totalmente la corrosión del acero en ambiente húmedo de ciudad. Para resistir la oxidación a temperaturas elevadas son necesarios porcentajes de cromo superiores, hasta de un 30%.
También trataremos como la aleación de níquel mejora aún más la resistencia a la corrosión de los aceros al cromo, creyéndose que esto se debe a que favorece la formación y da más estabilidad a la capa superficial del óxido.
Se ha de aclarar que no existe ningún acero totalmente resistente a todos los agentes corrosivos. Por lo tanto, ya podemos decir a priori que, no existe ningún acero, ni ningún metal, que sea inoxidable. Si bien es cierto que, cada tipo de acero resiste mejor los diferentes tipos de corrosión posible y de ahí que, sea uno de los factores más decisivos en el momento de elegir uno u otro. También tiene mucha importancia la estructura del material. Así, por ejemplo, si el cromo está en forma de carburo, no solamente no favorece la resistencia a la corrosión del acero sino que puede favorecerla, siendo la causa de que se inicie la corrosión de los aceros por las zonas carburadas.
Aceros semi-resistentes
Además de los aceros resistentes a la corrosión, aleados con cromo, que describiremos más adelante, hay otros materiales férricos que resisten la corrosión atmosférica y que se emplean en construcciones metálicas debiendo permanecer a la intemperie, para las que el precio hace prohibitivo el empleo de los aceros resistentes a la corrosión, puramente dichos.
En primer lugar puede citarse como material semi-resistente (hierro Armco), cuya composición es 0,012% de C, 0,017% de Mn, 0,005 % de P y 0,025 % de Si.
Los denominados hierros o aceros al cobre que se emplean en la construcción de puentes metálicos. Una composición muy utilizada es la siguiente: 0,15% de C, O,60% de Mn, 0,40 % de Cu, 0,025% de S y 0,018% de P.
También se pueden considerarse como semi-resistentes, los aceros al 5 % de cromo, empleados en la construcción de tuberías para la industria del petróleo y cuya resistencia a los gases sulfurosos es más de cinco veces mayor que la del acero ordinario. La composición media de estos aceros es: 0,05-0,25% de C, 0,50% de Si, 4-6% de Cr. En ocasiones, son aditivados con pequeños porcentajes de wolframio, molibdeno, aluminio, cobre y otros elementos, siempre en proporciones inferiores al 1%.
Aceros resistentes a la corrosión
Los aceros resistentes a la corrosión, han sido mal llamados y popularmente conocidos como «inoxidables», aunque como ya hemos visto, esto es totalmente impropio, además de imposible. Estos aceros pueden ser resistentes a la corrosión atmosférica, a los ácidos y álcalis, así como también a la oxidación provocada por las temperaturas extremadamente elevadas.
Tipos y principales características
Estos aceros, en cuya composición entra el cromo hasta en un 24 por ciento, en algunos casos, se acostumbran a clasificar en tres grupos, en función de su constitución:
- Aceros martensíticos.
- Aceros ferríticos.
- Aceros austeníticos.
Los aceros martensiticos se denominan así por admitir el temple y quedar, por tanto, mayoritariamente con una estructura martensítica, cuando están bien templados. Contienen del 13 al 17% de cromo y del O al 2% de níquel, con porcentajes de carbono variables desde el 0,08 al O,60%. Principalmente, estos aceros resisten la corrosión de ácidos débiles y la oxidación hasta temperaturas de 700°C.
Los aceros ferríticos conservan la estructura ferrítica a cualquier temperatura. Son también aceros al cromo, conteniéndolo hasta en un 27%. Resisten mejor la corrosión que los aceros martensíticos, y pueden calentarse sin oxidarse hasta los 1.1 50°C.
Los aceros austeníticos se mantienen en estado autenítico a temperatura ambiente, no transformándose la austenita ni por calentamiento ni por enfriamiento rápido en otros constituyentes. Son generalmente aceros al cromo-níquel, con porcentajes variable de estos dos elementos y porcentajes más pequeños de otros, como molibdeno, silicio y wolframio, entre otros.
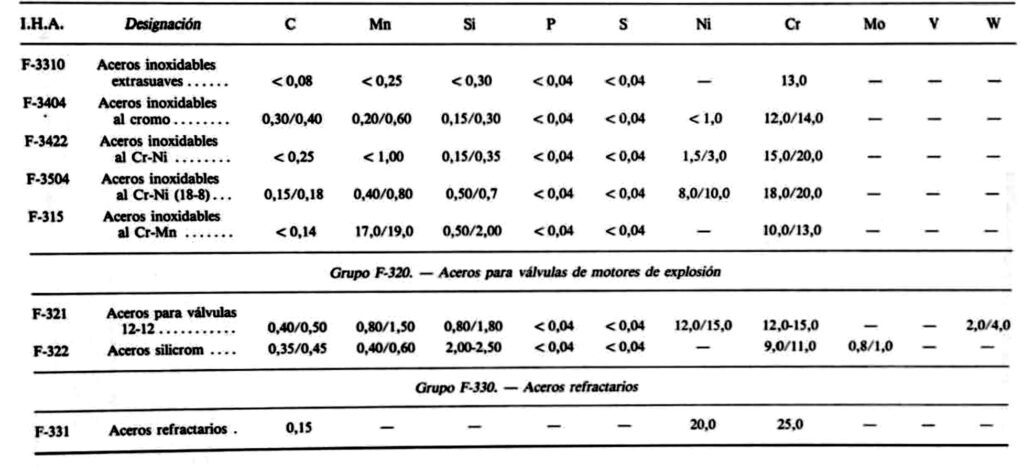
Aceros martensíticos
Principalmente, hay cuatro tipos de aceros martensíticos, en función de su composición y sus características elementales:
- Acero (o hierro) extrasuave.
- Acero de cuchillería.
- Aceros duros.
- Aceros al cromo-níquel.
El acero extrasuave, es un acero de bajo contenido en carbono, inferior a 0.08%, con un contenido de cromo del 13%. Este acero fue seleccionado por el I. H. A. con el número F-3 11. Después del templado a 960°C en agua y revenido a 600°C, queda con una resistencia de 65 Kg/mm2. Recocido, tienen un elongamiento de hasta el 30%. Es fácilmente soldable, y tiene una resistencia moderada a los ácidos débiles y a la oxidación hasta 750°C.
Por su gran ductilidad, es muy empleado en trabajos de embutición, en la fabricación de álabes de turbinas, instalaciones sanitarias, etc.
El acero de cuchillería, con un 0,30% de carbono y de 12 a 14% de cromo, fue desarrollado po Harry Brearly en 1913 y podríamos decir que, es el más clásico de los aceros martensíticos resistentes a la corrosión. Este es el acero seleccionado por el I. H. A. con el numero F-312. Después del proceso de temple a 950ºC, en aceite, y revenido a 700°C, tiene una resistencia de unos 100 Kg/mm2, un elongamiento de del 11% y una resiliencia de 11 Kg/cm2. Es decir, Que sus caraeterísticas corresponden a las de un acero de un 0,60% de carbono.
Este acero tiene mejor resistencia a la corrosión que el F-311, y se emplea en la fabricación de cuchillería, instrumentos de cirugía, ejes de bombas de agua, etc.
Los aceros martensíticos duros tienen un 17% de cromo y un porcentaje de carbono del 0,65 al 1%, con la adición, algunas veces, del 0,50% de Mo. Estos aceros, después de ser templados y revenidos, obtienen una dureza de 58 a 60 HRc, lo cual, los hace muy apropiados para herramientas clínicas y materiales quirúrgicos en general. Los de mayor dureza, con el 1% de carbono, suelen emplearse para rodamientos, bolas de molino y, un amplio espectro de piezas que deban resistir a la oxidación y deban ofrecer gran resistencia al desgaste.
Los aceros martensíticos al cromo-níquel contienen del 12 al 16% de cromo y del 1,50 al 3’70 de Ni. Estos aceros, bien templados y revenidos, que es cuando adquieren mejores cualidades, son muy resistentes a la corrosión salina del agua del mar y no sufren corrosión galvánica en contactos con bronces y latones, por lo que son muy usados en náutica, para piezas como pueden ser los ejes.
Aceros ferríticos
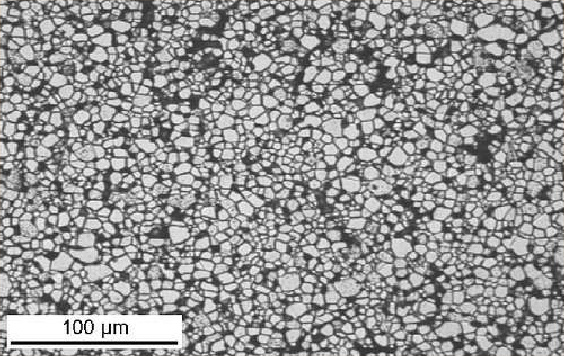
Estos aceros no cambian de constitución, que es siempre ferrítica, ni al calentarlos, ni al enfriarlos, aunque ven aumentada ligeramente su dureza, al ser enfriados rápidamente desde temperaturas elevadas.
Hay dos tipos fundamentales de aceros ferríticos: los que contienen el 16% de Cr y los que contienen 27% de Cr, ambos con una concentración de 0,10% de C.
Los primeros (16% Cr – 0,10% C), poseen gran resistencia a la corrosión atmosférica y al ataque del ácido nítrico. Se suelen emplear para la construcción de piezas decorativas para edificios y para la fabricación de piezas que deban permanecer muy expuestas al ataque del ácido nítrico.
El segundo tipo (27% Cr – 0,10% C) es muy resistente a la oxidación a temperaturas de hasta de 1.000°C, aun en presencia de gases sulfurosos. La resistencia de estos dos aceros es de unos 50 a 65 Kg/mm2, pero son muy frágiles, no rebasando su resiliencia, en general, los 5 Kg/cm2. Es destacable también que, la resiliencia aumenta notablemente cuando se calientan a temperaturas entre 150° y 200°C, lo que resulta útil para deformarlos y para cuando es necesario que trabajen a altas temperaturas.
No se les da ningún tratamiento térmico para endurecerlos y únicamente aumentan su resistencia, hasta 100 o 150 Kg/mm2, cuando se laminan en frío.
Hay que evitar el calentar estos aceros a temperaturas elevadas, pues a partir de 900°C
se inicia el crecimiento de su grano, y no puede ser afinado después más que trabajándolos en frio y recociéndolos después contra acritud a 825°C.
Para mejorar la tenacidad de los aceros ferríticos, se ha ensayado la adición de porcentajes de nitrógeno comprendidos entre 0,10 y 0,25 %, lo que limita el crecimiento del grano y los endurece notablemente. Efectos parecidos se consiguen con la adición de pequeñas cantidades de titanio y niobio.
Aceros austeníticos
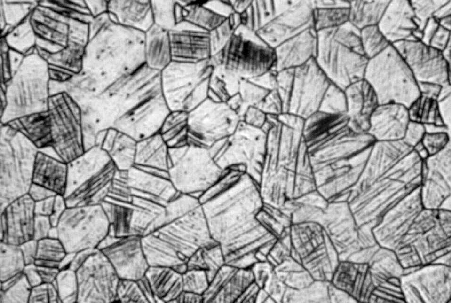
Los aceros austeníticos, podríamos decir que, son los más empleados, representando su consumo el 50% del total de los aceros resistentes a la corrosión.
En general, estos aceros están compuestos de cromo y níquel, siendo uno de los más usados, el acero con 18% de cromo y 8% de níquel. Se fabrican aceros austeníticos diferentemente aleados, con otras concentraciones de Cr y Ni, además de otros elementos, como el molibdeno, el wolfmmio, el manganeso, el silicio, principalmente.
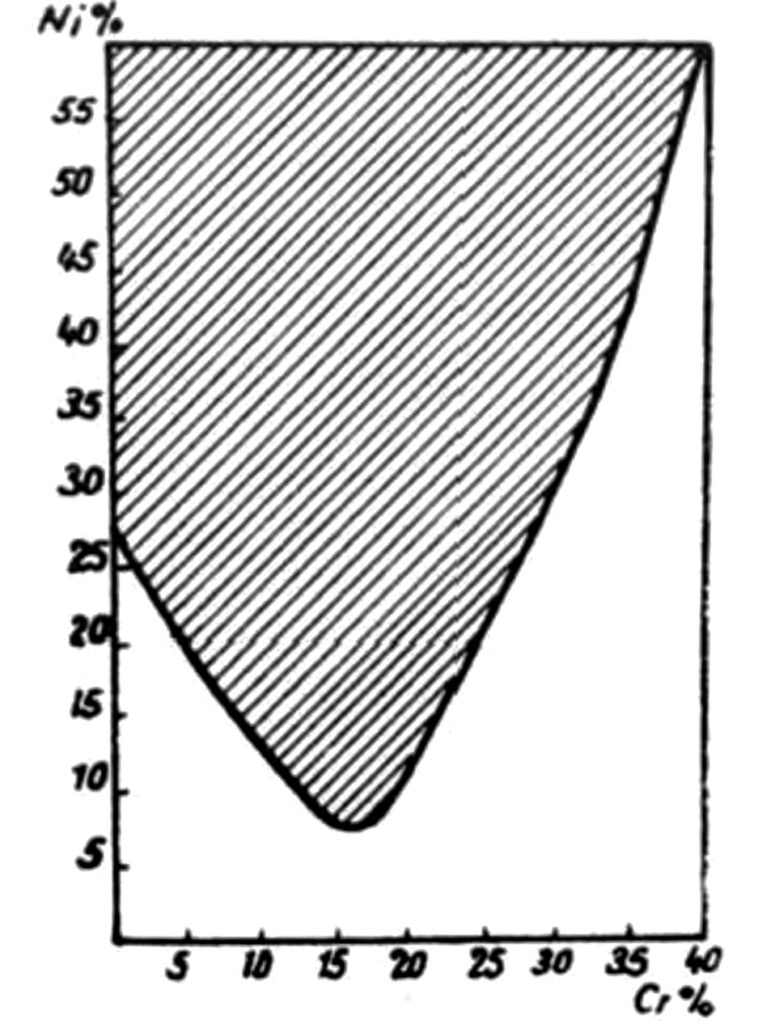
Una de las principales características de estos aceros es su no magnetismo. El elemento principal que le proporciona la resistencia a la corrosión, es el cromo; pero así como en el caso de los aceros martensíticos y ferrilicos, este elemento se configura como casi el único que les proporciona cualidades resistivas a la corrosión, en los aceros austeníticos, el níquel desempeña un importante papel en la función de protección frente a la corrosión. El níquel favorece la estabilidad de la austenita y aumenta la resistencia a la corrosión del cromo. Además, aumentando la proporción de níquel, mejora la ductilidad del acero, empleándose para trabajos de embutición aceros de 12% de cromo y 12% de níquel.
La resistencia a la corrosión en caliente se mejora con la adición de molibdeno, wolframio y silicio. También el manganeso se ha empleado para sustituir al níquel, pero requiere que sean trabajados con extremo cuidado, de lo contrario, los aceros cromo-manganeso experimentan corrosión intergranular, sobre todos si se calientan a temperaturas entre 500° Y 800°C.
Tipos de aceros austeníticos
Podríamos decir que, el más clásico de todos los aceros austeníticos es el conocido como «18-8», es decir, de 18 a 20% de Cr, de 8 a 10% de Ni y de 0,15 a 0,18% de C. Con esta composición fue seleccionado
por el I.H.A. con el número F-314.
Sus características mecánicas son las siguientes:
- Resistencia mecánica: 60-66 Kg/mm2.
- Límite elástico: 21-28 Kg/mm2.
- Elongamiento: 60-55%.
- Resiliencia: 32-35 Kg/cm2.
- Muy dúctil y apto para trabajos de embutición.
A través del laminado en frío, se consiguen resistencias de hasta 160 Kg/mm2. El ablandamiento se consigue calentándolo a 1.050°C y enfriándolo en agua o aceite. Este acero es muy empleado como elemento decorativo y para fabricación de accesorios para industrias químicas y textiles.
Algunas variantes del acero austenítico F-314, es el de bajo contenido en carbono, con solo 0,08% C (e incluso inferior, según el tipo de aleación), muy empleado para las piezas que deban someterse a procesos de soldadura o que durante el trabajo normal deban estar expuestas a temperaturas comprendidas entre 400° y 500°C.
El acero «18-8» con 2 a 3% de molibdeno resiste mejor la corrosión que el 18-8 clásico, así como a algunos ácido como el acético y el fosfórico, entre otros. También es más elevada su resistencia mecánica en caliente.
El acero «18-8» con titanio y niobio, con un contenido de carbono de hasta el 0,08%, se emplea para piezas que deben ser soldadas o que deban trabajar a un temperaturas entre los 500° y los 650°C.
Este tipo de aceros, aditivados con el 2,5% de silicio se configuran muy resistentes a la oxidación, hasta temperaturas de 925 °C, haciéndose muy común para la fabricación de hogares, parrillas y otros elementos que deban estar expuestos a altas temperaturas.
Los aceros con 25% de cromo y 12% de níquel, resisten perfectamente temperaturas de hasta 1100ºC, pero no debe utilizarse en temperaturas comprendidas entre 500° y 650°, puesto que es su zona frágil.
El acero con 25% de cromo y 20% de níquel, es el que mejor resiste a las temperaturas más elevadas. Incluso es resistente en presencia de gases que contengan S02, pero en cambio es atacado por el SO3. Este tipo de acero adolece también de una zona de fragilidad entre los 500° y 600°C.
El acero con 20% de cromo y 25% de níquel, resiste muy bien la oxidación a altas temperaturas y la corrosión de ácidos y álcalis. No es atacado por el SO3, pero en cambio, sí que lo es por el SO2.
El acero con 12% de cromo y 12% de níquel, es muy dúctil, por lo que lo hace idóneo en trabajos de embutición.
El acero F-315, con 10-13% de Cr, 17-19 de Mn y 0,14% de C, es un acero soldable y resistente a altas temperaturas. Por sus características, es muy empleado en la fabricación de colectores de escape de motores de combustión y piezas similares.
Corrosión intergranular en los aceros austenítlcos
Una de las características más destacables de los aceros austeníticos, es el hecho de tener una zona de temperaturas entre los 450ºC y los 650ºC, en la que sufren de corrosión entre los granos. Esta corrosión se presenta frecuentemente en piezas que han sido sometidas a procesos de soldadura, en las zonas que, debido a la soldadura, se han calentado a Ias temperaturas próximas al rango citado. A esta parte de la pieza se le atribuye el nombre de ZAT (Zona Afectada por la Temperatura). Al principio, no se acusa ninguna anormalidad, pero poco a poco van apareciendo grietas, sobretodo si se somete el acero a esfuerzos, por ejemplo, tras un mecanizado.
La causa de esta corrosión es la formación de carburos de cromo, a modo de precipitación, a costa de empobrece de cromo la zona del acero cercana, que queda indefensa, por resultar ser anódica en relación a las zonas de mayor concentración de cromo.
Para evitar esta corrosión pueden emplearse diversos procedimientos, entre los cuales:
- Reducirse el contenido de carbono hasta un porcentaje inferior al 0,03%, con lo que sedificulta la formación de carburos, por la escasez del carbono en el acero.
- Alear eI acero con titanio, molibdeno o niobio, con los que preferentemente se combina el carbono para formar carburos en lugar de hacerlo con el cromo, consiguiendo así estabilizar el acero a la franja «delicada» de temperaturas entre los 450° y 650°C.
- Calemar el material a 1.050°C después de que haya sufrido un calenlamlento en la zona de temperaturas a evitar, para así, disolver los carburos, pudiendo a continuación, enfriarlo al aire.
Aceros para válvulas de motores de combustión
Las válvulas de los motores de explosión, se configuran como un caso particular en el uso y elección del acero a emplear, debido a que deben resistir la corrosión de los gases calientes procedentes de la combustión, la oxidación a altas temperaturas y, además, poseer una buena resistencia mecánica.
Uno de los aceros más empleados es el F-322, con 0,35 a 0,45% de carbono, de 9 a 11% de cromo, de 2 a 2,5% de silicio y 0,8 a 1% de molibdeno. Este acero resiste la oxidación hasta los 800°C, siendo el punto de transformación de su estructura en austenita a 900°C. Gracias a esto, como que estas piezas no trabajan a más de 800°C, el acero no sufre endurecimiento secundario en el proceso de calentarse y enfriarse. El temple de este acero se efectúa calentando a 1.050°C y enfriando en aceite. Revenido a temperaturas de 750ºC a 800°C, el resultado es una resistencia mecánica de aproximadamente lOO Kg/mm2 y una dureza de unos 300 Brinell.
Para los antiguos motores de explosión, que trabajaban con gasolina aditivada con tetraetilo de plomo, no era adecuado este acero, pues resultaba muy atacado por los vapores de la gasolina. Para estos motores, se empleaba el acero cromo-níquel, de O,80% de carbono, 0,20% de cromo, 2% de níquel y 2% de silicio. Este acero se templa a 1.050°C, con enfriamiento al aire, y se reviene a 700°C.
Un acero muy utilizado para la fabricación de válvulas de motores de aviación, que si bien su resistencia a la corrosión no es muy superior a la de otros aceros, su resistencia en caliente es suprior a la de los aceros al cromo y al silicio. Éste tiene una composición de 0,40 al 05% de carbono, del 12 al 15% de cromo, del 12 al 15% de níquel, del 0,80 al 1 ,80% de silicio y el 2 a 4% de wolframio. Este acero austenítico es el F-321.
Aceros refractarios
Bajo la denominación de aceros refractarios se conocen una serie de materiales que resisten sin oxidarse y conservan buena resistencia mecánica a elevadas temperaturas.
De los aceros que hemos citado como resistentes a la corrosión, en los parágrafos precedentes, los más resistentes a la oxidación son el acero ferrítico al 27% de cromo y los austeníticos cromo-níquel de 25-20 y 25-12. Todos se conservan sin formar cantidades apreciables de cascarilla hasta los 1.000°C.
A pesar de ello, no basta con no oxidarse, sino que es, además, necesario que conserven buena resistencia a temperaturas elevadas. La resistencia de los aceros disminuye significativamente en caliente, sobre todo a partir de los 450°C. Se han realizado ensayos para determinar la carga máxima que pueden resistir los
aceros a 500°C, y además la carga que pueden soportar a esa temperatura sin que se rompan en el plazo de mil horas, siendo esta carga muy inferior a la primera.
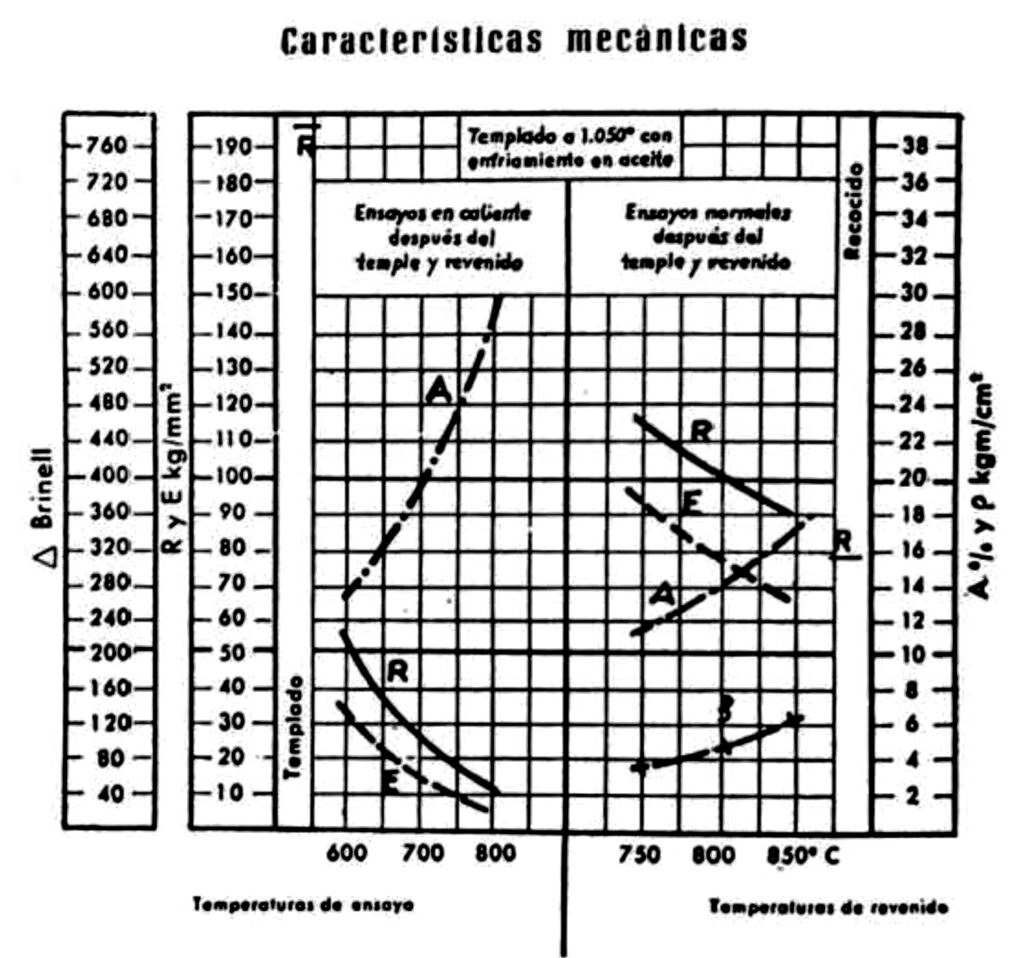
De lo anteriormente comentado se desprende que, los aceros más resistentes a elevadas temperaturas
son los austeníticos aleados con cromo y níquel.
Para la fabricación de piezas que deban resistir bien a la oxidación a elevadas temperaturas, los aceros más adecuados son:
Aceros ferríticos con un 27% de cromo, para piezas que deben resistir elevadas temperaturas y tener, además, buena resistencia mecánica.
Aceros austeníticos, 25-20, como el F-331 o los cromo-níquel 18-8, como el F-314.
Aceros austeníticos enriquecidos con molibdeno, si además se necesita una elevada resistencia a la deformación bajo carga en caliente, es decir, fluencia.
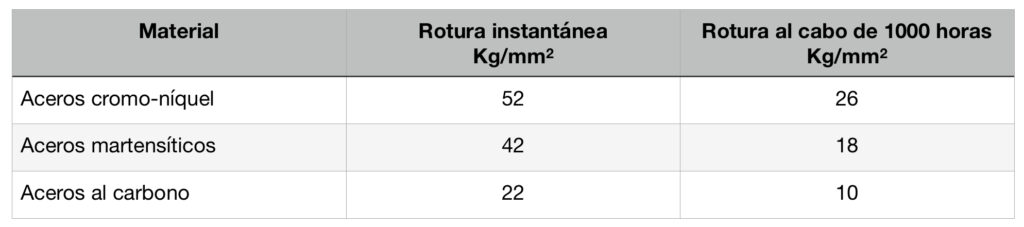
Aceros inoxidables austeníticos, con elevado porcentaje de níquel si se trata de resistir el calor en atmósfera controlada a base de óxido de carbono o hidrocarburos, que favorecen la formación de carburos de cromo en el acero y, por tanto, la corrosión intergranular. En este grupo pueden incluirse los aceros con el 35% de Ni y 18 % Cr; los de 22 % de Ni y 15 % de Cr, y los de 25 % de Mn y 9 % de Cr.
Aleaciones férricas para resistencia eléctricas. Otros tipos de aleaciones férricas resistentes al calor son los que se emplean para la fabricación de resistencias para hornos eléctricos. Las composiciones más utilizadas son las siguientes:
- Hierro 76%, cromo 20%, aluminio 4%.
- Hierro 67%, cromo 25%, aluminio 5%, cobalto, 3%.
- Hierro 55,5%, cromo 37%, aluminio 7,5%.
Aleaciones especiales para turbinas de gas. Para construcción de álabes de turbinas de gas que trabajan a temperaturas de 650ºC a 750ºC se pueden usar aceros aleados con níquel, con porcentajes de hasta el 40 al 80%, así como, con aleaciones de cobalto del 50 al 70 %, con una excelente resistencia en piezas que deban trabajar a altas temperaturas.