CLASIFICACIÓN DE LOS ACEROS COMUNES
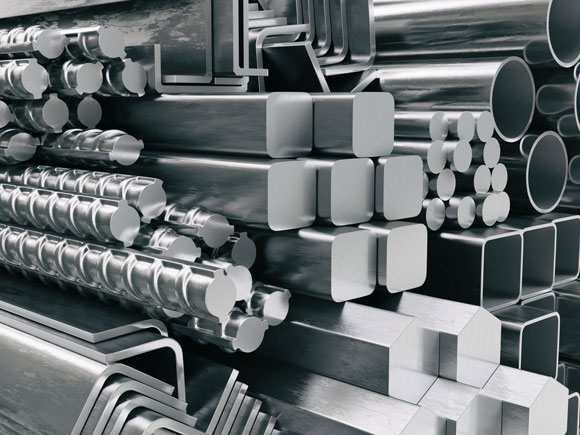
1. Clasificación de las aleaciones hierro-carbono atendiendo a su porcentaje de carbono
Se denomina acero, a toda aleación hierro-carbono forjable cuyo contenido de carbono está generalmente comprendido entre 0,10 y 1,76%. Se denomina fundición, a toda aleación hierro-carbono no forjable y cuyo contenido de carbono es generalmente de 2,5 a 4%. Estas definiciones son exactas salvo casos muy especiales, pues hay aceros aleados que contienen hasta un 2,5 % de carbono y también hay fundiciones que son forjables. Se denomina hierro, al metal de este nombre técnicamente puro, o con un contenido de carbono inferior a 0,03 %. El hierro se puede obtener casi puro por un procedimiento electrolítico, pero tiene pocas aplicaciones industriales.
Cabe destacar, por su resistencia a la corrosión, el denominado hierro Armco, que es un tipo de hierro ideado por la «American Rolling Mili Co.» (A.R.M.C.O.) y que se obtiene en hornos Martin-Siemens básicos, a temperaturas superiores a las normales y con arreglo a una técnica patentada.
El hierro Armco es de una gran pureza, que puede compararse a la del hierro electrolítico.

Las propiedades mecánicas medias del hierro Armco son:
R = 28 Kg/mm2 a 32 Kg/mm2 A = 25 % a 35 %
2. Clasificación de los aceros atendiendo a su procedimiento de fabricación
Según el procedimiento de fabricación, se clasifican los aceros en aceros Bessemer, aceros Thornas, aceros Siemens (en Francia e Italia se denominan más frecuentemente los aceros Siemens, aceros Martin), aceros eléctricos, aceros al crisol y hierros pudelados (aunque en realidad son aceros de bajo contenido de carbono).
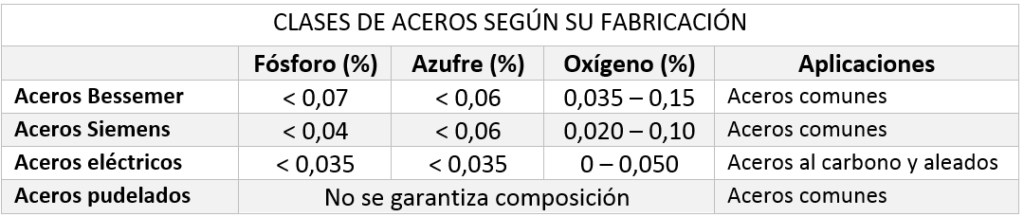
3. Clasificación de los aceros atendiendo al porcentaje de carbono
Se denominan aceros hipoeutectoides a los aceros cuyo porcentaje de carbono es inferior al de punto S (eutectoide); eutectoides, si su porcentaje de carbono es igual al del punto S. y se denominan hipereutectoides, si su porcentaje de carbono es superior al del punto S.
El punto S corresponde para los aceros al carbono a un porcentaje de 0,89 % de C, pero puede variar en los aceros aleados.
4. Clasificación de los aceros atendiendo al grado de des-oxidación
Como hemos visto anteriormente, pueden obtenerse dos clases de aceros, según el grado de des-oxidación que se consiga en el afino. Los aceros calmados son los que se han desoxidado por completo y al solidificarse no desprenden gases.
Los aceros efervescentes son los que se han desoxidado incompletamente y al solidificarse desprenden abundantes gases que producen numerosas sopladuras. Estos aceros sueldan bien en la forja y tienen cualidades muy apreciables para el trabajo de embutición profunda. Como la capa exterior de los lingotes es de bajo contenido de carbono y de gran dureza, se obtiene después del laminado una superficie sin defectos que los hace particularmente aptos para la fabricación de chapa fina para neveras, carrocerías de automóviles, etc. Estos aceros, sin embargo, son de características mecánicas inferiores a los aceros calmados y muy sensibles al envejecimiento, aumentando su fragilidad con el tiempo. Por todas estas razones, salvo para las aplicaciones citadas, los aceros utilizados son del tipo calmado.
5. Clasificación de los aceros atendiendo a su constitución
También pueden clasificarse los aceros con arreglo a la constitución con que quedan después de enfriarse al aire tras un calentamiento a elevada temperatura. En las piezas de mucho espesor, puede suceder que la constitución no sea uniforme en el enfriamiento al aire, puesto que siendo la velocidad de enfriamiento del núcleo de las piezas gruesas mucho más lenta que la de la periferia, es posible que al enfriar al aire quede el núcleo con una constitución distinta.
La clasificación se podrá hacer sin reservas, haciendo constar que se refiere a la constitución de los aceros de un diámetro máximo de 25mm o el redondo equivalente en perfiles de otra sección, calentados hasta la austenización completa y enfriados al aire. Con arreglo al constituyente predominante con que quedan los aceros en las condiciones antes dichas, se acostumbra a clasificarlos en:
- aceros perlíticos
- aceros martensíticos
- aceros austeníticos
- aceros ferríticos
- aceros con carburos
Aceros perlíticos
Los aceros perlíticos se caracterizan por estar constituidos a la temperatura ambiente después de un enfriamiento normal desde el estado austénico, por perlita y ferrita o perlita y cementita, según que su porcentaje de carbono sea inferior o superior al eutectoide. Son los aceros que pudiéramos denominar normales. Pertenecen a este grupo los aceros al carbono y además los aceros de baja y media aleación.
Aceros martensíticos
Los aceros martensíticos quedan constituidos después del enfriamiento al aire desde su estado austenítico, en su mayor parte por martensita. En realidad, se trata de aceros perlíticos cuya velocidad de temple es muy lenta y, por tanto, quedan templados con enfriamiento al aire. Estos aceros se denominan también de autotemple. Pertenecen a este grupo los aceros al cromo-níquel, de 0,35% de C, 1% de Cr y 4% de Ni, y cromo-níquel-molibdeno, de 1% de C, 1,25% de Cr y 0,35% de Mo, y los resistentes a la corrosión, de 0,30% de C y 30% de Cr.
Aceros austeníticos
Los aceros austeníticos son los que, enfriados desde elevada temperatura, generalmente superior a 900°C, quedan constituidos en su mayor parte por austenita a la temperatura ambiente. Pertenecen a este grupo los aceros cromo-níquel, resistentes a la corrosión de 18% de Cr, 8% de Ni, y de 12% de Cr, 12% de Ni, etc., y también el acero de 12% de Mn. Como el hierro gamma de la austenita no es magnético, se reconoce fácilmente su estado austenítico porque no son atraídos por el imán. Si las piezas son muy gruesas, se enfrían en agua o en aceite para que la velocidad de enfriamiento sea más rápida, lo que favorece la obtención de la austenita.
Aceros ferríticos
Los aceros ferríticos son los que están formados principalmente por ferrita a cualquier temperatura. Es decir, que estos aceros no pueden templarse porque no alcanzan el estado austenítico por calentamiento y, por tanto, el estado martensítico en el enfriamiento. Pertenecen a este grupo los aceros de bajo contenido de carbono, inferior a 0,30%, y elevado contenido de cromo, superior al 16%, y algunos aceros al 3% o más de silicio.
Aceros con carburos
Los aceros con carburos se caracterizan por contener un porcentaje de carburos de elementos de aleación muy superiores al que se considera como normal en los aceros al carbono. La temperatura de temple de estos aceros es más elevada, en general de 950°C a 1.300°C, para conseguir la dilución de los carburos. Pertenecen a este grupo los aceros rápidos, los aceros indeformables, entre otros.
6. Clasificación de los aceros atendiendo a su composición
Según sea su composición, se pueden dividir los aceros en dos clases fundamentales: aceros al carbono y aceros aleados.
Se ha convenido en designar como aceros al carbono aquéllos que están formados fundamentalmente por hierro y carbono, no siendo los porcentajes de otros elementos superiores a los límites expresados en el cuadro indicado más abajo.
Los aceros aleados son los que contienen, además del carbono e impurezas, elementos de aleación voluntaria, como cromo, níquel, molibdeno, vanadio, wolframio, etc. Estos elementos influyen de muy diversas maneras en las propiedades de los aceros, aumentando o disminuyendo la templabilidad, la dureza, la maquinabilidad, etc.
Delimitación de las clases del acero no aleado y acero aleado
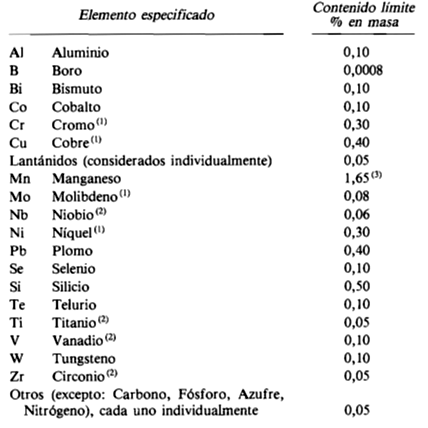
(2) Para estos elementos se aplica la misma regla dada en (1).
(3) Cuando el manganeso está definido sólo por un máximo, el valor límite es 1,80%.
Para una mejor comprensión de las características de los aceros aleados, de las que trataremos en el capítulo siguiente, examinaremos a continuación la influencia no sólo de los elementos aleados, sino de todos los elementos que puede contener el acero además del hierro y el carbono, tanto como elemento de aleación deseable como indeseable en forma de impurezas, de inclusiones, etc. Estos elementos son los siguientes:
- Elementos que pueden beneficiar al acero: aluminio, azufre, boro, circonio, cobalto, cobre, cromo, fósforo, manganeso, molibdeno, niobio, níquel, nitrógeno, plomo, selenio, silicio, titanio, vanadio y wolframio.
- Elementos que perjudican al acero: antimonio, arsénico, estaño, hidrógeno y oxígeno.
7. Influencia de los elementos de aleación que benefician al acero
Agruparemos los elementos de aleación con arreglo a sus propiedades y, en general, por orden de mayor a menor influencia.
Elementos que aumentan la dureza de los aceros
El fósforo, níquel, silicio, aluminio, cobre y cobalto se encuentran siempre disueltos en la ferrita, lo que se traduce en un endurecimiento de ésta y aumento también de dureza en el acero.
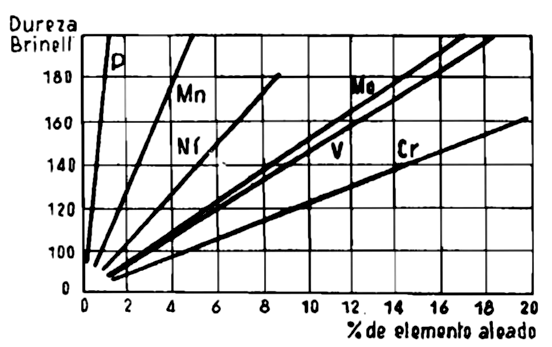
El manganeso, cromo, wolframio, molibdeno, vanadio y titanio tienen tendencia a formar carburos, pero en los aceros de bajo contenido de carbono se disuelven y endurecen la ferrita y el acero.
Elementos que aumentan la dureza de los aceros y la conservan a altas temperaturas
EI titanio, vanadio, molibdeno, wolframio, cromo y manganeso forman carburos si el porcentaje de carbono del acero es suficiente. Estos carburos son muy duros y resistentes al desgaste, propiedades que conservan a altas temperaturas cercanas a los 500°C y que, por tanto, comunican al acero.
De estos carburos, los de cromo y vanadio son los más duros y resistentes al desgaste, y los de molibdeno, wolframio y vanadio, los más estables a altas temperaturas.
Elementos que modifican los puntos críticos
El níquel, el manganeso y el cobre tienden a bajar los puntos críticos A1 y A3, mientras que el molibdeno, aluminio, vanadio, wolframio y silicio tienden a elevar los puntos críticos. El cromo tiende a elevarlos en los aceros de alto contenido de carbono y a bajarlos en los de bajo contenido.
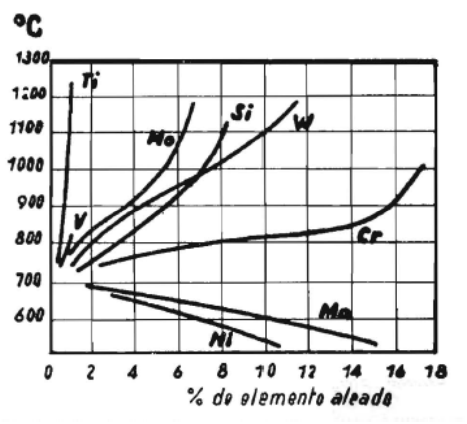
Cuando se encuentran varios elementos aleados con el mismo acero, sus influencias se suman si son del mismo signo, o se restan si son del sentido contrario.
Elementos que modifican los puntos Ms y Mf del principio y fin de la transformación de la austenita en martensita.
El manganeso, el cromo, el níquel, el molibdeno y el wolframio bajan los puntos Ms y Mf casi proporcionalmente a su porcentaje de aleación. A pesar de ello, es el porcentaje de carbono el que más influencia tiene en la posición de los puntos Ms y Mf.
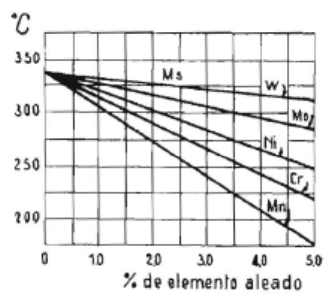
Elmentos que modifican el porcentaje de carbono del acero eutectoide.
El titanio, molibdeno, wolframio, silicio, manganeso, cromo y níquel, en orden de importancia, reducen el porcentaje de carbono del acero eutectoide.
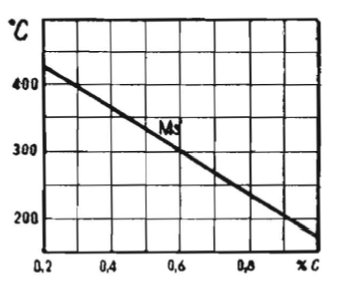
Elementos que influyen en el campo austenítico
El níquel y el manganeso tienden a ampliar el campo austenítico. En cambio, el cromo, el silicio, molibdeno, aluminio y vanadio disminuyen el campo austenítico y favorecen la formación de estructuras ferríticas.
Elementos que influyen en el tamaño del grano
El titanio, vanadio y aluminio limitan el crecimiento del grano de la austenita. El titanio y el vanadio, formando carburos, y el aluminio, formando partículas de alúmina, que constituyen centros de cristalización.
Elementos que influyen en la templabilidad
EI manganeso, el molibdeno y, en menor proporción, el cromo, el silicio y el níquel aumentan la templabilidad de los aceros. En cambio, el cobalto hace que la templabilidad disminuya.
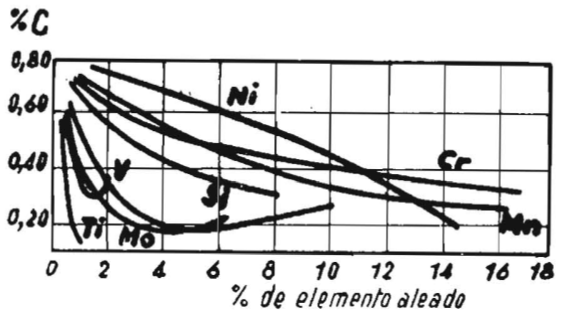
Elementos que influyen en el revenido
El cromo, el molibdeno y el wolframio dificultan el ablandamiento de los aceros en el revenido.
Elementos que influyen en la resistencia a la corrosión
El cromo favorece la resistencia a la corrosión de los aceros, y el molibdeno y el wolframio, la resistencia a la oxidación.
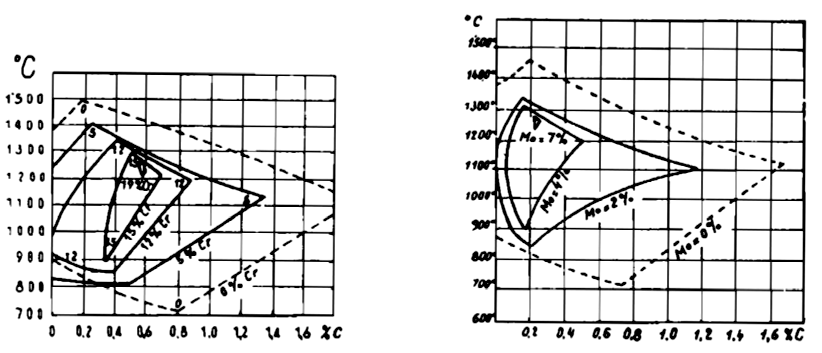
Influencia del porcentaje de molibdeno en el campo austenítico del diagrama de equilibrio de los aceros.
8. Influencia de los elementos que perjudican al acero
Los elementos de cuya influencia hemos tratado en el parágrafo anterior, aunque pueden perjudicar a veces las propiedades del acero, se emplean como elementos de adición voluntaria con un determinado fin. Pero hay otros elementos que no son deseables por ningún concepto y que, por tanto, su presencia en los aceros se considera siempre como una impureza de origen accidental. Estos elementos son principalmente los siguientes:
Antimonio. El antimonio llega al acero aportado por la chatarra que puede contener restos de metal de antifricción, etc. el antimonio produce un aumento de fragilidad a partir de porcentajes de 0,50%.
Arsénico. Procede también de contaminación de la chatarra, generalmente.
En proporciones hasta el 1% aumenta la resistencia y el límite elástico, disminuyendo en mayor proporción la estricción y la resiliencia. Con porcentajes superiores al 0,8 %, aumenta los fenómenos de envejecimiento del acero, ya partir del 0,25 % disminuye su soldabilidad.
Estaño. El estaño se incorpora a los aceros por la chatarra que interviene en su fabricación y que contiene soldaduras, metales de antifricción, etc. El estaño aumenta la fragilidad del acero en caliente, siendo su acción parecida a la del fósforo, pero 4 veces más intensa.
Hidrógeno. Casi todos los aceros contienen hidrógeno en proporciones muy pequeñas, de 0,0003% y a veces inferior.
A la presencia del hidrógeno se atribuyen grietas en la forja y otros accidentes.
Se conoce como fragilización por hidrógeno a la pérdida de ductilidad causada por la entrada de hidrógeno en un material metálico, como, por ejemplo, durante el decapado o la electrólisis.
Un procedimiento que da buen resultado para eliminar el hidrógeno por completo es calentar el acero a altas temperaturas durante un tiempo suficiente.
Oxígeno. También la presencia del oxígeno en los aceros aleados en muy perniciosa, empleándose principalmente aluminio y silicio para desoxidarlos en el curso de su fabricación.
Los aceros que contienen pequeñas cantidades de oxígeno en forma de óxido de hierro son más fáciles de trabajar en corte y perforado que los aceros totalmente desoxidados.
9. Tabla de tipificación de los aceros del Instituto del Hierro y del Acero (ahora Centro Nacional de Investigaciones Metalúrgicas)
Como es la tabla de aceros del Instituto Español del Hierro y del Acero (Centro Nacional de Investigaciones Metalúrgicas), que ordena los aceros atendiendo a sus aplicaciones, muy utilizada en España, y nos vamos a referir a ella constantemente en la descripción de los tipos de aceros que haremos en los capítulos siguientes, juzgamos necesario y de interés una relación completa de la misma.
El Instituto del Hierro y del Acero clasificó los materiales metalúrgicos en cinco clases:
- F: Aleaciones férreas.
- L: Aleaciones ligeras.
- C: Aleaciones de cobre.
- V: Aleaciones varias.
- S: Productos sinterizados.
A su vez, la clase de las aleaciones férreas se divide en 9 series:
- F-100: Aceros finos de construcción general.
- F-200: Aceros finos de usos especiales.
- F-300: Aceros resistentes a la oxidación y corrosión.
- F-400: Aceros de emergencia (1).
- F-500: Aceros para herramientas.
- F-600: Aceros comunes.
- F-700: Aceros para moldear.
- F-800: Fundiciones.
- F-900: Aleaciones férreas especiales.
(1)-En posteriores ediciones de la Tabla de Tipificación de los aceros finos de construcción del I.H.A. se suprimió la serie F-400 de Aceros de emergencia, por lo que no la tendremos en cuenta en lo sucesivo.
Cada una de estas series se subdivide a su vez en grupos, según la clasificación siguiente:
SERIE F-IOO – ACEROS FINOS DE CONSTRUCCIÓN GENERAL
- Grupo F-100: Aceros al carbono (para construcción, de piezas que no exijan elevadas características).
- Grupo F-120 y 130: Aceros aleados de gran resistencia (para piezas de alta resistencia).
- Grupo F-140: Aceros de gran elasticidad (para construcción de muelles, ballestas, etc.).
- Grupos F-150, F-160: Aceros para cementar. Grupo F-170: Aceros para nitrurar.
SERIE F-200 – ACEROS PARA USOS ESPECIALES
- Grupo F-21O: Aceros de fácil mecanización (al azufre y al plomo).
- Grupo F-220: Aceros de fácil soldadura.
- Grupo F-230: Aceros de propiedades magnéticas (para chapas de transformadores y para imanes).
- Grupo F-240: Aceros de alta y baja dilatación.
- Grupo F-250: Aceros resistentes a la fluencia.
SERIE F-300 – ACEROS RESISTENTES A LA OXIDACIÓN Y CORROSIÓN
- Grupo F-31O: Aceros inoxidables.
- Grupo F-320: Aceros para válvulas de motores de explosión.
- Grupo F-330: Aceros refractarios.
SERIE F-400 – DE ACEROS DE EMERGENCIA
- Grupo F-410 y 420: Aceros de alta resistencia.
- Grupo F-430: Aceros para cementar.
SERIE F-500 – ACEROS PARA HERRAMIENTAS
- Grupo F-51O: Aceros al carbono para herramientas.
- Grupo F-520, 530, 540: Aceros aleados para herramientas (indeformables, para trabajos de choque en frío y en caliente, para corte no rápido, e inoxidable para corte).
- Grupo F-550: Aceros rápidos (rápidos y extrarrápidos al cobalto).
SERIE F-600 – ACEROS COMUNES
- Grupo F-61O: Aceros Bessemer.
- Grupo F-620: Aceros Siemens.
- Grupo F-630, 640: Aceros para usos particulares.
Posteriormente haremos hincapié en la descripción de los tipos de aceros más característicos de cada grupo, indicando sus utilizaciones más adecuadas y los tratamientos térmicos a que deben someterse para obtener de ellos las mejores propiedades.
A continuación, trataremos de las características de los aceros comunes, también denominados ordinarios, algunos de cuyos tipos son conocidos vulgarmente con el nombre de hierros comerciales.
10. Aceros comunes
Los aceros comunes se fabrican, en general, en convertidores Bessemer o en hornos Siemens, no garantizándose una composición muy exacta y conteniendo además bastantes impurezas.
Su contenido de carbono varía, en general, entre 0,1 y 0,7%; el manganeso, entre 0,35 y 0,80%; el silicio, entre 0,1 y 0,3%, y su contenido de fósforo y azufre son inferiores al 0,10%.
Serie F-600 – Aceros comunes
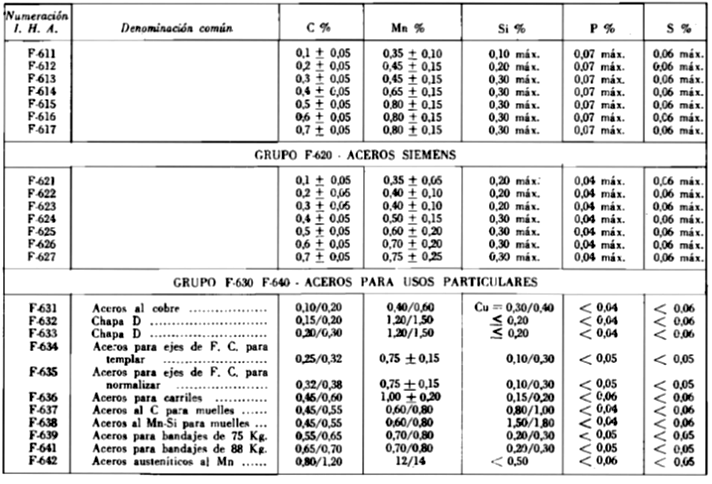
Estos aceros se destinan, en general, a la construcción de estructuras metálicas de edificios, a la construcción de chapas para industria naval, a la construcción de material móvil y fijo de ferrocarriles, etc.
Se utilizan, salvo algunos de los tipos particulares, en estado bruto de forja o de laminación, y sus características son similares a las de los aceros al carbono normalizados, de los que trataremos en el capítulo siguiente.
La dureza y resistencia de estos aceros crece con el contenido de carbono, siendo muy parecidas las de los aceros obtenidos en convertidores Bessemer a la de los aceros obtenidos en hornos Martin-Siemens.
Sus aplicaciones son las siguientes:
- Aceros F-611 y F-621 (0,1% C): Tubos soldados y sin soldadura, alambre, llanta, chapa, hojalata, clavos, tornillos, etc. Son fácilmente soldables.
- Aceros F-612 y F-622 (0,2% C): Material para construcciones, puentes, traviesas, flejes, perfiles y hierros comerciales, etc. Estos tipos son los conocidos vulgarmente con el nombre de hierros comerciales, y son la calidad corriente, de la que se fabrican los redondos para el armado del hormigón, los angulares, doble T, etc. Son fácilmente soldables.
- Aceros F-613 y F-623 (0,3% C): Placas de asiento, bridas, elipses, escarpias y piezas de forja en general. Son medianamente soldables.
- Aceros F-6140 y F-624 (0,4% C): Carriles pequeños y medianos, bridas, alambres para cable. Se fabrican también ejes y discos para ruedas de vagones, preferentemente con el F-624. Son poco soldables.
- Aceros F-615 y F-625 (0,5% C): Carriles pequeños, bandajes, ejes para locomotoras, material para muelles que no han de soportar grandes esfuerzos. Poco soldables.
- Aceros F-616 y F-626 (0,6% C): Muelles, tensores, resortes. Preferentemente, con el F-626, carriles grandes y cilindros forjados. No soldables.
- Aceros F-6170 y F-627 (0,7% C): Herramientas útiles diversas, carriles, proyectiles. No soldables.
Las aplicaciones principales de los aceros para usos particulares quedan especificadas en su denominación común.
De la utilización de los aceros F-637 y F-638 trataremos más adelante.
El acero F-642, que se denomina en la clasificación “acero austenítico al manganeso”, es similar al conocido como “acero Hadfield”, muy resistente al desgaste y cuyas interesantes características conviene detallar.
11. Acero Hadfield
El acero clásico resistente al desgaste es el acero Hadfield, denominado así en recuerdo de su descubridor, que figura con el número F-642 en la clasificación de I.H.A. El acero Hadfield contiene del 0,80 al 1,20% de C y del 12 al 14% de Mn. Es austenítico y no es atraído, por tanto, por los imanes.
Este acero no posee gran resistencia (unos 100 Kg/mm2), pero, en cambio, tiene, cuando está perfectamente austenizado, un alargamiento excepcionalmente elevado, del orden de 45%, al que se atribuye su resistencia al desgaste.
Para conseguir una austenización completa se calienta de 1.000° a 1.100°C y luego se enfría en agua.
El acero Hadfield conserva sus buenas cualidades a temperaturas elevadas hasta de 800°C, no variando sus características, independientemente de la velocidad de enfriamiento, lenta o rápida, desde esa temperatura. Tiene el inconveniente de que es muy difícil de mecanizar, pues se endurece en cuanto se trabaja con cualquier herramienta. Por eso se construyen las piezas moldeadas, rectificando después los pequeños defectos. El acero Hadfield, también llamado acero austenítico al manganeso, se emplea mucho para la fabricación de bolas y placas de revestimiento para molinos, cruzamientos de vías, etc., y, en general, para todas las aplicaciones en que se desea mucha resistencia al desgaste combinada con muy buena tenacidad.
12. Estado y forma de suministro de los aceros comunes
Los aceros comunes se suministran normalmente en bruto de forja o laminación o en estado de recocido. En casos especiales podrán suministrarse los aceros normalizados o con temple y revenido. El material se suministra generalmente en forma de “semi elaborados” o “semiproductos” y en forma de “acabados”. Los productos de cada tipo normalizados en España son los siguientes:
SEMIELABORADOS
- Lingote: producto bruto de colada, destinado a ser transformado ulteriormente por forja o laminación.
- Desbaste: producto obtenido por una primera laminación o forja del lingote. Puede ser de sección cuadrada o rectangular. Su espesor está comprendido entre 130 y 350mm, y anchura entre 130 y 550 mm (inclusive).
- Palanquilla: barra de sección aproximadamente cuadrada y aristas redondeadas, cuyo lado está comprendido entre 40 y 125mm.
- Llantón: producto de sección rectangular, cuyo espesor está comprendido entre 10 y 125mm, y la anchura, entre 200 y 600mm (inclusive).
ACABADOS
- Plano ancho: producto de sección rectangular, cuyo espesor está comprendido entre 4 y 10mm, y la anchura, entre 200 y 600mm.
- Llanta: producto de sección rectangular, cuyo espesor es superior a 10mm, sin llegar a 130mm, y cuya anchura está comprendida entre 100 y 200mm.
- Pletina: producto de sección rectangular, cuyo espesor está comprendido entre 4 y 10mm, y la anchura, entre 10 y 200mm.
- Fleje: producto laminado de sección rectangular, cuyo espesor es inferior a 4mm y cuya anchura no pasa de 200mm.
- Chapa: producto laminado de anchura superior a 600mm, o que, cualesquiera que sean sus dimensiones superficiales, tenga forma irregular.
- Chapa fina: es la de espesor inferior a 3mm.
- Chapa media: es la de espesor superior a 3mm, inclusive, e inferior a 6mm.
- Chapa gruesa: es la de espesor superior a 6mm, inclusive.
- Redondo: producto de sección circular, cuyo diámetro está comprendido entre 5 y 200mm.
- Cuadrado: producto de sección cuadrada, cuyo lado está comprendido entre 8 y 100mm.
- Pasamano. Producto cuya sección es un segmento de círculo con ángulos redondeados. Además de los pasamanos corrientes, existen otros de formas complejas.
- Medio-redondo: Producto cuya sección es un semicírculo con ángulos vivos y cuyo radio está comprendido entre 10 y 25mm.
- Angular de lados iguales: Se caracteriza por dos alas de igual anchura que forman un ángulo de 90°. Sus dos caras exteriores se unen en ángulo vivo y la arista interior es redonda. Los bordes de las alas terminan en aristas vivas por el exterior y generalmente redondeadas por el interior.
- Angular de lados desiguales. Perfil análogo al anterior, pero con alas de anchura diferente.
- Vigas: Producto cuya sección tiene forma de 1. La unión de las dos caras del alma a las caras interiores de las alas es redondeada. Los bordes de las alas terminan en arista viva por su exterior, y generalmente redondeadas por su interior.
- Perfil en U: Perfil cuya sección tiene forma de U. La unión del alma con las caras interiores de las alas es redondeada, así como el borde interior de éstas.
- Perfil en T: Producto cuya sección tiene forma de T. Las dos caras del ala presentan una pequeña inclinación. El extremo de esta es redondeado, así como las uniones con las alas y las aristas interiores de éstas.
- Hexagonal: Producto cuya sección es un hexágono regular definido por su doble apotema, que está comprendido entre 5 y 70mm.
- Carriles: Producto de sección especial que presenta, en general, una superficie de apoyo (patín) y otra de rodamiento (cabeza).
13. Tabla de Aceros con designaciones de 4 cifras
Al revisar la Tabla de Aceros del I.H.A., para incluir nuevos tipos ya normalizados en otros países, se llegó a la conclusión que se debía reestructurar, y designar los aceros con 4 cifras, lo que ofrecía mayor capacidad de clasificación, dando además a cada acero una designación simbólica.
Iniciaremos esta exposición con las reglas generales en que se basan ambas designaciones, la numérica y la simbólica. A continuación, figura una relación con la composición química de los aceros especiales ya normalizados.
DESIGNACIÓN NUMÉRICA
Los aceros en esta tabla se designan numéricamente con una F seguida de 4 cifras. De estas cifras, y a efectos de clasificación, sólo son significativas las dos primeras.
La primera cifra indicará grandes grupos de acero, reservándose las cifras 1, 2, 3, 4 y 5 para los aceros especiales. Las cifras 6 y 7 se reservan para los aceros de uso general y la cifra 8 para los aceros moldeados.
La segunda cifra se reserva para designar subgrupos afines dentro de cada grupo. Las dos cifras restantes sólo tienen la misión de diferenciar un tipo de otro, aplicándose a medida que van siendo normalizados los aceros y en orden cronológico. En esta tabla se ha procurado que los aceros de las mismas características que los de las tablas anteriores, lleven la misma designación seguida de un O. Así, por ejemplo, el acero F-111 del I.H.A. se designa en la tabla F-1110. Reservando las últimas cifras diferentes de cero para los nuevos tipos que se establezcan.
DESIGNACIÓN SIMBÓLICA
Además de la designación numérica de 4 cifras, se distinguen los aceros en la tabla por una designación simbólica que se establece de acuerdo con:
- Su composición química.
- Sus características de utilización.
ACEROS DESIGNADOS SIMBÓLICAMENTE POR SU COMPOSICIÓN QUÍMICA
Se designan simbólicamente por su composición química los aceros cuya composición los define perfectamente, como son los aceros especiales, que a efectos de la designación se dividen en cuatro grupos:
- Aceros no aleados.
- Aceros aleados con menos de 5% de elementos de aleación.
- Aceros aleados con más del 5% de elementos de aleación.
- Aceros para usos generales, aleados y no aleados.
Aceros especiales no aleados.
Se designan con la letra C, seguido de su porcentaje medio de carbono multiplicado por 100. Así, por ejemplo, el acero F-1130 se designa C35, lo que indica que es un acero especial no aleado con 0,35% de carbono.
Aceros especiales aleados con menos de 5% de elementos de aleación.
Se designan por el porcentaje de carbono, multiplicado por 100, seguido del símbolo químico, o símbolos de los elementos que se consideren básicos para definir el acero, ordenados de mayor a menor, por su porcentaje, y terminando la designación con los productos de los porcentajes de los elementos de aleación citada, por los factores del cuadro n.O 4, redondeando este producto por encima o por debajo, si la primera cifra decimal es superior o inferior a 5. Si los elementos de aleación son más de uno, los productos se deben dar en dos cifras, y si alguno no tiene más que una, debe figurar con un cero delante. Finalmente, pueden añadirse los símbolos de los elementos, cuyo contenido no se especifica, pero, sin embargo, son indispensables para que el acero tenga las características deseadas. Normalmente, no se expresa el porcentaje de los elementos si no es superior al indicado en el siguiente cuadro:
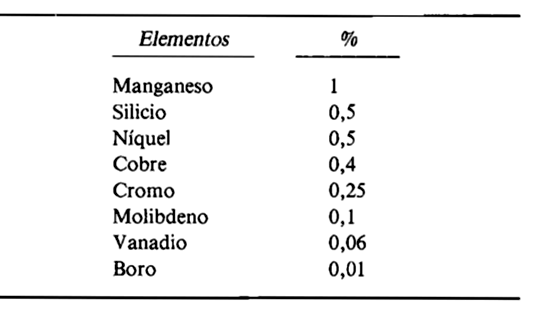
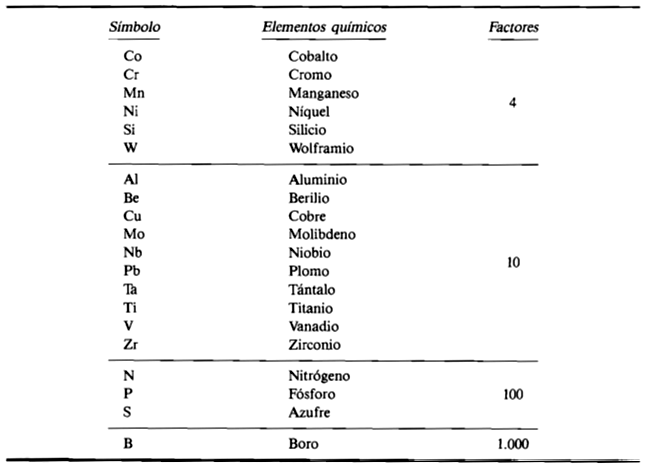
Así, por ejemplo, el acero F-1251 se designa por 30CrMo4, lo que indica que es un acero aleado de menos de 5% de elementos de aleación con un porcentaje medio de carbono de 0,30% y de cromo de 4/4=1% y que contiene también molibdeno.
Aceros especiales aleados con más de 5% de elementos de aleación.
Se designan con una X, seguido por el contenido medio de carbono multiplicado por 100, seguido de los símbolos químicos de los elementos de aleación, y de su porcentaje en dos cifras, y si alguno es de una cifra figurará con un cero delante. Así, por ejemplo, el acero F-3517 se designa por X12CrNi17-07, lo que indica un acero especial aleado, con más de 5% de elementos de aleación, con un porcentaje de carbono de 0,12%, de cromo de 17% y de níquel de 7%.
Aceros no aleados para usos generales.
Se designan simbólicamente por su porcentaje de carbono multiplicado por 100 y por su porcentaje de manganeso multiplicado por 40, tomando de este producto solamente las dos primeras cifras, y sumando a la segunda una unidad, si la tercera es mayor que 5. Se intercala entre ambas cifras la letra Q. Así, el acero F-7201 se designa simbólicamente como 6Q18, lo que indica que se trata de un acero no aleado de usos generales con un porcentaje medio de carbono de 0,06% y 0,045% de manganeso.
Aceros aleados para usos generales.
Se designan como los aceros especiales aleados, anteponiendo a la designación la letra Q.
ACEROS DESIGNADOS SIMBÓLICAMENTE POR SUS CARACTERÍSTICAS DE UTILIZACIÓN O PROPIEDADES FÍSICAS
Las características que sirven de base para la designación de estos tipos de aceros son:
- Su resistencia a la tracción.
- Su límite elástico.
- Otras características particulares.
Aceros designados por su resistencia a la tracción
Se designan estos aceros por la letra A, seguido de su resistencia mínima a la tracción expresada en Kp/mm2. Si lleva algún elemento de aleación se añade a continuación su símbolo químico.
Aceros designados por su límite elástico
Se designan estos aceros por las letras AB, seguidas del valor mínimo de su límite elástico expresado en Kp/mm2.
Designación del estado de desoxidación en la designación simbólica de los aceros
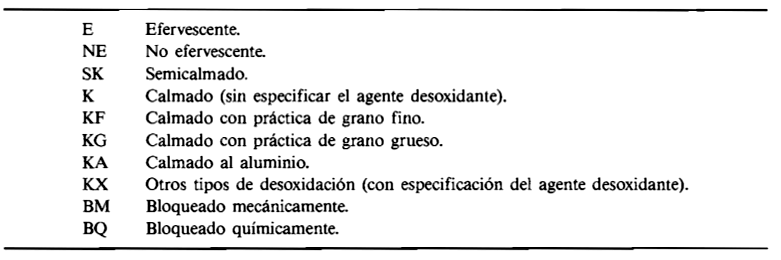
Aceros designados por sus características particulares
Los aceros que se considera conveniente designarlos por sus características particulares se simbolizan por la letra A, seguida de la letra que indica su característica (W para las características magnéticas; P, para las de embutición), seguidas por un número que indica la aptitud del acero para dicha característica.
SÍMBOLOS GENERALES QUE DESIGNAN CARACTERÍSTICAS ESPECÍFICAS
Se emplean a continuación de la designación simbólica de los aceros que hemos descrito otros símbolos que indican:
- Su estado de desoxidación, de acuerdo con el código del cuadro visto anteriormente.
- Su estado de pureza, concretada en el porcentaje de azufre y fósforo que contiene el acero, que se simboliza de acuerdo con el cuadro siguiente.
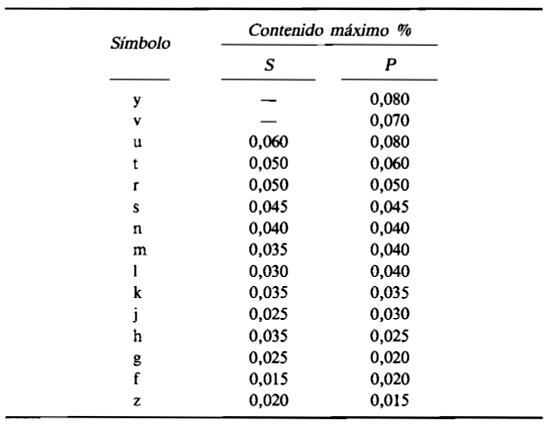
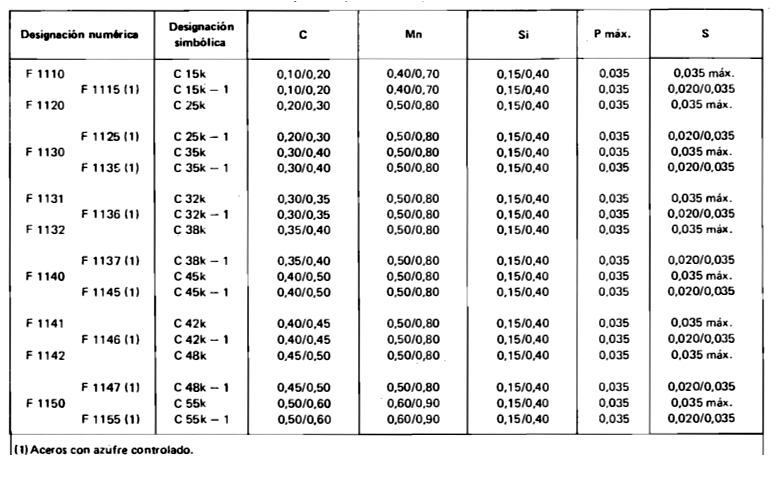
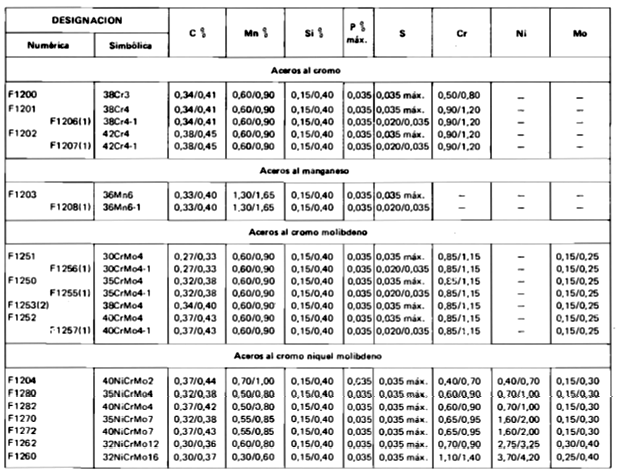
(2) Aceros de uso no preferente.
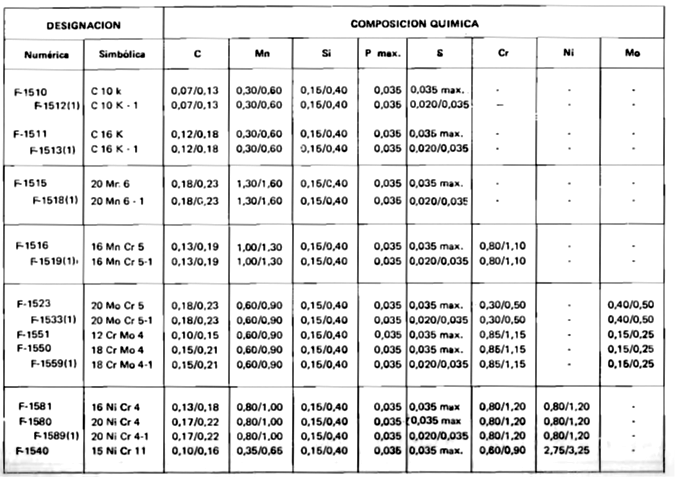
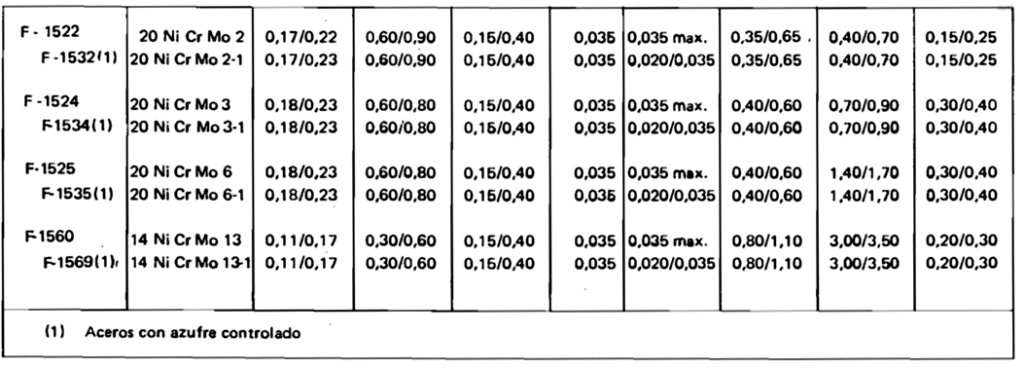
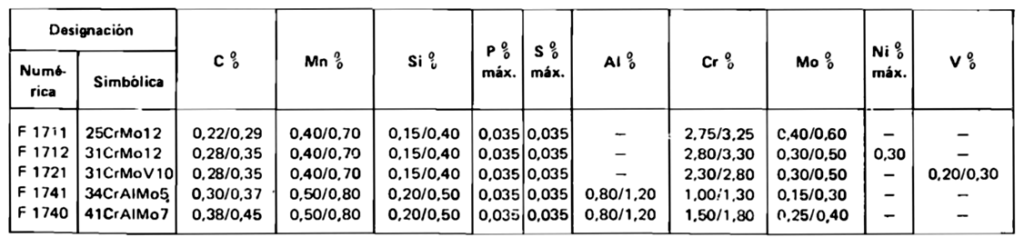
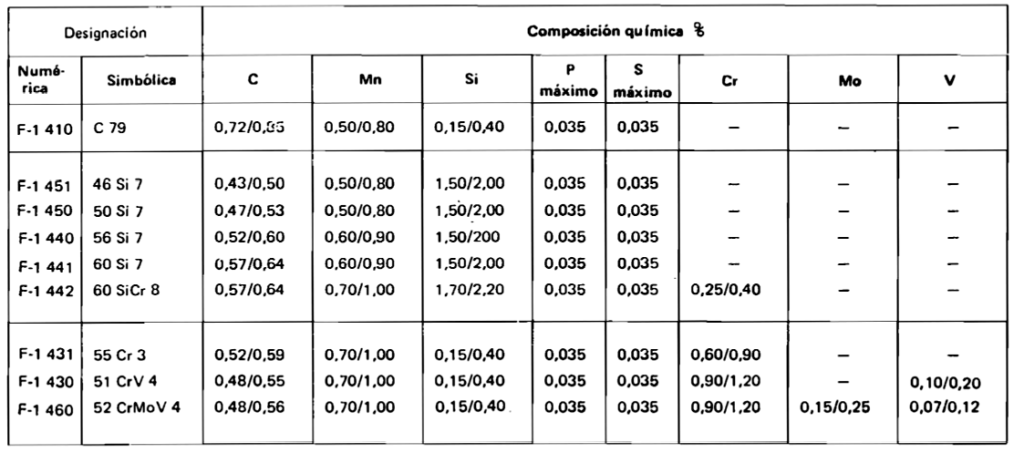
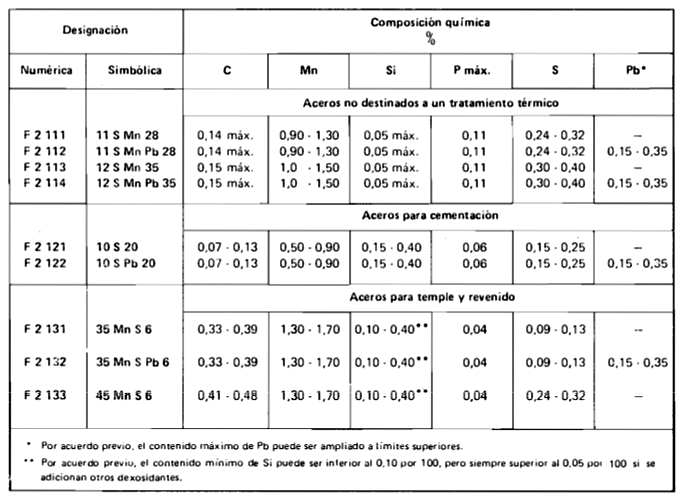
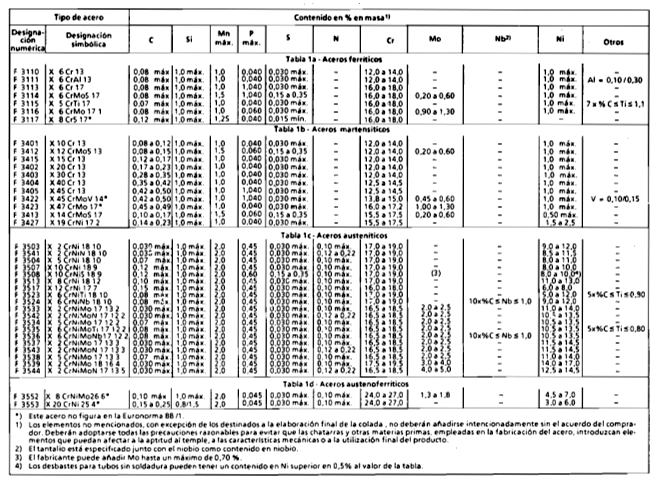
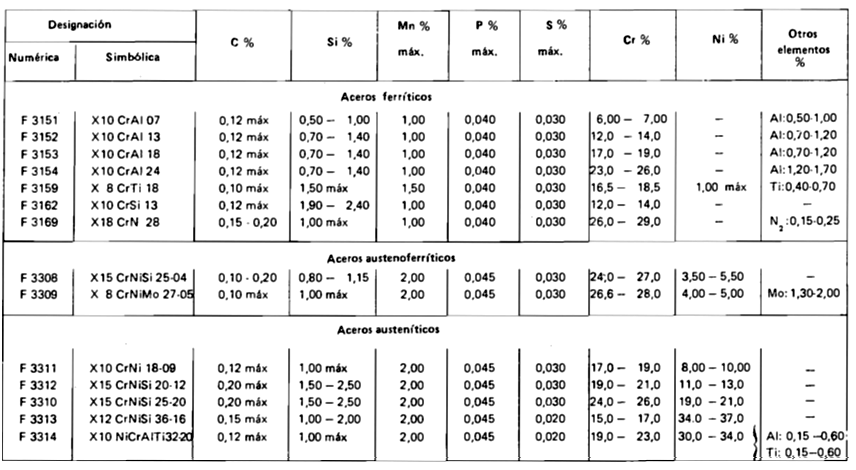
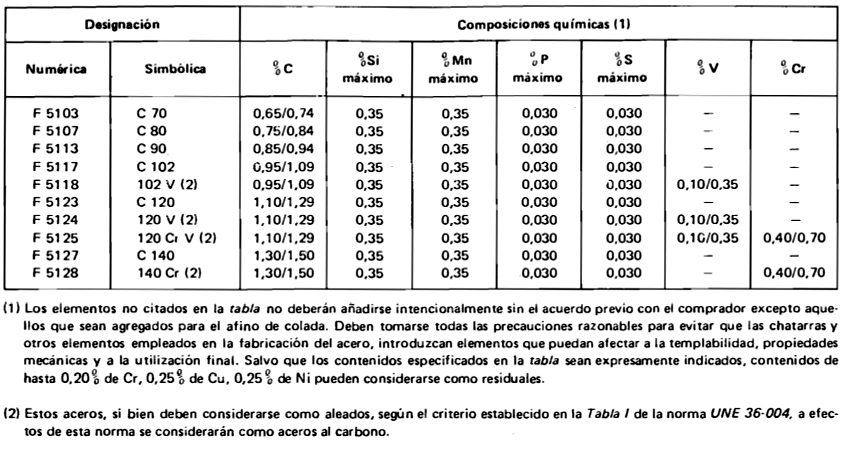
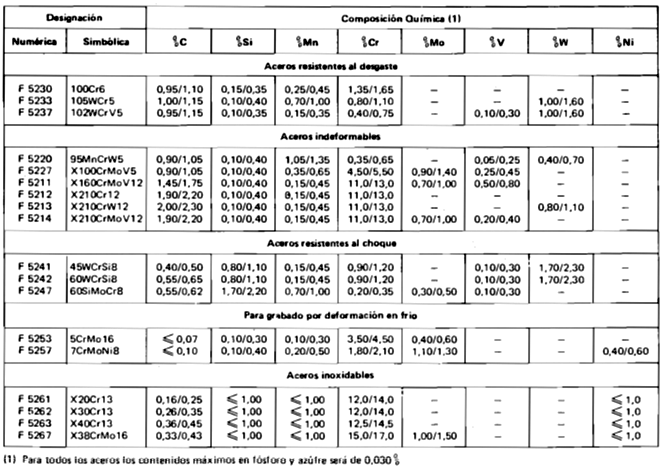
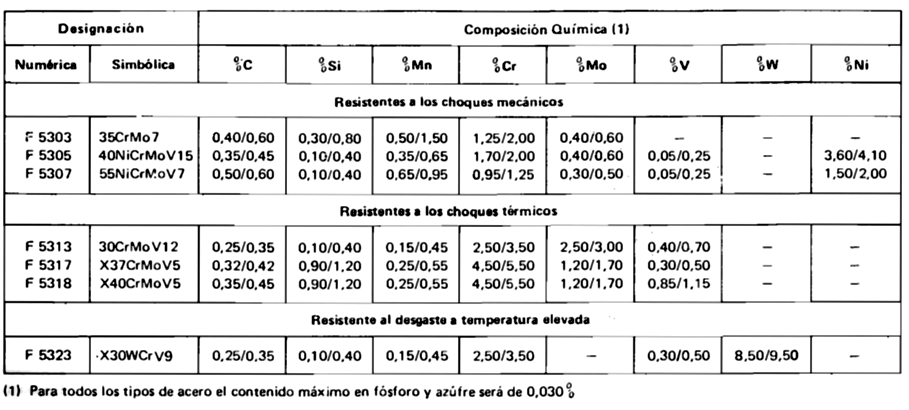
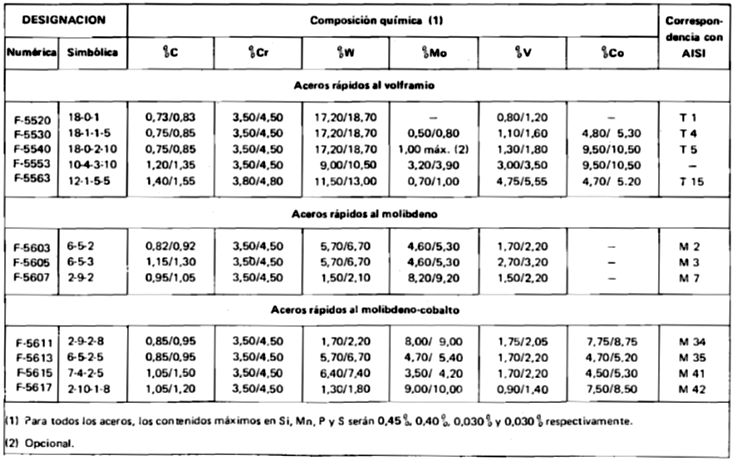