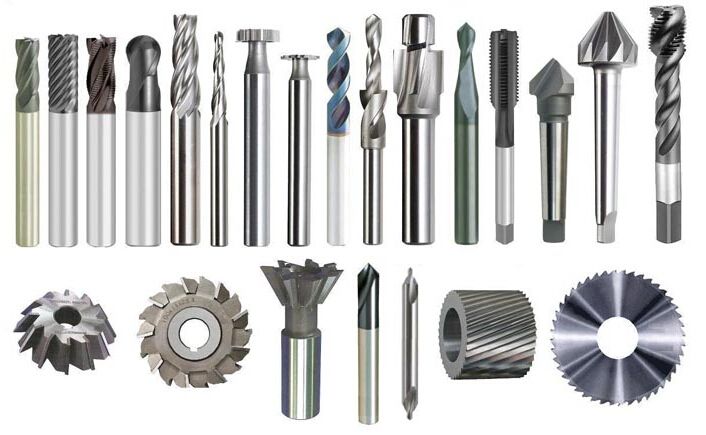
Generalidades
La Industria ha vivido siempre en un continuo desarrollo, que ha generado la necesidad de adecuar los productos necesarios para cada trabajo. Un caso particular de ello es la aplicada a la industria metalúrgica, para las herramientas de trabajo.
Cada tipo de herramienta va a necesitar un tipo de acero y éste, debe ser adecuado a lo que esperamos de ella. Esto es aplicable a toda clase de herramientas, desde las más sencillas, como pueden ser las herramientas agrícolas o las de carpintería, hasta las cuchillas de acero rápido para máquinas herramientas. El conocimiento de los tipos de aceros para herramientas y de sus características, es absolutamente indispensable para lograr mejores tiempos de fabricación, mayores rendimientos en la producción y una más alta productividad en la industria.
Características que interesan en los aceros para herramientas.
Las características mecánicas que en general interesan en los aceros para herramientas son la dureza, la tenacidad, la resistencia al desgaste y, a veces de manera especial, la indeformabilidad.
La dureza es la característica principal que deben poseer los aceros para herramientas. Ésta, principalmente, depende del contenido de carbono y también del temple y revenido a que sean sometidos los aceros. La dureza de los aceros para herramientas varia entre los 30 y 65 HRc, según el porcentaje de carbono y también el temple y revenido empleados.
A veces interesan herramientas que conserven la dureza en caliente para estampación en caliente, etc., que forzosamente habrá que hacer con aceros aleados, pues los aceros al carbono bajan mucho de resistencia mecánica y dureza en caliente.
La tenacidad es una propiedad, en cierto modo, contraria a la dureza. Si se les configura una elevada dureza a las herramientas después del tratamiento, en general resultarán frágiles y si por el contrario, se les da un revenido prolongado a alta temperatura, mejorará su tenacidad a costa de reducir su dureza. Pero puede lograrse también, una buena solución entre ambas propiedades, dureza y tenacidad, atribuyendo una alta dureza en la zona de trabajo de la herramienta, dejando el resto de la pieza con poca dureza y alta tenacidad.
La resistencia al desgaste es interesante también en las herramientas sometidas al roce continua. Esta propiedad podría dar a creer que sólo depende de la dureza, pero no es así, puesto que depende tanto o más de la constitución del material, como sucede con los aceros al cromo, gracias a los granos de carburo.
La no deformabilidad o indeformabilidad, de las herramientas, es sumamente interesante en matricería, en las que las dimensiones deben permanecer lo menos variables posible en los cambios de temperatura. Los denominados aceros indeformables se templan siempre en aceite, lo que origina menos deformaciones que en el agua. Y además, su composición es tal que el aumento de volumen que experimentan al templarse queda a veces totalmente compensado con la contracción del revenido.
Clasificación de los aceros para herramientas
Estos aceros suelen conocerse bajo la denominación «Serie 500 – Aceros para
herramientas«, y se dividen en tres grandes grupos:
- Aceros al carbono: Grupo F-51O.
- Aceros aleados: Grupos F·520. F-530 y F-54O.
- Aceros rápidos: Grupo F-550.
Los aceros al carbono son los que no contienen elementos de aleación. Su contenido en carbono varia entre el 0,50 y el 1,40%, es decir, que continúan la serie de los aceros al carbono de construcción, cuyo máximo contenido de carbono es 0,50 a 0.60%.
Los aceros aleados, contienen porcentajes variables de elementos de aleación según sus aplicaciones. Se suelen clasificar con arreglo a sus aplicaciones en:
- Aceros «indeformables».
- Aceros «resistentes al choque para trabajos en frío».
- Aceros «resistentes al choque para trabajos en caliente».
- Aceros para «herramientas de corte».
- Aceros «resistentes a la corrosión para herramientas» (también conocidos como «inoxidables») .
Los aceros rápidos se emplearon al principio exclusivamente para cuchillas de máquinas herramienta, pero actualmente se fabrican también con ellos, brocas, fresas, escariadores, etc. La característica principal que distingue y da superioridad a los aceros rápidos sobre los demás aceros es la conservación del filo a temperaturas cercanas a los 600°C, mientras que, las mejores herramientas de aceros “no rápidos” no pueden trabajar a más de 250°C.
En su composición pueden incluirse porcentajes variables de wolframio y cobalto.
Podríamos clasificar a los aceros de herramientas en cuatro grandes grupos:
- Aceros no aleados.
- Aceros aleados para trabajo en frío.
- Aceros aleados para trabajo en caliente.
- Aceros rápidos.
Los aceros no aleados, obviamente, son los que no contienen elementos de aleación. Su contenido en carbono varia del 0,65 al 1,50%.
Los aceros aleados para trabajo en frío contienen porcentajes variables de aleación según sus aplicaciones. Estos aceros se clasifican en cinco grupos:
- Aceros «resistentes al desgaste«
- Aceros «indeformables«
- Aceros «resistentes al choque«
- Aceros «para grabado por deformación en frío«
- Aceros «resistentes a la corrosión, para herramientas«
Aceros no aleados para herramientas.
Los contenidos de carbono en los aceros al carbono para herramientas varían entre el 0,50 y el 1,40%, dependiendo de la proporción de carbono la dureza y la aplicación específica de cada tipo.
En los aceros no aleados para herramientas, lo mismo que ocurre con los aceros no aleados para construcción, a medida que aumenta el porcentaje de carbono aumenta también la dureza y resistencia mecánica y disminuye la tenacidad, o sea, la resiliencia. Esto ocurre en cualquier estado, en bruto de laminación, normalizados, templados y recocidos. El contenido máximo de manganeso en los aceros no aleados para herramientas es del 0,35%. Cuanto mayor es el contenido de Mn, mayor es la templabilidad y, por tanto, serán mejores las características obtenidas en el temple y el revenido.
Aceros resistentes al desgaste
Los aceros resistentes al desgaste tienen la ventaja de que se mecanizan mejor que los aceros indeformables. manteniendo un grado medio de indeformabilidad, dureza y resistencia al desgaste. Se templan a una temperatura de 800° a 860°C, alcanzando una dureza de 60 HRc. Dentro de este grupo consideramos los aceros: F-5230, F-5233 y F-5237.
Aceros indeformables
Los aceros denominados “indeformables” son muy utilizados para la fabricación de troqueles, fresas, etc., pues interesa que sufran las mínimas deformaciones posibles en el tratamiento térmico. La indeformabilidad de estos aceros es en gran parle debida a su elevada templabilidad, que permite templarIos en aceite o en aire.
Otra cualidad de los estos aceros es su gran resistencia al desgaste, debida a la presencia de carburos en su estructura. La dureza media obtenida es estos aceros es de 60-61 HRc.
Podemos clasificarlos en seis tipos de aceros indeformables:
- Aceros F-5212, al 12% de Cr.
- Aceros F-5220, al Cr-Mn.
- Aceros F-5227. F-5 211 y F.5214, al Cr-Mo.
- Aceros F-52J3, al Cr-W.
Los aceros F-5212. al 12% de Cr, son muy poco deformables, por poseer muy alta templabilidad. Su resistencia al desgaste es unas seis veces mayor que la de los aceros al carbono. Como su contenido de cromo es relativamente elevado, son en cierto modo resistentes a la corrosión, conservándose las herramientas fabricadas con ellos siempre brillantes. El inconveniente de estos aceros es que, el mecanizado, aún recocidos, se realiza con dificultad, y que la temperatura de temple es muy elevada (960°-1.000°C).
Cabe destacar que, los aceros F-5220, al Cr-Mn, son muy económicos, con un valor poco superior al de los aceros al carbono. Son los más deformables y los más resistentes al desgaste. Tienen, en cambio, la ventaja de que la temperatura de temple es relativamente baja (770 °-810°C), y que, en estado de recocido se mecanizan fácilmente. Además, el pequeño porcentaje de cromo que poseen (0,35-0,65%) aumenta su templabilidad y dureza, y el wolframio (0,50%) eleva la temperatura límite del crecimiento del grano.
Aceros resistentes al choque
Los aceros agrupados bajo esta denominación se emplean para la fabricación de buriles, buterolas, etc. Las características que interesan en este tipo de acero son una elevada tenacidad combinada con una buena dureza.
Los aceros especialmente adecuados para estos trabajos son los aceros al Cr-W y Cr-Mo, cuya tenacidad es extraordinaria, aún a la máxima dureza.
Podemos seleccionarlos en tres tipos:
- F-5241, de O,40-0,50% de C, 1,70-2,30% de W y 0,90-1,20% de Cr, que, templado de 880° a 920°C en aceite, y revenido de 160° a 210°C al aire, queda con una dureza de 56 HRc.
- F-5242, de 0,55-0,65% de C, 1,70-2,30% de W y 0,90-1,20% de Cr, que templado de 870° a 910°C en aceite, y revenido de 160° a 210°C al aire, queda con dureza de 57 HRc.
- F-5247 acero al Cr-Mo, de 0,55-0,62% de C, 0,30-0,50% de Mo y 0,20-0,35% de Cr, que templado de 860° a 900°C en aceite, y revenido de 160° a 210°C al aire, queda con dureza de 58 HRc.
Aceros para trabajos en caliente
Se considera que una herramienta trabaja en caliente cuando su temperatura de trabajo se eleva por encima de los 200°C.
Entre las herramientas para trabajar en caliente pueden citarse, las dedicadas a la fabricación en serie de tornillos, remaches, bulones, etc. Otras herramientas que trabajan en caliente son las estampas para fabricación de piezas de automóviles y, de aviones, como bielas, cigüeñales, discos de turbinas, etc., así como los rodillos para máquinas enderezadoras.
Para la fabricación de herramientas que deban trabajar a altas temperaturas, se utilizan cuatro tipos de aceros, principalmente:
- Aceros al carbono.
- Aceros de media aleación.
- Aceros bajos en wolframio.
- Aceros altos en wolframio.
Aceros al carbono.
Son los que contienen porcentajes de carbono del 0,50 al 0,90%, y se utilizan para determinados trabajos, como, por ejemplo, para la fabricación de grandes matrices que no se han de emplear en grandes series, para las que el precio hace prohibitivo el empleo de aceros especiales.
También se emplean los aceros al carbono para la fabricación de moldes para fundición en coquilla de aleaciones de cinc y aluminio de bajo punto de fusión, y siempre que no se trate de grandes series.
Pero para trabajos de responsabilidad o grandes series se emplean los aceros de “media aleación”, “bajos en wolframio” y “altos en wolframio”.
Aceros de media aleación para trabajos en caliente
La superioridad de los aceros de media aleación sobre los aceros al carbono se debe a su templabilidad, la cual es mucho mayor. Esto tiene dos ventajas:
- La obtención de resistencias mucho más elevadas en piezas de gran espesor.
- La templabilidad en aceite, lo cual, reduce mucho las deformaciones y evita casi totalmente la formación de grietas. En general, estos aceros son de un contenido de carbono superior al 0,40%, para lograr obtener mayor resistencia en el temple.
Se emplean con éxito a temperaturas de hasta de 400°C.
EL I.H.A, selecciona dos tipos de aceros de media aleación para trabajos en caliente:
- F-528 al Cr-Ni-Mo, con 0.40 al 0,50% de C, 0,60 al 0,75% de Cr, 1,30 al 1,70% de Ni y 0,30 al 0,60% de Mo, Que después del templado a 850° – 875°C en baño de aceite y revenido a 600°C al aire, queda con una dureza de 40 a 50 HRc.
- F-529 al Cr, que contiene de 0,5 al 0,60% de C y de 0,50 a 1% de Cr, con el que se obtiene, templado a 820°C en aceite y revenido a 550° – 600°C, una dureza de 32 a 37 HRc.
Aceros bajos en wolframio para trabajos en caliente
El acero F-527, pertenece a este tipo de aceros, que tienen un porcentaje de wolframio de 3.75 a 4,25%. Contienen también de 1 a 2% de Cr y de 0,20 a 0,30% de Mo, siendo su contenido en carbono de 0.30 a 0,40%.
Estos aceros se utilizan y dan buenos resultados en trabajos a temperaturas de hasta 450°C. Además, resisten mejor los choques que los aceros altos en wolframio.
Aceros altos en wolframio para trabajos en caliente
De estos aceros podemos destacar el acero F-526, de 0,30-0 ,40% de C, 9,50 a 10,50% de W, 2,50 a 3% de Cr y 0,20 a 0,50 % de V.
Estos aceros son los que conservan la dureza y resistencia a más elevadas temperaturas. Por ello, son los empleados para la fabricación de cuchillas de corete en caliente, herramientas para prensas y, en general, para herramientas que han de trabajar a temperaturas superiores a los 500°C, además de a grandes presiones.
No tienen, en cambio, mucha tenacidad, y por eso no se aconsejan para emplearlos en herramientas que han de sufrir fuertes y repetidos choques.
Aceros aleados para herramientas de corte
Incluimos en este epígrafe los aceros aleados empleados para herramientas de corte en el más amplio sentido de la palabra.
Estos aceros se emplean para fabricar brocas, escariadores, cuchillas para máquinas herramientas y también para la fabricación de limas.
El contenido de carbono de los aceros aleados para herramientas de corte oscila entre 0,60 y 1,40%, o sea, que es el mismo que el de los aceros al carbono para herramientas.
Sus características son también parecidas, aunque mejoradas por la adición de los elementos de aleación, principalmente por el cromo, wolframio, molibdeno y vanadio.
- El cromo afina el grano, mejora su templabilidad, y sus carburos la resistencia al desgaste.
- El wolframio a fina también el grano, mejora las cualidades de corte, sobre todo en caliente, y aumenta su resistencia al desgaste. El molibdeno mejora la templabilidad.
- El vanadio afina el grano.
Podemos destacar cuatro aceros con estas características:
Aceros de gran dureza para herramientas
F-531: de 1,25 a 1,50% de C, 3,50 a 4,50% de W y 0,40 a 0,60% de Cr.
- El vanadio es opcional. Este acero, una vez tratado, queda con una gran dureza de 60 a 65 HRc y con una gran resistencia al desgaste, que es cuatro o cinco veces mayor que la del acero al carbono del mismo porcentaje.
- Se emplea para la fabricación de hileras para estirar en frío y cuchillas de corte para trabajos realizados a altas velocidades con pasadas pequeñas
- El recocido se realiza a 800°C, debiendo enfriar a menos de 10°C por hora hasta 600°C.
- Se templa de 800°C a 850°C en agua, pues es de poca penetración de temple, salvo piezas muy pequeñas, que pueden enfriarse en aceite.
- El revenido se verifica ordinariamente entre los 200°C a 300°C, enfriando al aire.
Aceros al WOLFRAMIO para brocas
F-532: de 1,10 a 1,20% de C y 0,90 a 1,10% de W.
- Es éste un acero clásico para la fabricación de brocas, fresas, terrajas, etc., con el que se obtiene, tras el tratamiento térmico, durezas comprendidas entre los 60 y los 65 HRc.
- Se templa el agua, pero se fabrica una variante con 0,70% de Cr, que se templa en aceite.
- El recocido del acero F-532 se verifica a 780°C, enfriando a 10°C por hora hasta los 600°C.
- El temple se efectúa a 800°C, enfriando en agua, el revenido, de 150° a 225°C, enfriando al aire.
Aceros al CrOMO para limas
F-533: Este acero es una variable del acero al carbono clásico para la fabricación de limas, que es el F-517, de 1,20 al 1,40% de C, que contiene además de 0,50 a I% de cromo. Este porcentaje de cromo mejora su templabilidad, y al penetrar más el temple, aumenta ligeramente la dureza obtenida, que siempre supera los 62 HRc y que, además, es más uniforme en toda la lima.
- El recocido se realiza a 780°C enfriando a 10°C hasta los 600°C.
- El temple se efectúa de los 780°C a los 800°C, es decir, a 20°C más que para el F-517, debido al cromo.
- El revenido, para eliminar tensiones principalmente se efectúa de 150 °C a 225°C, enfriando al aire.
Aceros semirrápidos para herramientas
F·534: de 0,65 a 0,75% de C, de 9 a 11% de W y 3,5 a 4,5% de Cr.
- Estos aceros son casi aceros rápidos, que pueden trabajar en cuchillas de corte para máquinas herramienta a grandes velocidades.
- Se forjan de 900°C a 1100°C, enfriándolos después entre cenizas para evitar que templen.
- El recocido se efectúa a 875°C, enfriando en el horno a 10°C/hora hasta los 600°C.
- Se templan a 1150°C, enfriando en aceite, salvo piezas muy pequeñas que puedan enfriarse al aire.
- El revenido se recomienda a 450°C a 500°C, enfriando al aire.
Los calentamientos de estos aceros son muy lentos porque el coeficiente de transmisión del calor es inferior al de los demás aceros, debiendo durar casi el doble de tiempo. La elevación de temperatura para la forja y temple debe hacerse en dos etapas, una hasta 800°C, con una detención suficiente para uniformar la temperatura en toda la pieza y otra, a la temperatura máxima, permaneciendo en ella las piezas el menor tiempo posible. Conviene utilizar atmósfera controlada para evitar descarburaciones superficiales.
Aceros resistentes a la corrosión para herramientas de corte
F-535: de 13 a 14% de Cr. En realidad, este acero es prácticamente idéntico al F-312.
Aceros grafíticos
Estos aceros, son excelentes para la fabricación de calibres, troqueles, etc., dónde interesa a veces el empleo de un acero que tenga grafito libre, que actúa como lubricante, favorece el deslizamiento y mejora el aspecto de las superficies.
El grafito, además, hace más fácil la mecanización, pues la viruta salta y rompe con más facilidad, reduciéndose el tiempo de mecanizado en hasta un 25%.
La presencia de grafito libre se consigue con la inclusión de una proporción del 1%, aproximadamente, de silicio, o hasta un 0,20% de aluminio, y dando después al acero un tratamiento térmico adecuado. El porcentaje de carbono es más elevado que lo normal, puesto que parte de él ha de quedar separado en forma de grafito.
En general, se emplea una proporción del 1,50% de carbono, quedando aproximadamente 0.90% (composición eutectoide) como elemento aleado, y el resto, o sea, 0,60%, como carbono grafitado.
La grafitación se obtiene calentando el acero por encima de la temperatura crítica, o sea, de 750°C a 825°C, y enfriando muy lentamente. Una vez precipitado el grafito, se someten las piezas al temple y revenido, como se hace con cualquier otro acero.
Pueden formar parte de los aceros grafíticos el cromo, molibdeno, wolframio, níquel y manganeso, consiguiéndose tipos de aceros grafiticos similares a los indeformables o a los de gran resistencia al desgaste.
Aceros rápidos
Los aceros al carbono y la mayoría de los aceros aleados para herramientas tienen el gran inconveniente de que se ablandan y desafilan a temperaturas superiores a 250°C, lo que limita la velocidad de corte de las herramientas que se fabrican con ellos.
En cambio, los aceros denominados rápidos (desarrollados por Taylor y White en 1898), trabajan a temperaturas hasta de 600°C conservando su dureza y filo inicial. Esto permite una velocidad de trabajo mucho mayor que la de los demás aceros, y de ahí su nombre de “aceros rápidos”.
Composición de los aceros rápidos.
Los aceros rápidos contienen en proporción relativamente elevada tres elementos de aleación fundamentales: el wolframio, el cobalto y el molibdeno, y dos elementos accesorios el cromo y el vanadio.
- El wolframio mejora la resistencia de la martensita en caliente y aumenta la resistencia al desgaste.
- El molibdeno es de una acción similar a la del wolframio, pero más intensa, teniendo el mismo efecto una parte de molibdeno que dos de wolframio. Tiene el inconveniente de bajar el punto de fusión del acero y de aumentar su tendencia a la descarburación.
- El cobalto mejora la resistencia en caliente del acero y eleva su temperatura de fusión. Aumenta también la tendencia a la descarburación del acero.
- El cromo favorece la formación de carburos, aumenta la templabilidad del acero y su resistencia a la oxidación a elevada temperatura.
- El vanadio mejora la resistencia de la martensita y aumenta la resistencia al desgaste.
- El carbono forma parte de los aceros rápidos en proporciones elevadas de 0.65 al 0.85%, con objeto de obtener en el temple gran dureza, y además, el carbono necesario para la formación de los carburos, a los que deben sus extraordinarias cualidades de resistencia al desgaste.
Tipos de aceros rápidos
Hay dos clases principales de aceros rápidos: los aceros rápidos al wolframio y los aceros rápidos al cobalto.
Aceros rápidos al wolframio
Contienen fundamentalmente del 13 al 19% de wolframio, del 3.75 al 4.50% de cromo, del 1 al 1.25% de vanadio y del 0.65 al 0,80% de carbono.
Podemos destacar dos clases de aceros de este tipo:
- F-551: denominado acero rápido al 14% de W.
- F-552: denominado acero rápido al l 18% de W.
El primero se utiliza para la fabricación de herramientas de perfiles finos, como herramientas para tornear, cepillar, fresar, taladrar, etc. El acero rápido al 18% de W se utiliza para herramientas destinadas a trabajos pesados de desbaste.
Aceros rápidos al cobalto
También denominados extrarrápidos, contienen del 4 al 11% de caballo, del 17 al 19% de wolframio y del 0,80 al 1% de molibdeno.
Podemos destacar dos tipos:
- F-553: denominado acero extrarrápido al 5% de Co.
- F-554: denominado acero extrarrápido al 10% de Co.
El primero se utiliza para cuchillas de corte de alta velocidad, para máquinas herramientas y para fabricar brocas, escariadores, machos de roscar, etc. El segundo es el acero de mayor rendimiento de corte, pero no debe utilizarse para herramientas finas por su alta temperatura de temple.
Durante la segunda guerra mundial, y debido a la escasez de wolframio, se ensayó la sustitución de parte del porcentaje de este metal por molibdeno, obteniendo los denominados aceros rápidos al molibdeno. Aun cuando las cualidades de corte son parecidas a los aceros al wolframio, su fabricación y tratamientos son muy delicados, y por ello, en desuso.
Forja y tratamientos térmicos de los aceros rápidos
Las temperaturas de la forja y tratamientos térmicos de los aceros rápidos son bastante más elevadas que las de los aceros al carbono. Además, los calentamientos de los aceros rápidos deben hacerse más lentamente, aproximadamente a la mitad de velocidad que, para los aceros al carbono, pues la transmisión del calor a través de la masa de acero se hace más difícilmente.
También la permanencia a las temperaturas limites debe ser más prolongada. Los calentamientos de forja y temple que deben llegar a temperaturas superiores a los 1.000°C, se aconseja hacerlo en dos fases. Una primera fase hasta 800°C, manteniendo las piezas a esta temperatura dos minutos por cada milímetro de diámetro o espesor, subiendo después a la temperatura final.
Este sistema tiene por objeto uniformar toda la temperatura del acero a los 800°C, para reducir todo lo posible el tiempo de permanencia de la pieza a temperaturas elevadas, en las cuales existe un evidente peligro de crecimiento anormal del grano y de quemar las aristas vivas.
También se recomienda la utilización de atmósfera controlada para evitar descarburaciones superficiales.
La forja de los aceros rápidos se realiza a 1.200°C o, iniciándose con golpes suaves hasta que toda la superficie haya sido recalcada. Después se puede martillar más fuertemente mientras que el acero esté por lo menos a 900°C.
AI terminar la forja, debe enfriarse el acero en horno o entre cenizas, pues si se deja enfriar al aire adquiere temple.
El recocido de los aceros rápidos se realiza a temperaturas de entre los 850°C y los 900°C, bajando de una dureza de 600 Brinell a unos 250 Brinell. Como los aceros al cobalto tienen tendencia a oxidarse mucho y a descarburarse, se deben de recocer en hornos de atmósfera controlada o en cajas de carbón vegetal muy seco, en trozos de unos 5mm. o con viruta de fundición. Las cajas se cierran con arcilla para conseguir su perfecta estanqueidad.
La velocidad de enfriamiento debe ser inferior a los 10°C/hora hasta los 600°C, pudiendo luego enfriar al aire. Si se enfría más rápidamente quedará el acero parcialmente templado.
Se emplea también el recocido isotérmico, consistente, en calentar a la temperatura de recocido (850° a 900°C), manteniendo esta temperatura de dos a cinco minutos por milímetro de espesor.
Después se pasan las piezas a otro horno, que permanece a una temperatura constante de 700° a 750°C. Al cabo de dos horas, se saca la pieza y se enfría al aire.
El temple se realiza a temperaturas muy elevadas, de unos 1.250°C, cercanas al punto de fusión, para conseguir la dilución de los carburos.
El calentamiento se aconseja que se realice en dos etapas: primero se calienta hasta 850°C, manteniendo el material en esta temperatura hasta que se uniforme en toda la masa.
Después se eleva a los 1.200° – 1.250°C durante unos treinta segundos a diez minutos, según el tamaño de la herramienta.
La temperatura de temple debe ser superior a los 1.200°C, pues si calienta a más baja temperatura (por ejemplo, a 1.100 °), la martensita que se forma es blanda. Pero tampoco conviene sobrepasar la temperatura límite, pues a partir de una temperatura determinada, según la composición de los aceros, queda al templar mucha austenita residual y la estructura resulta también blanda.
Se emplean mucho los hornos de baño de sales con calentamiento eléctrico, lo que evita la formación de cascarilla y descarburación. El enfriamiento se realiza en aceite o al aire, según el acero y la herramienta. En herramientas de forma complicada se enfría primero en sales a 550°C y después al aire, con el fin de evitar deformaciones.
El revenido debe realizarse inmediatamente después del temple, a 525°C – 580°C, según el acero, con una duración de dos horas por cada 25mm. de espesor de la herramienta; y enfriando después al aire. Es conveniente dar un segundo revenido a una temperatura de 10 a 20°C más baja que el primero.