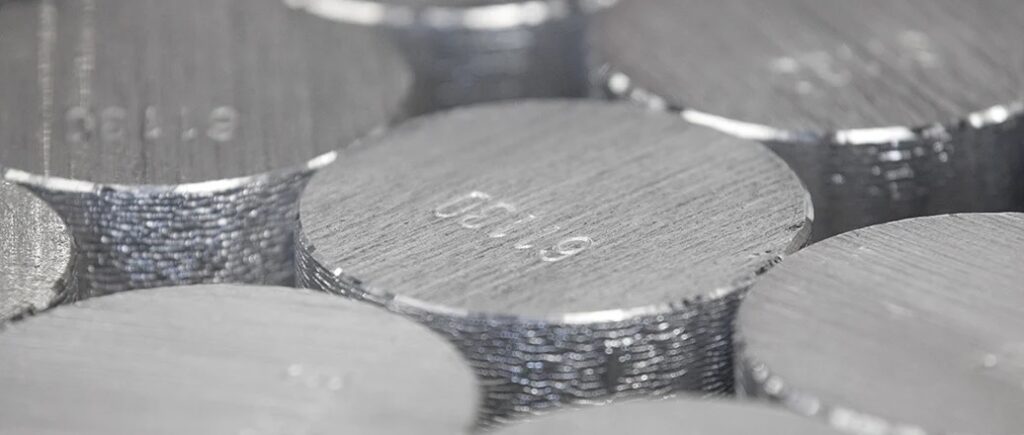
1. Metales no férreos
Los productos siderúrgicos férreos son, con mucha diferencia los más utilizados de ente todos los metales conocidos, siendo su producción mundial, aproximadamente veinte veces superior a la de todos los demás metales.
Esta supremacía se debe, además de a su precio de coste relativamente económico, a sus excelentes propiedades mecánicas, que, sobre todo las de los aceros, ya hemos visto cómo pueden variarse para amoldarlas a la conveniencia del usuario para trabajarlos más cómodamente, dándose después el “punto” deseado de dureza, resistencia y tenacidad.
Tienen en cambio, los productos siderúrgicos el grave defecto de que son muy sensibles a la oxidación y corrosión atmosférica, ya que es el hierro el metal industrial que más fácilmente se deteriora en el aire. Aunque, como ya hemos visto en publicaciones anteriores, se fabrican aceros resistentes a la corrosión, los cuales presentan un estado de auto protección durante el proceso de oxidación, cabe destacar su elevado coste.
Los metales industriales no férreos y sus aleaciones son, en general, resistentes a la oxidación y corrosión atmosférica. Pero no es ésta la única buena cualidad, que los hace recomendables para muchas aplicaciones, sino también la facilidad con que se moldean y mecanizan; la elevada resistencia mecánica con relación a su peso de algunas aleaciones; la gran conductividad térmica y eléctrica del cobre y también su bello acabado desde el punto de vista decorativo.
2. Aleaciones ligeras
Se suelen denominan aleaciones ligeras las aleaciones que tienen como elemento base o principal el aluminio.
Respecto a los metales de adición, los más empleados son el cobre, silicio, cinc, manganeso, níquel, hierro, titanio, cromo y cobalto. Estos metales pueden figurar en las aleaciones juntos o aislados. En general, la proporción total en que forman parte de las aleaciones ligeras no pasa del 15%.
La característica principal de las aleaciones ligeras es su bajo peso específico que, en algunas de ellas llega a ser hasta de 1/3 del peso específico del acero, y aun resulta más interesante la relación de resistencia mecánica a peso específico, que en algunos tipos de aleaciones ligeras es la más alta entre todos los metales y aleaciones conocidos. Esto las hace indispensables para determinadas aplicaciones, como por ejemplo, para las construcciones aeronáuticas en las que interesan materiales muy ligeros con una resistencia mecánica mínima.
3. El aluminio
El aluminio es uno de los principales componentes de la corteza terrestre conocida, de la que forma parte en una proporción del 8,13%, superior a la del hierro, que se supone es de un 5%, y solamente superada por el silicio, que es de un 26,5%.
El aluminio no se encuentra puro en la naturaleza, sino formando parte de los minerales, de los cuales los más importantes son las bauxitas, que están formadas por 62-65% de alúmina (AI2 03), hasta un 28% de óxido de hierro (Fe2 03), 12-30% de agua de hidratación (H2 O) y hasta un 8 % de sílice (Si O2),
La obtención del aluminio se realiza en dos fases:
1ª. Separación de la alúmina (AI2 03) de las bauxitas por el procedimiento Mayer, que comprende las siguientes operaciones: se calientan las bauxitas para deshidratarlas, una vez molidas; se atacan a continuación con lejía de sosa en caliente y a presión para formar aluminato sódico (Na2 O. AI2 03), que se separa del resto de los componentes de la bauxita; después, bajo la influencia de una pequeña cantidad de alúmina que inicia la reacción, se hidroliza el aluminato de sodio, quedando alúmina hidratada e hidróxido de sodio; y por fin se calcina la alúmina hidratada a 1.200°C, con lo que queda preparada para la fase siguiente.
2ª. Reducción de la alúmina disuelta en un baño de criolita (FNa. F3 Al), y con cierta cantidad de fundente, por electrólisis con electrodos de carbón.
Para obtener una tonelada de aluminio son necesarias, aproximadamente, 4Tm. de bauxita, 80Kg de criolita, 600Kg de electrodos de carbón y 22.000 kW/hora. La metalurgia de aluminio es, por tanto, esencialmente electrolítica.
PROPIEDADES FÍSICAS DEL ALUMINIO
El aluminio es un metal blanco brillante que, pulido semeja a la plata. Cristaliza en la red cúbica centrada en las caras. Su peso específico es igual a 2,699, es decir, casi 1/3 del hierro (7,87). El único metal industrial más ligero que el aluminio es el magnesio, de peso específico 1,74. Su conductividad eléctrica es un 60% de la del cobre y 3,5 veces mayor que la del hierro. Su punto de fusión es 660°C y el de ebullición 2.450°C. Este punto de fusión relativamente bajo, unido a su punto de ebullición bastante alto facilita su fusión y moldeo.
PROPIEDADES DEL ALUMINIO
La propiedad química más destacada del aluminio es su gran afinidad con el oxígeno, por lo que se emplea, entre otras cosas, para la desoxidación de los baños de acero, para la soldadura alumino-térmica (Al + Fe2 03), para la fabricación de explosivos, etc.
A pesar de esto y aunque parezca un contrasentido, el aluminio es completamente inalterable en el aire, pues se recubre de una delgada capa de óxido, de algunas centésimas de micra, que lo pasiva y protege el resto de la masa de la oxidación.
Debido a esta película protectora, resiste también la acción del vapor de agua, el ataque del ácido nítrico concentrado y muchos otros compuestos químicos. En cambio, es atacado por el ácido sulfúrico, el clorhídrico, el nítrico diluido y por las soluciones salinas.
PROPIEDADES MECÁNICAS DEL ALUMINIO
Las propiedades mecánicas del aluminio más interesantes son su débil resistencia mecánica y su gran ductilidad y maleabilidad, que permite forjarlo, trefilarlo en hilos delgadísimos y laminarlo en láminas o panes tan finos como los del oro, hasta de un espesor de 0,0004mm (0,4 micras). A la temperatura de 500°C se vuelve frágil y se puede pulverizar fácilmente.
CALIDADES DE ALUMINIO
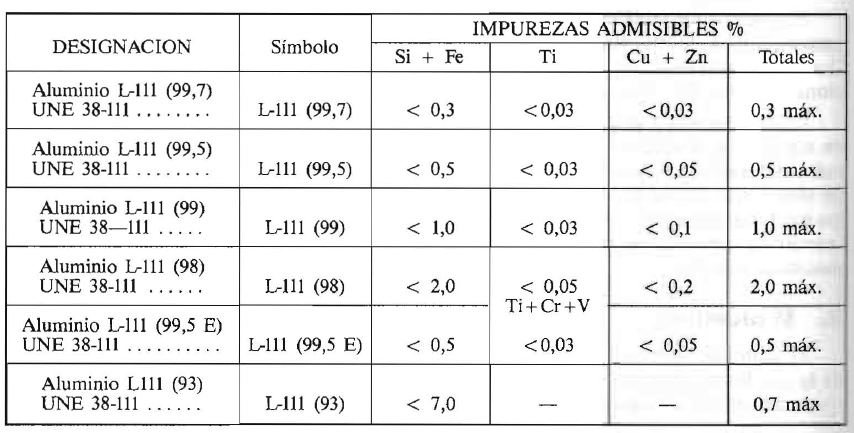
APLICACIONES DEL ALUMINIO
EI aluminio tiene multitud de aplicaciones:
Su bajo peso específico lo hace útil para la fabricación de aleaciones ligeras, extensamente empleadas en construcciones aeronáuticas y en general cada vez más en los vehículos de transporte.
Su elevada conductividad eléctrica lo hace útil para la fabricación de conductores eléctricos de aluminio técnicamente puro o en forma de cables armados con acero galvanizado.
Su elevada conductividad calorífica e inalterabilidad lo hacen útil para la fabricación de utensilios de cocina y, en general, para aparatos de intercambio de calor.
Su maleabilidad lo hace útil para la fabricación de papel de aluminio, en lo que se emplea actualmente un 10% de su producción total.
Su resistencia a la corrosión lo hace útil para fabricación de depósitos para ácido acético, cerveza, etc. También se emplea en forma de chapas para cubiertas de edificios. Y reducido a polvo para la fabricación de purpurinas y pinturas resistentes a la corrosión atmosférica.
Sus propiedades reductoras lo hacen útil para la desoxidación del hierro y otros metales y para las soldaduras alumino-térmicas.
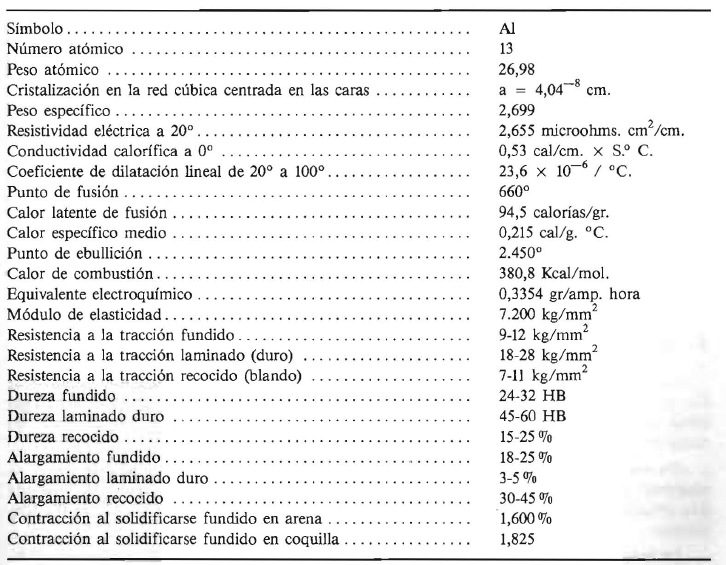
4. Aleaciones de aluminio
Los principales metales empleados para su aleación con aluminio son los siguientes: Cobre (Cu), silicio (Si), cinc (Zn), magnesio (Mg) y manganeso (Mn). y los metales que pudiéramos considerar como secundarios, son los siguientes: Níquel (Ni), titanio (Ti), hierro (Fe), cromo (Cr) y cobalto (Ca). Sólo en casos especiales se adicionan: Plomo (Pb), cadmio (Cd), antimonio (Sb) y bismuto (Bi).
5. Aleaciones aluminio-cobre
En la figura de a continuación, se ha representado el diagrama de equilibrio AI-Cu hasta un 50% de Cu, que es muy superior al porcentaje máximo empleado en estas aleaciones, que en general no supera el 15%, pues a partir de esta concentración se forman compuestos intermetálicos que hacen frágil la aleación.
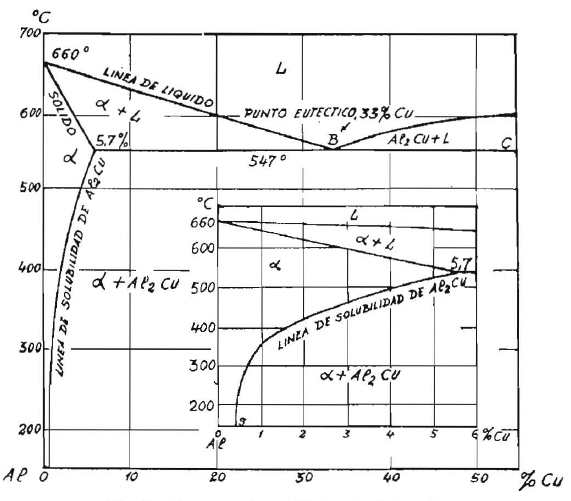
En este diagrama están presentes la fase α, que es una solución sólida de cobre en aluminio que cristaliza en la red cúbica de caras centradas. La eutéctica está formada por cristales duros de aluminiuro de cobre (Al2 Cu) incrustados en la matriz de cristales α.
La temperatura eutéctica es 547°C, que corresponde a una concentración del 33% de Cu.
La solubilidad del cobre en el aluminio varía del 0,45% a 300°C hasta 5,7% a 547°C, lo que se utiliza para el temple de precipitación a que pueden ser sometidas estas aleaciones, como veremos en el parágrafo 14. El cobre endurece mucho el aluminio, por lo que estas aleaciones poseen propiedades mecánicas excepcionales, pero mantienen la buena maquinabilidad y ligereza que posee el aluminio. Su peso específico es alrededor de 2,8.
6. Aleaciones aluminio-silicio
Estas aleaciones siguen en importancia a las del aluminio-cobre. El porcentaje de silicio suele variar del 5 al 20%.
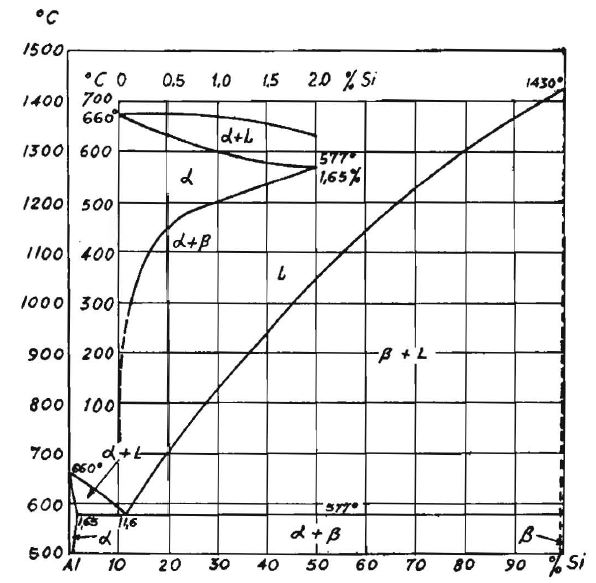
En la figura anterior se ha representado el diagrama de equilibrio Al-Si, que es muy sencillo, pues no forma más que una solución sólida ex de silicio en aluminio y una solución sólida (3 de aluminio en silicio, aunque algunos autores consideran la fase (3 como silicio elemental. Y en este caso la eutéctica estaría formada por α + Si.
No hay más que un punto eutéctico que corresponde a la proporción de 11,6% de Si y cuya temperatura es 577°C.
El silicio endurece al aluminio y, sobre todo, aumenta su fluidez en la colada y su resistencia a la corrosión. Las aleaciones Al-Si son muy dúctiles y resistentes al choque; tienen Un bajo coeficiente de dilatación y una elevada conductividad calorífica y eléctrica, pero son difíciles de mecanizar por la naturaleza abrasiva del silicio. Su peso específico es alrededor del 2,7.
Las propiedades mecánicas de las aleaciones aluminio-silicio pueden mejorarse si se añade a la cuchara de colada de estas aleaciones cloruro sódico o una mezcla de fluoruro y cloruro sódico. Esta operación incorpora una pequeña cantidad de sodio, inferior al 0,01% a la aleación, pero sufriente para variar la concentración eutéctica del 11,6 13% y bajar la temperatura eutéctica de 577°C a 570°C.
Pero sobre todo las aleaciones Al-Si modificadas con esta adición resultan con un grano extremadamente fino en lugar de las agujas o láminas en que cristaliza el silicio en las aleaciones sin “modificar”.
Esta mejora en la estructura micrográfica se traduce en una notable mejora de las propiedades mecánicas de las aleaciones “modificadas” y, concretamente, de su ductilidad, resistencia al choque, resistencia mecánica e incluso de su resistencia a la corrosión.
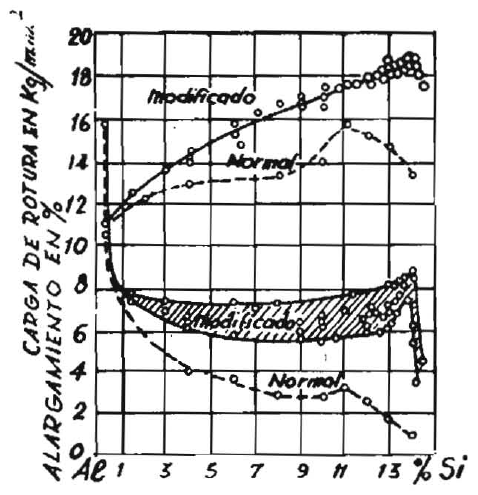
La principal aplicación de las aleaciones aluminio-silicio son la fundición de piezas difíciles, por sus buenas cualidades de moldeo, y la fabricación de piezas para la marina, por su resistencia a la corrosión. Pero no se emplean para piezas ornamentales porque ennegrecen con el tiempo.
7. Aleaciones aluminio-cinc
En estas aleaciones figura el cinc con un porcentaje máximo del 20%. En la gráfica siguiente, se ha representado el diagrama Al-Zn, en el que están presentes la solución sólida α de cinc en aluminio, la solución sólida β de aluminio en cinc, que algunos autores identifican con cinc elemental, y la solución sólida intermedia.
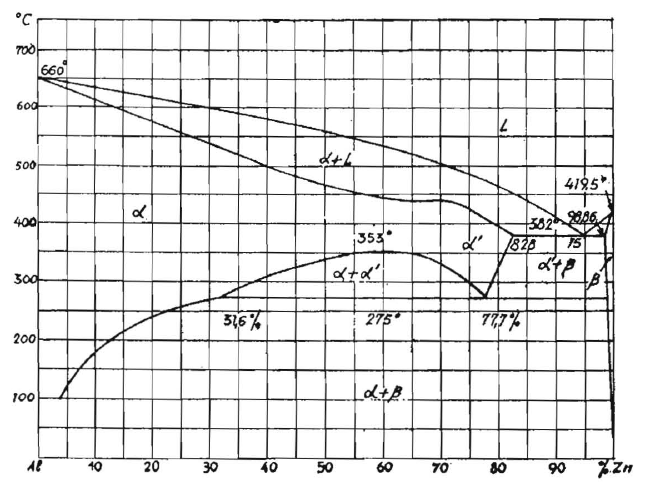
Como no se forman compuestos químicos no puede aplicarse a estas aleaciones el temple de precipitación. Las aleaciones de cinc son más baratas que las de cobre a igualdad de propiedades mecánicas, pero menos resistentes a la corrosión y más pesadas.
8. Aleaciones aluminio-magnesio
Estas aleaciones contienen magnesio en proporciones inferiores al 10% de Mg. En general, el magnesio va asociado a otros elementos como el cobre, silicio, cinc, etc. es decir, formando aleaciones ternarias, en las que el magnesio figura con proporciones del 0,1 al 1%.
En la figura 5 se ha representado el diagrama aluminio-magnesio en el que están presentes la fase α, que es una solución sólida de magnesio en aluminio, y la fase β, que es aluminiuro de magnesio (Al3, Mg2 o, según otros autores, Al8 Mg5).
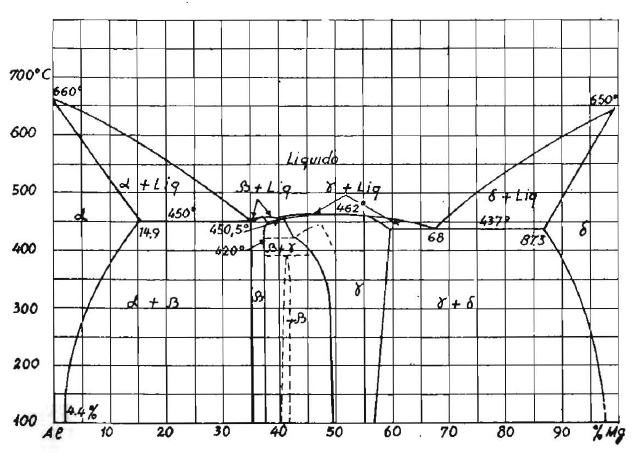
La proporción eutéctica es de 34,5% de Mg y la temperatura eutéctica 450°C. La solubilidad sólida del magnesio en aluminio varía del 4,4% a 250°C hasta 14,9% a 450°C. Por esto las aleaciones Al-Mg admiten el temple de precipitación. Las aleaciones Al-Mg son más ligeras que el propio aluminio, pues su peso específico es alrededor de 2,6. Poseen buenas propiedades mecánicas, se mecanizan con facilidad y tienen una buena resistencia a la corrosión.
9. Aleaciones aluminio-manganeso
El manganeso se encuentra en la mayor parte de las aleaciones de aluminio ternarias y cuaternarias. Su solubilidad en el aluminio pasa del 0,35% a 500°C hasta 1,82% a la temperatura eutéctica, que es 658,5°C. La concentración eutéctica es de 1,95% de Mn. A la temperatura ambiente, y hasta un 25% de Mn la aleación está formada por Al + Al6 Mn. El manganeso aumenta la dureza, la resistencia mecánica y la resistencia a la corrosión de las aleaciones de aluminio.
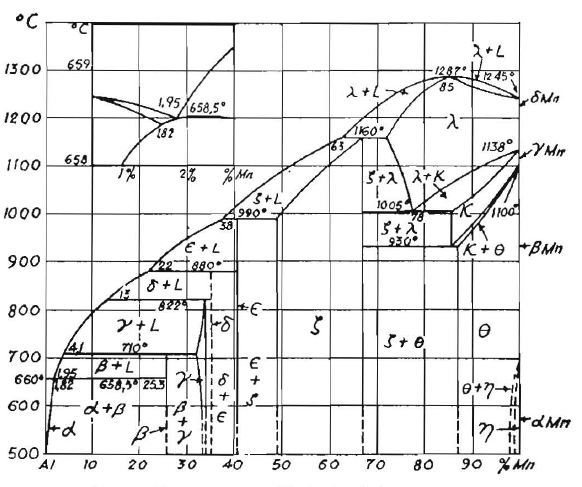
10. Otros elementos de aleación con aluminio
Además de los elementos citados, que son los principales, de aleación con el aluminio, se encuentran formando parte de las aleaciones ternarias y cuaternarias el hierro, el níquel, el titanio, el cromo y el cobalto.
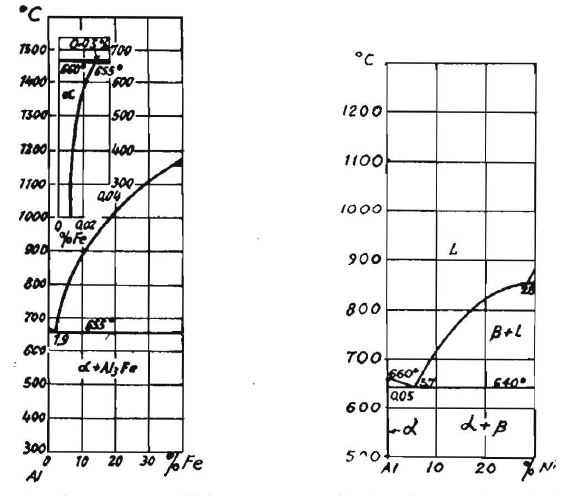
Diagrama de equilibrio aluminio-níquel
Todos estos elementos se encuentran en las aleaciones generalmente en forma de aluminiuros, Al3 F2, Al3 Ni, Al3 Ti, Al7 Cr, Al3 Co, que son insolubles o casi insolubles en la matriz de la aleación.
El hierro, aunque sea en pequeñas proporciones, forma parte de todas las aleaciones incorporado con el aluminio técnico, del que forma siempre parte como impureza, El titanio se adiciona para refinar el grano en las aleaciones con la mejora consiguiente de las propiedades mecánicas, El cobalto endurece las aleaciones. y el níquel y cromo, además de endurecerlas, mejora su resistencia a la corrosión,
Los puntos eutécticos de las aleaciones del aluminio con todos estos elementos están por debajo de la proporción del 1%. Además, en general, pasado el punto eutéctico, la temperatura de iniciación de la solidificación asciende rápidamente.
Por todo esto, ninguno de los elementos citados forma parte de las aleaciones en proporciones superiores al 1%.
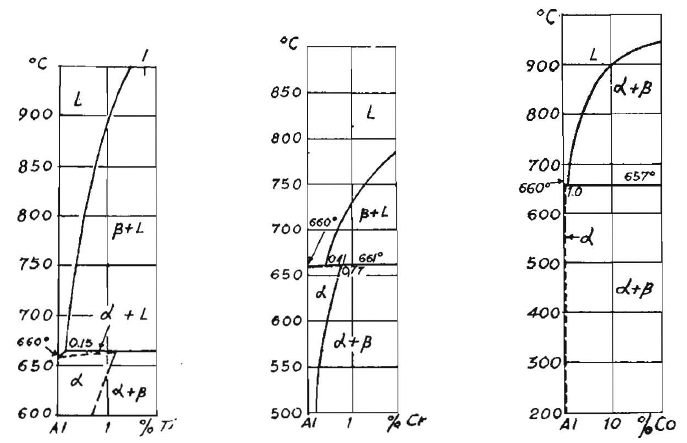
Diagrama de equilibrio aluminio-cromo
Diagrama de equilibrio aluminio-cobalto
11. Aleaciones de aluminio normalizadas
En las normas establecidas, se clasifican las aleaciones en aleaciones ligeras de aluminio para moldeo, que contienen elementos como el silicio que facilita su fusibilidad y aleaciones ligeras de aluminio para forja, que en general contienen menos porcentajes de aleación que las de moldeo.
Entre las aleaciones normalizadas figuran algunas muy conocidas por su nombre comercial, como la L-311, comercialmente denominada duro-aluminio o dur-aluminio, de 95% de Al, 4% de Cu, 0,5% de Mg y 0,5% de Mn, que puede ser templada y adquiere extraordinaria dureza y resistencia mecánica por maduración natural. Precisamente fue este endurecimiento natural del duro-aluminio después de haberlo moldeado, el que condujo al descubrimiento del temple de precipitación y maduración natural y artificial.
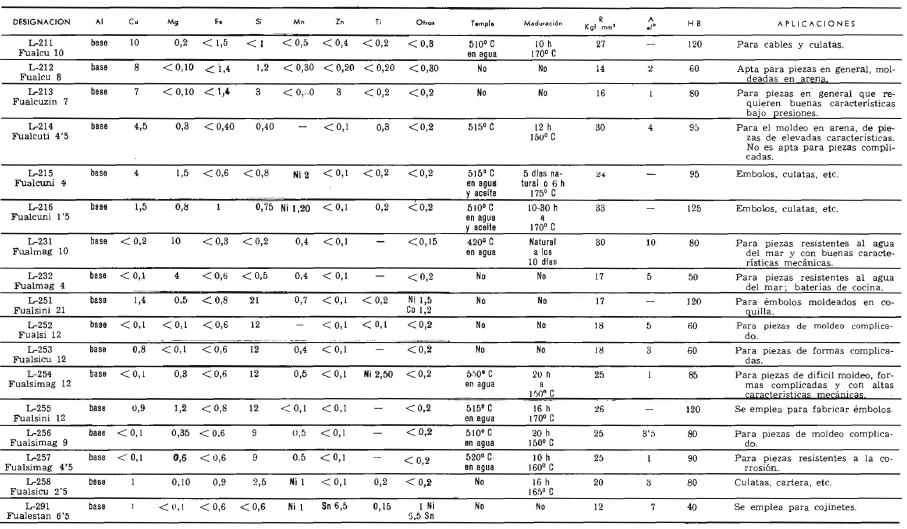
12. Tratamientos anticorrosivos, mecánicos y térmicos del aluminio y sus aleaciones
El aluminio y sus aleaciones pueden someterse a los siguientes tratamientos:
Tratamientos anticorrosivos
Se realizan para dar mayor resistencia a la corrosión del aluminio. El más empleado es la oxidación anódica de que tratamos en otro capítulo, que consiste esencialmente en aumentar el espesor de la película superficial de óxido que se produce naturalmente en el aluminio, mejorando a veces su aspecto dándole un acabado brillante o tiñéndola en diversos colores.
Tratamientos mecánicos
Los trabajos de forja, laminación, trefilado, etcétera, realizados en frío aumentan la resistencia mecánica y dureza del aluminio y de las aleaciones forjables (figura 12), a consecuencia del aumento de acritud adquirido por el material en su deformación. Esto se aprovecha ampliamente en las aleaciones ligeras para mejorar sus características mecánicas.
Tratamientos térmicos
Los tratamientos térmicos que pueden aplicarse al aluminio y sus aleaciones son: El recocido de estabilización, el recocido contra acritud, el recocido de homogeneización, el temple de precipitación y la maduración artificial.
No todos los tratamientos citados pueden aplicarse y se aplican al aluminio y sus aleaciones, pues hay algunas de éstas que no endurecen con el temple.
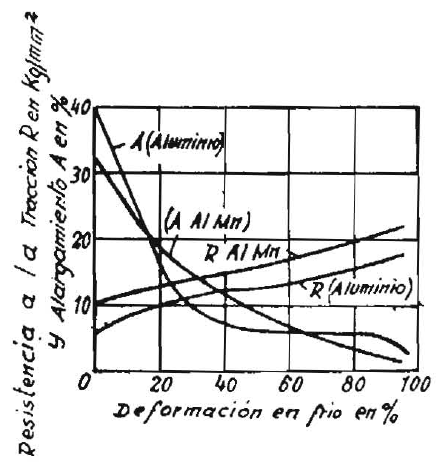
13. Recocido del aluminio y sus aleaciones.
Los recocidos, como ya definimos en su momento, son operaciones de calentamiento y enfriamiento lento para conseguir la constitución y estructura más estable a la temperatura ambiente y destruir, por tanto, cualquier anormalidad en que se encuentre el material producida por tratamientos mecánicos o térmicos. La intensidad de los recocidos depende, sobre todo, de la temperatura máxima a que se llega en el calentamiento. Según sea ésta y clasificados con arreglo a la temperatura y de menor a mayor, se practican con el aluminio los siguientes recocidos:
RECOCIDO DE ESTABILlZACIÓN
Tiene por objeto eliminar tensiones residuales que pueden producirse en el mecanizado o en la conformación en frío o en caliente. La operación se realiza calentando el material a temperaturas inferiores a la de recristalización para que no se modifique su estructura micrográfica. Estas temperaturas varían según las aleaciones. Por ejemplo, las del aluminio de 99,97 oscilan entre 180°C y 210°C. El tiempo de permanencia a estas temperaturas es de unas cuatro horas, exceptuando el tiempo de elevación de la temperatura y el de enfriamiento, que debe ser, sobre todo éste, muy lento para evitar la aparición de nuevas tensiones.
RECOCIDO CONTRA ACRITUD
Tiene por objeto eliminar la acritud adquirida por el material al deformarse en frío o a temperaturas inferiores a la recristalización. Con este tratamiento no sólo recobran los granos deformados su forma poliédrica, sino que también, si la deformación ha sido muy intensa, se rompen los granos y constituyéndose fos fragmentos en núcleos de recristalización se produce una nueva estructura granular más fina. A este fenómeno se conoce con el nombre de germinación. Si la deformación sólo ha sido moderada, no se produce germinación y el material queda con grano poliédrico, pero grueso.
Las temperaturas de recocido contra acritud dependen de la aleación, oscilando en general entre 300°C y 400°C, ya que la temperatura de recristalización a la que debe superarse oscila entre 200°C y 300°C. Es conveniente pasar con rapidez esa zona de temperaturas de recristalización, sobre todo si las piezas no han sido muy deformadas, para evitar un excesivo crecimiento del grano. De todas maneras, si las piezas no han sido muy deformadas, no deben someterse al recocido contra acritud, porque aumentará siempre al tamaño del grano.
El tiempo de permanencia a la temperatura máxima debe ser lo más breve posible y oscilará entre dos y ocho horas, según la aleación, no debiendo sobrepasarse el tiempo máximo señalado de permanencia a la temperatura de recocido, para evitar también el crecimiento del grano. Por esto mismo se aconseja introducir las piezas en el horno, una vez que esté a la temperatura del recocido, para abreviar la duración de la elevación de la temperatura en la pieza.
RECOCIDO DE HOMOGENEIZACIÓN Y REGENERACIÓN
Tiene por objeto uniformar la composición química y el grano de las aleaciones de aluminio que son propensas a heterogeneidad química y estructural.
El recocido se realiza a temperaturas comprendidas entre 450°C y 550°C durante un tiempo comprendido entre 15 y 60 minutos. A estas temperaturas se facilita la difusión de los elementos y la solución de otros como el silicio.
Con este tratamiento se consigue también la regeneración de las aleaciones endurecidas por el temple, anulando los efectos de éste y volviéndolas a su estado natural.
El enfriamiento debe ser lo más lento posible para evitar el temple, que daría lugar posteriormente por maduración natural a un endurecimiento indeseable de la aleación, como ocurre en el duraluminio.
14. Temple de precipitación de las aleaciones de aluminio
Definimos el temple en general como un calentamiento hasta una temperatura adecuada, seguido de un enfriamiento muy rápido para impedir la transformación normal del constituyente obtenido del calentamiento.
En el temple del acero, el constituyente formado en el calentamiento era la austenita, que se transformaba, en enfriamiento normal, en ferrita y perlita (aceros hipoeutectoides), o perlita y cementita (aceros hipereutectoides). Pero si enfriamos bruscamente el acero en estado austenítico, en lugar de formarse los constituyentes normales citados, se forma martensita, que ya vimos que es hierro Q: sobresaturada de carbono, lo que provoca el endurecimiento del acero. Este proceso se conoce como temple martensítico.
Pues bien: si en una aleación de aluminio de solubilidad sólida variable y que forme compuesto químico como, por ejemplo, el duro-aluminio (Al, y 4%de Cu), puesta a temperatura del recocido de homogeneización, para que toda la aleación esté constituida por solución sólida Ci de Cu en Al, se enfría lentamente al atravesar la línea AB del límite de solubilidad sólida total del cobre en el aluminio, empieza a disminuir el porcentaje de cobre disuelto, que al segregar reacciona con el aluminio formando el compuesto químico Al2 Cu, cada vez en mayor proporción hasta un cierto límite.
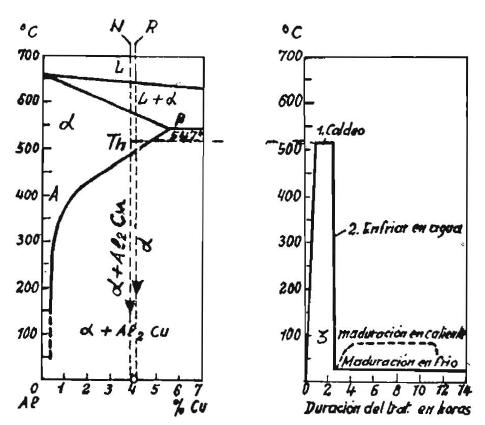
Esquema del proceso de temple de precipitación y maduración en frío y en caliente de una aleación de aluminio templable.
Pero si en lugar de enfriar lentamente desde la temperatura de recocido esta aleación de aluminio, la enfriamos bruscamente (línea R), no se precipita el compuesto químico y queda formada la aleación a la temperatura ambiente casi exclusivamente por solución sólida alfa del elemento aleado, en este caso Cu en aluminio. Este enfriamiento rápido constituye el temple denominado de precipitación. Pero, así como el acero adquiría una gran dureza con el temple, las aleaciones de aluminio, en cambio, una vez templadas, tienen casi las mismas características mecánicas que antes. El endurecimiento se produce después progresiva y más o menos lentamente, pues como la solución sólida obtenida en el enfriamiento brusco es metaestable, a medida que pasa el tiempo se van precipitando diminutas partículas del compuesto químico, que dificulta el movimiento de dislocaciones en los planos de deslizamiento de la solución sólida, lo que trae como consecuencia, el progresivo endurecimiento de la aleación.
Este fenómeno de precipitación se conoce con el nombre de maduración o envejecimiento y dura un tiempo variable, según la aleación. En el duro-aluminio (Al, con 4% de Cu) el endurecimiento es rapidísimo, pero en otras aleaciones llega a durar hasta tres meses. En todos los casos el endurecimiento es más rápido al principio, para hacerse cada vez más lento a medida que pasa el tiempo.
15. Maduración artificial de las aleaciones de aluminio
Si la viscosidad atómica es elevada, no se produce la precipitación del compuesto o se produce muy lentamente a la temperatura ambiente. Entonces se pude acelerar la precipitación con un tratamiento que se conoce con el nombre de maduración artificial o también revenido de endurecimiento, que consiste en calentar la aleación a una tempera inferior a la de temple, con objeto de dilatar las redes cristalinas y facilitar la difusión y precipitación del compuesto químico y abreviar, por tanto, la duración del período de endurecimiento. Este tratamiento, por tanto, tiene efectos contrarios al revenido de los aceros con temple martensítico, que como se recordará, disminuye la dureza y resistencia de los metales templados, en lugar de aumentarla como ocurre con la maduración artificial.
16. Práctica del temple de maduración de las aleaciones de aluminio.
La temperatura de temple es muy similar a la del recocido de homogeneización y oscila alrededor de los 500°C. Para cada aleación existe una temperatura exacta del temple, que no debe variarse, de ± 5%, pues es muy pequeño el intervalo de temperaturas entre la temperatura que debe superarse para conseguir la solución total del elemento en el aluminio y la temperatura que no debe rebasarse para que no se produzca una fusión parcial de la aleación.
La duración de la permanencia a la temperatura de temple varía entre quince minutos y cuatro horas, dependiendo en todo caso del grueso de la pieza y estructura. Así, por ejemplo, la permanencia debe ser mayor para las piezas en bruto de moldeo que para las piezas forjadas.
El enfriamiento del temple se realiza generalmente en agua, y solamente si las piezas son muy delgadas, en aceite, o por pulverización de agua, o en el aire. Cuanto más suave sea el medio de enfriamiento, menos peligro habrá de tensiones residuales, deformaciones y grietas. En todo caso, siguen siendo válidas para este temple las recomendaciones generales sobre la forma de introducir las piezas en los medios de enfriamiento.
La maduración artificial se realiza a temperaturas comprendidas entre 130°C a 165°C, con permanencias de ocho a veinticuatro horas a la temperatura máxima. El método de enfriamiento no tiene importancia y generalmente se realiza al aire, aunque pude enfriarse en agua. Las aleaciones se consideran de maduración natural, cuando tardan en adquirir la dureza máxima menos de cinco días.
La resistencia mecánica obtenida después del temple y maduración es aproximadamente de dos a tres veces la que tenían antes del tratamiento.
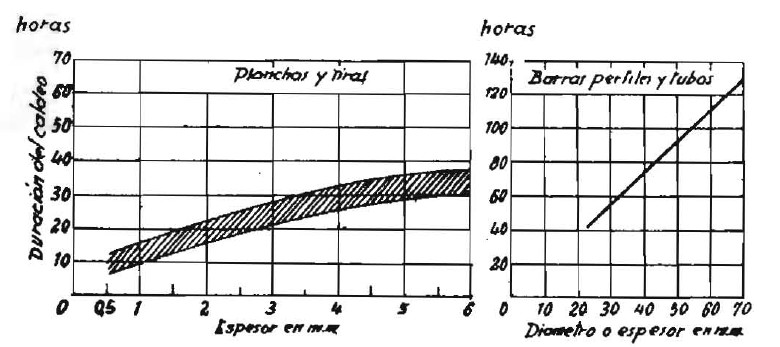
La maduración produce un aumento de volumen que puede ser bastante importante, lo que debe ser tenido en cuenta, sobre todo si las piezas son de maduración natural y, por tanto, el aumento de volumen se produce espontánea y a veces inesperadamente.
CONFORMACIÓN DE LAS PIEZAS TEMPLADAS
La conformación de las piezas templadas, si son de maduración natural, debe realizarse dentro de las dos horas siguientes al temple, y si la conformación ha de ser complicada, se recomienda que se realice antes de los 30 minutos.
De todas maneras, puede detenerse a voluntad la maduración natural conservando las piezas templadas a temperaturas inferiores a 0°C. Los remaches de duraluminio templado se conservan sin endurecimiento apreciable hasta cuatro días en nieve carbónica a temperatura comprendidas entre -6° a-10° C. La conformación de las aleaciones de maduración artificial se realiza también después del temple, dando el tratamiento de maduración una vez adquirida su forma definitiva.
TEMPLE DE PRECIPITACIÓN Y MADURACIÓN ARTIFICIAL DE OTRAS ALEACIONES DISTINTAS DEL ALUMINIO
Como veremos al tratar de las aleaciones de cobre y otras, el temple de precipitación y maduración artificial no se aplica exclusivamente a las aleaciones de aluminio, sino a todas las que están sujetas a cambio de solubilidad sólida con precipitación de compuesto químico, como ocurre con otras aleaciones del cobre, etc.

17. Aplicaciones de las aleaciones de aluminio
Las aleaciones de aluminio tienen cada día una mayor aplicación, utilizándose extensamente para la fabricación de piezas que deben ser resistentes y al mismo tiempo ligeras para las construcciones aeronáuticas, vagones de ferrocarril de trenes articulados modernos, etc. También se emplean para la fabricación de culatas, cárters, bloques y émbolos de motores de explosión.
En la edificación se emplean las aleaciones de aluminio para la construcción de puertas y ventanas, molduras, etc.
En las construcciones navales se emplean ampliamente determinadas aleaciones de aluminio por su resistencia a la corrosión marina.