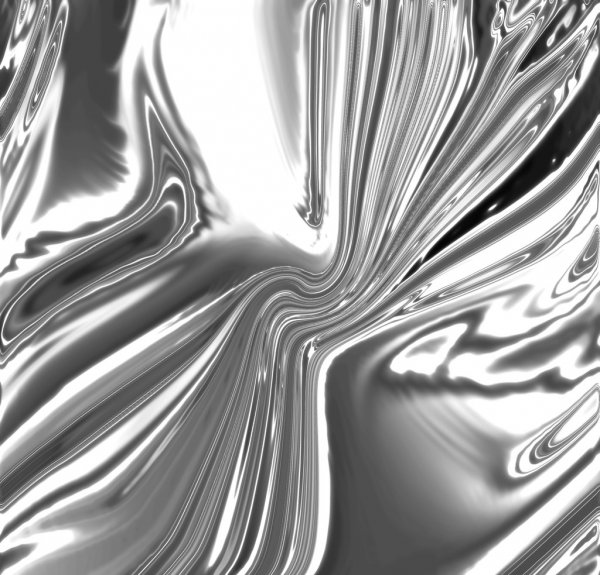
Características del cromado duro
Con el nombre de cromado duro, se designa un recubrimiento galvánico que se realiza sobre metales, con arreglo a una técnica especial que mejora algunas de las propiedades del metal base.
El cromado duro mejora, sobre todo, la resistencia al desgaste, al rayado, a la penetración, a la corrosión, y mejora también, en general, el coeficiente de rozamiento del mátalos base.
La resistencia al desgaste es la cualidad más apreciada del cromado duro, siendo superior en cinco veces a la del acero F-521, de 1,6% de C y 12% de Cr, empleado para la fabricación de hileras, y cuatro veces superior a la del acero cementado.
La resistencia al rayado es también muy elevada, lo que aumenta el valor de la protección contra la corrosión del cromo duro, ya que garantiza la permanencia de la capa aunque accidentalmente resulte rayada.
La dureza a la penetración es superior a 70 Rockwell-C, o sea, aproximadamente 1.165 Vickers; sin embargo, no es la dureza a la penetración una de las cualidades más interesantes del cromo duro, pues no depende de ella exclusivamente la resistencia al desgaste, que es la cualidad que más se busca en la aplicación del cromo duro.
La resistencia a la corrosión del cromo duro es muy elevada hasta unos 800°C, temperatura a la que comienza a oxidarse. Sin embargo, esta protección contra la corrosión está condicionada a que no existan o que no se produzcan porosidades ni grietas, pues en este caso, como el cromo respecto al hierro es anódico, se producirá la corrosión acelerada. El espesor de película que proporciona una mínima garantía contra la corrosión es de 0,05 mm.
El rozamiento sobre superficies cromadas es suave y ligeramente untuoso, y su coeficiente, inferior al del acero sobre acero y sobre otros materiales. Tiene el inconveniente de que no retiene bien la película de aceite lubricante, dificultad que se ha logrado superar en algunas aplicaciones utilizando el denominado cromado duro poroso, que más adelante se tratará.
Aplicaciones del cromado duro
Se aplica el cromado duro tanto a piezas de nueva fabricación como a piezas desgastadas, que son perfectamente recuperadas e incluso, algunas propiedades mejoradas.
El cromado duro se utiliza en la fabricación de motores de explosión, para el cromado de cilindros, camisas, segmentos, cigüeñales, ejes de levas, etc.
Se emplea también en la fabricación y recuperación de cilindros: para laminación de metales, para máquinas de fabricar papel, para teñido y estampación de telas, etc.
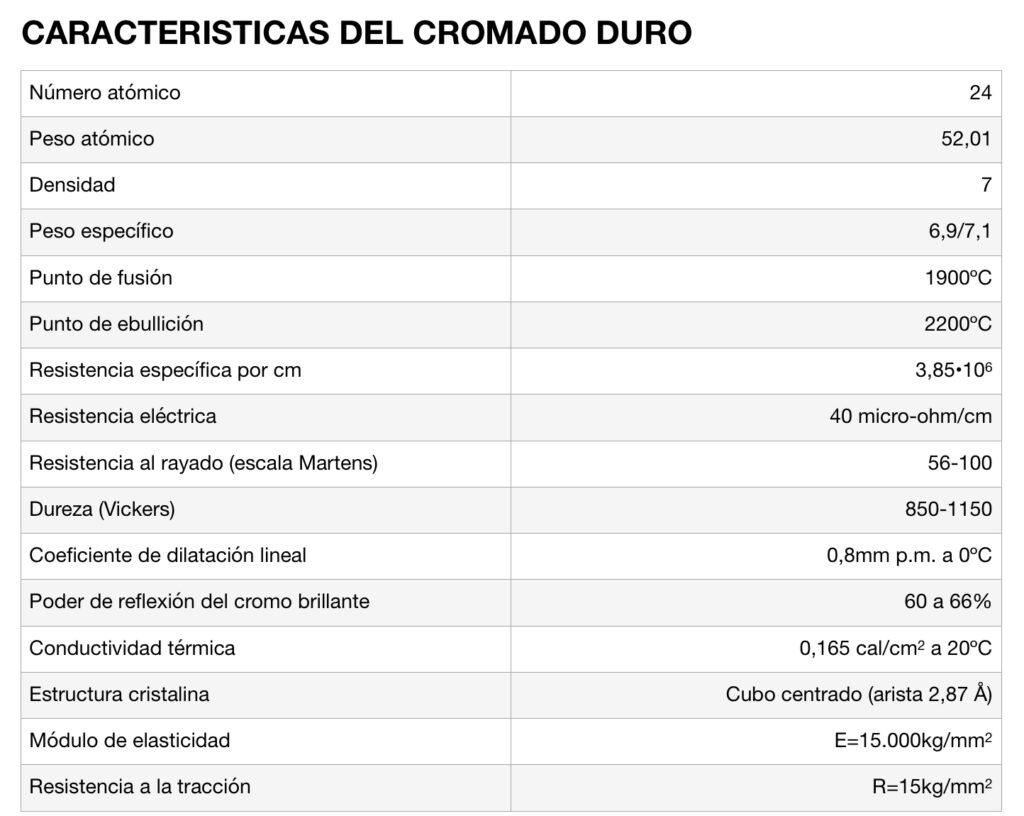
El cromado duro da excelentes resultados y prolonga mucho la vida de los ejes y pistones de bombas hidráulicas, pistones de prensas, de martillos de forja, de máquinas neumáticas, etc.
Los plásticos, pastas alimenticias, etc., no se adhieren al cromo duro, lo que se aprovecha para cromar moldes utilizados para la fabricación de estos productos.
Otra aplicación muy interesante es el cromado de matrices, troqueles, machos, tanto para metales como para plástico.
Las herramientas como brocas, escariadores, etc., cromadas, mejoran no sólo en duración, sino en velocidad de trabajo, que puede elevarse por la mayor facilidad para el desprendimiento de la viruta, cuando las superficies están cromadas.
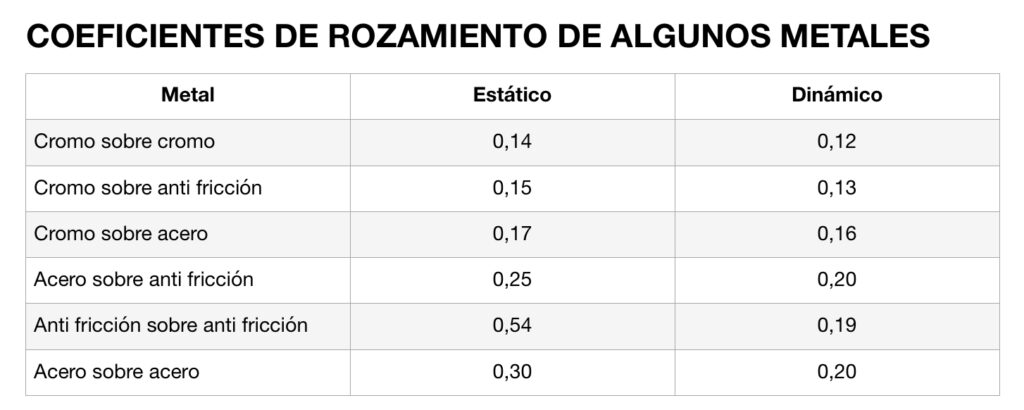
También los instrumentos de medida, sobre todo los calibres, se croman, lo que, además de proteger la superficie contra la corrosión, mantiene sus medidas exactas mucho más tiempo, gracias a la resistencia al desgaste del cromado duro.
Destacar también que, se utiliza para recubrir zonas del armamento militar.
Materiales que pueden ser cromados
El cromo duro se puede aplicar sobre casi todos los metales; pero a los que más resulta beneficioso son: el acero, la fundición de hierro, el aluminio, el latón y el cobre.
Los aceros al carbono y los aceros aleados pueden cromarse previa preparación de la superficie. Si han sido sometidos a tratamientos térmicos, se les debe dar un tratamiento de estabilización a 200ºC durante 30 minutos, para reducir tensiones. Y, desde luego, eliminar, con un fuerte decapado previo, los residuos que tenga la superficie de cementaciones o nitruraciones.
En el caso de la fundición de hierro, sólo puede cromarse si es de grano fino, no existen poros y estando la superficie perfectamente pulimentada. Esto es algo que se cumple a la perfección, en los cilindros, segmentos y camisas de los motores de combustión interna.
El aluminio, el latón y el cobre pueden cromarse siguiendo una técnica especial para cada metal.
Técnica del cromado duro
Las principales diferencias entre la técnica del cromado duro y las del cromado decorativo están en las densidades de corriente y en la temperatura del baño. Además, los espesores de película depositados en el cromado duro son mucho mayores que los del cromado decorativo.
En el cromado decorativo se trabaja con intensidades máximas de 5 A por dm2, mientras que en el cromado duro se utilizan densidades de corriente de 30 a 50 A por dm2.
Respecto a la temperatura, en el cromado decorativo no se sobrepasan los 45°C, mientras que en el cromado duro se trabaja a temperaturas de 55°C. En realidad, la mayor temperatura del baño es consecuencia de la necesidad de emplear mayores densidades de corriente, ya que éstas dependen de la temperatura del electrolito.
El espesor de la película que normalmente se deposita en el cromado duro es de 0,05 a 0,1 mm., y en el cromado decorativo no llega, en general, a 0,001 mm.
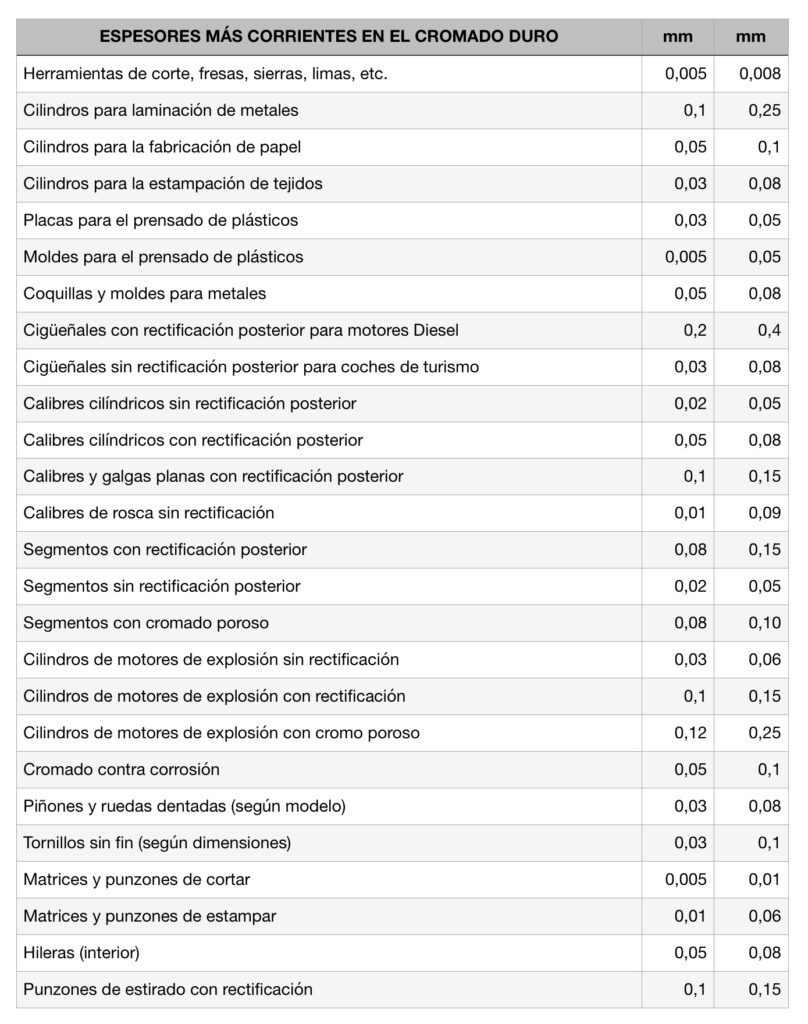
Dentro de cada temperatura existe una densidad de corriente adecuada para obtener películas de la máxima dureza al desgaste. Y para cada densidad de corriente se obtiene una velocidad de deposición de película.
Como norma general, y si el espesor de película necesario es superior a 0,1 mm; por tratarse de una reparación, se recomienda aplicar primero, electrolíticamente, una capa de níquel que puede llegar a tener varios milímetros de espesor, y después rectificar y cromar. Como la dureza de la capa de níquel no será superior a 400 Brinell, puede ser que este procedimiento no sea aplicable en algunos casos.
Cromado poroso
El cromado poroso se desarrolló para resolver los defectos de lubricación que se presentaban cuando se trató de aplicar el cromado duro a los cilindros y camisas de los motores de combustión interna.
El cromado poroso consiste en producir en la superficie del cromado liso, realizado con la técnica que se ha descrito, pequeñas rayas o cráteres, sin llegar nunca a perforar totalmente la película de cromo hasta el metal base, con objeto de facilitar la dispersión del aceite.
Se ha ensayado el producir un moleteado previo del metal base que resultase reproducido al cromar. Y también se ha ensayado producir mecánicamente en la superficie del cromo un rayado o picado.
Pero los procedimientos actualmente más empleados se basan en el ataque anódico de la pieza, una vez cromada con una película de espesor a sobremedida. O sea, que se deposita una película de cromo liso de unos 0,1 mm. Después se ataca la película de cromo electrolíticamente, utilizando la pieza como ánodo y una plancha de acero resistente a la oxidación como cátodo, y según el electrólito empleado se obtiene un grabado en forma de picado o forma de malla, quedando una película base mínima sobre el metal de 0,01 mm. y espesor total de la película porosa, después de rectificada, de 0,05 mm.
Cromado del aluminio
El cromado duro del aluminio y sus aleaciones resulta interesante por fabricarse estos materiales cilindros y camisas de motores de explosión.
La preparación de las superficies para el cromado del aluminio tiende a producir rugosidad que facilite la adherencia del cromo.
También puede lograrse una buena adherencia aplicando sobre el metal base una película intermedia de cobre o níquel.
Después de cualquiera de las dos preparaciones descritas, el cromado se realiza la técnica normal.
La adhesión conseguida con la preparación especial cromando sobre cobre o níquel es muy buena, y a pesar de que el coeficiente de dilatación del cromo es la tercera parte que la del de aluminio, sólo se producen grietas en la superficie del cromado, sin llegar a desprenderse ninguna porción de película.
Nuevas técnicas en tratamientos superficiales
En los últimos años se ha asistido a un gran crecimiento de las técnicas de deposición gran aplicación en la industria química, mecánica, eléctrica, óptica, microelectrónica, etc., que pueden clasificar en dos grandes grupos:
- Técnicas que producen revestimientos por deposición de un material sobre un sustrato, junto a la clásica electrodeposición, podemos citar la técnica de deposición de vapor (CVD), deposición física de vapor (PVD) y proyección térmica.
- Técnicas que provocan la alteración de la superficie del sustrato, pudiendo corregirse por difusión, por fusión superficial localizada, por tratamientos térmicos o por implantación iónica.
Los procesos de deposición utilizados actualmente en aplicaciones de alta tecnología son principalmente:
- Proyección por plasma.
- Deposición química de vapor (CVD).
- Deposición física de vapor (PVD).
- Implantación iónica.
El proceso de proyección térmica por plasma consiste en un chorro de plasma a elevada temperatura que funde y arrastra al polvo de material de aportación, haciéndole impactar sobre la superficie a recubrir en donde solidifica.
Este proceso implica condensación de gotitas, por lo que la rugosidad del sustrato debe ser del mismo orden de magnitud que sus dimensiones.
Se utiliza este procedimiento en la deposición de cermets tales como el de carburo de Wolframio-Cobalto en cojinetes.
Las técnicas CVD y PVD han surgido como técnicas para la producción de capas compuestos duros tales como carburos y nitruros sobre herramientas y componentes con objeto de prolongar su vida en servicio.
En el caso de CVD se depositan revestimientos utilizando reacciones químicas implican a una o más especies sobre un sustrato a temperaturas elevadas.
Los procesos de deposición física de vapor PVD constan de las siguientes etapas:
a) Síntesis o creación de la fase vapor.
b) Transporte desde la fuente hasta el sustrato.
Para la primera etapa se puede utilizar calentamiento por resistencia, inducción electrónico, arco, láser y otros.
La segunda etapa puede tener lugar también bajo una gran variedad de condiciones tales como flujo molecular (presiones inferiores a 10-4 torr.), flujo viscoso (presiones superiores a 10-3 torr.) o en presencia de plasma.
Los procesos PVD son los más versátiles para conseguir la deposición de compuestos refractarios en un amplio margen de velocidades de deposición con control de la composición estequiométrica y de la microestructura.
Por otra parte, la temperatura del sustrato puede variar desde la ambiente hasta muy elevadas temperaturas.
La técnica de implantación iónica emplea el bombardeo con iones acelerados para introducir distintos tipos de átomos en las primeras capas de un material con el fin de modificar su superficie y hacerla más resistente al desgaste y a la corrosión, así como mejorar otras características.
Dependiendo del flujo iónico, el cambio en la composición puede ir desde partes por millón (caso del dopado de semiconductores) hasta decenas por ciento en la modificación de las propiedades superficiales de los metales.
Los tiempos requeridos en implantación iónica van desde segundos hasta horas por cada cm2 de superficie a tratar. Este tratamiento se efectúa a temperatura ambiente.
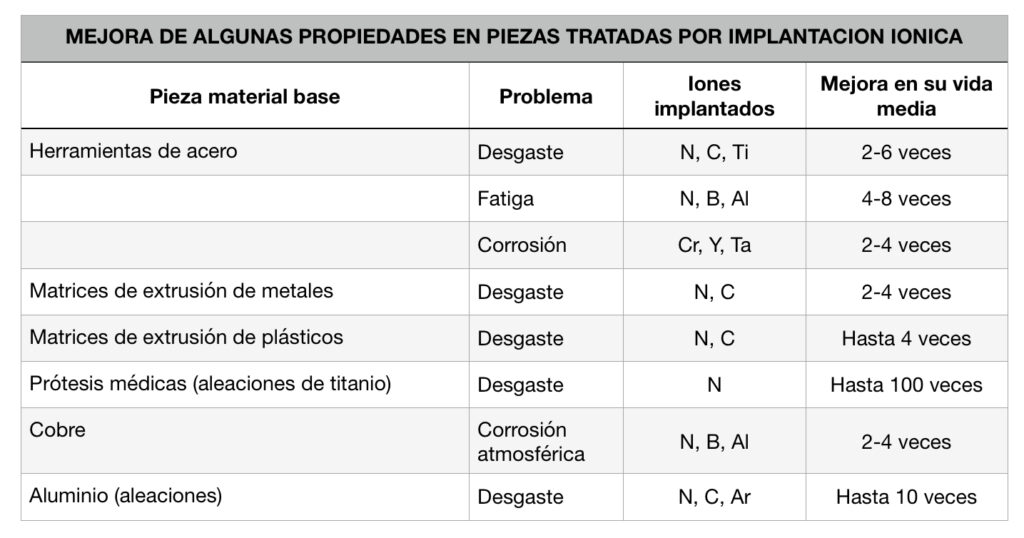