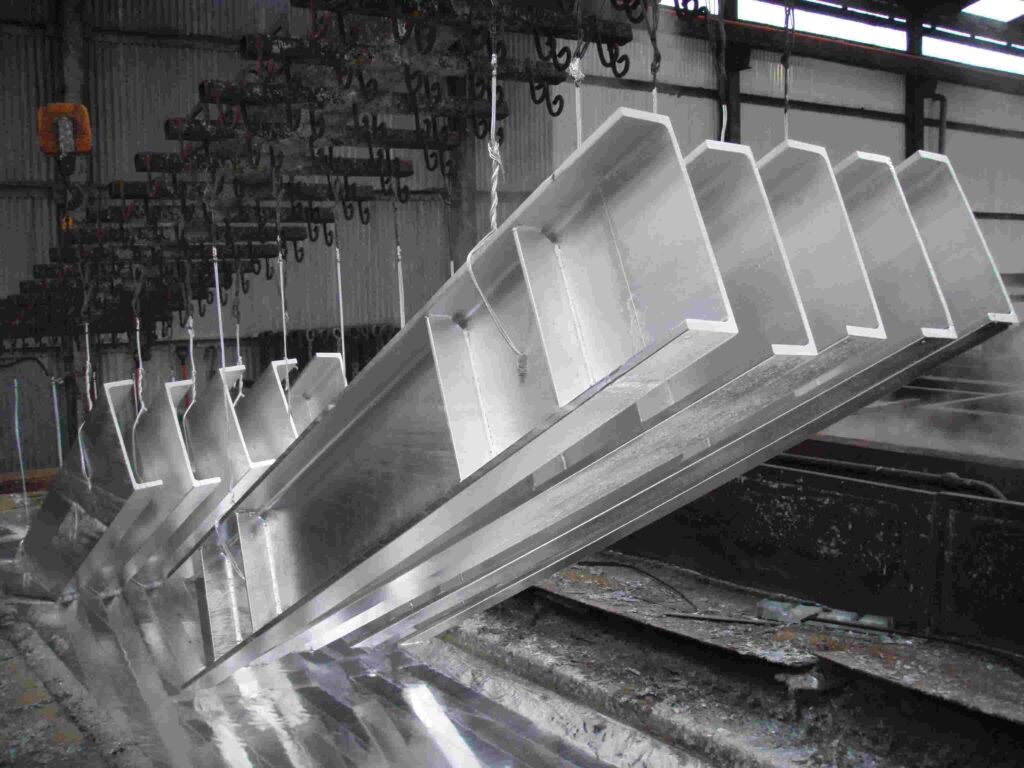
Generalidades
La protección contra la oxidación y corrosión es un problema muy complejo, en el que intervienen tantos factores que no se puede pensar en una solución de protección de tipo universal.
Los principales factores que se deben considerar en el estudio de las protecciones contra la oxidación y corrosión son los siguientes:
- Clase y estado del metal. Evidentemente hay que tener en cuenta, en primer lugar, la clase de metal y el estado en que se encuentra. Para esto hay que conocer su composición química, su constitución, estructura, impurezas que contiene, procedimientos de elaboración, tratamientos térmicos a que ha sido sometido, tratamientos mecánicos, etc.
- Medio en que se encuentra. El ataque al metal partirá del medio en que se encuentra y, por tanto, cuanto mejor lo conozcamos, más fácilmente será prever la clase de corrosión que se puede producir y los medios de evitarla. Sobre el medio conviene conocer su naturaleza química, su concentración, el porcentaje de oxígeno disuelto, el índice de acidez pH (el pH es el logaritmo de la inversa de la concentración del ión hidrógeno, El pH de una solución neutra es 7, Por encima de 7 es alcalina, y por debajo, ácida), presión, temperatura, etc.
- Clase de contacto entre el metal y el medio en que se encuentra. EI contacto entre el metal y el medio en que se encuentra queda definido por la forma de la pieza, estado de la superficie, condiciones de inmersión, etc.
Procedimientos empleados para la protección contra la oxidación y corrosión
Los procedimientos generalmente aplicados para la protección contra la oxidación y corrosión pueden clasificarse en seis grupos principales:
- Protección por recubrimientos metálicos.
- Protección por recubrimientos no metálicos,
- Protección por el empleo de inhibidores.
- Protección por el empleo de pasivadores.
- Protección catódica.
- Protección por el empleo de metales autoprotectores.
Sobre la elección del procedimiento más adecuado para cada caso no se pueden dar normas generales. Cada problema debe ser estudiado como un caso particular, puesto que simplemente pequeñas impurezas en el medio o en el metal pueden cambiar por completo el planteamiento del problema.
Protección por recubrimientos metálicos
Uno de los procedimientos más empleados contra la oxidación y corrosión es el recubrir la superficie que se desea proteger con una capa de metal autoprotector lo más compacta y adherente posible.
La elección del metal empleado en el recubrimiento se hace de acuerdo con el metal que se ha de proteger, del objeto de que se trata y del espesor que se proyecta dar a la capa protectora.
Cualquiera que sea el recubrimiento que se adopte, debe desengrasarse previamente la pieza con un disolvente apropiado, como sosa cáustica, tricloroetileno, benceno, etc. Después se elimina la cascarilla de la superficie del metal sometiéndolo a un decapado.
Los recubrimientos metálicos pueden aplicarse por varios procedimientos:
- Por electrólisis.
- Por inmersión en el baño del metal protector.
- Por metalización.
- Por cementación.
- Por chapado.
RECUBRIMIENTOS POR ELECTRÓLISIS.
Se obtienen películas de metal protector utilizando éste como ánodo, y las piezas que se desea recubrir, como cátodos, y empleando un electrólito de una solución del metal que se ha de depositar en forma de sulfatos o cianuros con adición de algunas sustancias orgánicas.
La electrólisis es la descomposición de una sustancia mediante la corriente eléctrica. La cantidad de sustancia transformada en cada electrodo viene dada por la ley de Faraday, que fundamentalmente describe a la cantidad de electricidad de 96.496 culombios como aquélla que descompone a un equivalente químico del electrólito.

Esto significa que esa cantidad de electricidad deposita un equivalente químico del metal en el cátodo. Teniendo en cuenta que se calcula el peso equivalente de un metal al dividir su masa atómica por la valencia.
Conociendo la superficie a recubrir y el espesor del recubrimiento, obtenemos el volumen de metal depositado. De esta manera y con el dato de la densidad podemos establecer la relación de tiempo e intensidad de corriente necesarios para obtener el recubrimiento deseado.
Los principales metales autoprotectores que se depositan electrolíticamente son: el cobre, el níquel y el cromo, y alguna vez, el cinc, el cadmio y el latón. También se depositan electrolíticamente el oro, la plata, el vanadio y el rodio, aunque estos metales tienen a veces más interés decorativo que protector.
El espesor de las películas es del orden de 0,001 a 0,01mm. El níquel y el cromo son los metales más empleados en recubrimientos electrolíticos. Cuando se trata de piezas de acero se aplican frecuentemente tres o cuatro capas: una de cobre, otra de níquel y otra de cromo, o bien una de níquel, otra de cobre, otra de níquel y otra de cromo. los espesores aproximados son: níquel, 0,005mm; cobre, 0,01mm; níquel, 0,02mm; cromo, 0,002mm. Para proteger el latón son suficientes dos capas: una de níquel, de 0,002mm, y otra de cromo, de 0,003mm. El níquel protege bien al acero contra la oxidación y corrosión, pero se empaña o mancha con el aire húmedo y por eso se acostumbra a aplicar una película de cromo sobre níquel, lo que resulta ventajoso porque el cromo es más duro que el níquel. El depósito del cobre tiene por objeto cubrir el metal base si queda algún poro en la película de níquel, y, además, aumentar la adherencia del revestimiento.
Se han hecho ensayos de depositar el cinc y el estaño electrolíticamente; pero estos metales se aplican corrientemente por inmersión, en su masa fundida, de los metales que se desea proteger.
El cadmio depositado electrolíticamente se creyó que desplazaría al cinc; pero en realidad sólo se emplea actualmente para objetos que han de funcionar en atmósferas tropicales.
RECUBRIMIENTOS POR INMERSIÓN EN BAÑO DE METAL FUNDIDO
Consiste este método en sumergir la pieza que se desea proteger, durante breve tiempo, en un baño de metal protector fundido. A la salida del baño se somete a la pieza a una especie de «enjuagado» que disminuye y, sobre todo, uniformiza el espesor de la capa del metal adherido. Los recubrimientos de este tipo más utilizados son el galvanizado y el estañado.
Galvanizado
El galvanizado es el recubrimiento del acero con cinc. El hierro es catódico respecto al cinc; por lo tanto, quedará protegido, aunque se produzca un poro o fisura en la capa protectora, pero a costa del cinc, que sufrirá la corrosión. Por esto debe ser la capa de cinc gruesa, por lo menos de 0,05gr. por cm2 de superficie, si se quiere que la protección sea efectiva.
Se emplea mucho el galvanizado para el recubrimiento de chapas acanaladas para techados; para la protección de alambres de hierro, de utensilios de cocina, de tuberías para agua, de utensilios para avicultura, etc. Parece demostrado, sin embargo, que las tuberías galvanizadas se corroen más rápidamente que sin galvanizar, si son de agua caliente. Si son de agua fría, la protección es eficaz.
Estañado
El estañado es un procedimiento de recubrimiento de los metales por inmersión en un baño de estaño fundido.
El estaño se aplica preferentemente para la fabricación de hojalata, que es acero suave calmado, con una película de estaño en cada cara, de unos 0,005mm.
El estaño es catódico con respecto al acero y, por tanto, en los poros o fisuras del recubrimiento se producirá una corrosión del metal base más intensa que si estuviese el metal desnudo. Sin embargo, en las conservas de frutas, los jugos cambian la polaridad electrolítica y el acero resulta generalmente catódico, por lo que se pierden pocos botes de conserva por corrosión. Algunos, en cambio, se rompen por la presión de hidrógeno desprendido en el cátodo.
El recubrimiento de estaño se emplea también para proteger utensilios de cocina, tuberías de agua de cobre, tubos de condensadores de latón, etc.
RECUBRIMIENTO POR METALIZACIÓN
La metalización, o sea, la proyección de un metal fundido con una pistola de metalizar, es un procedimiento de tratamiento superficial de los metales, que estudiaremos con más detalle en otra publicación de este blog.
La metalización se aplica, entre otros fines, para protección de las superficies metálicas contra la oxidación y corrosión, empleando generalmente, como metal protector, el cinc, el plomo y el aluminio. También se emplea el acero resistente a la corrosión en la metalización de ejes de bombas hidráulicas. La metalización tiene la ventaja de que se puede aplicar, a pie de obra, a objetos de todas las formas y tamaños, como gasómetros, vagones de ferrocarril, turbinas hidráulicas, barcos, etc.
RECUBRIMIENTOS POR CEMENTACIÓN
La cementación empleada para la protección contra la corrosión no debe confundirse con el tratamiento termoquímico de este nombre, aunque la operación es similar, pues se trata de alear por difusión la capa superficial del metal con otro más resistente a la corrosión. Pero, así como en la cementación (tratamiento termoquímico) el fin de la aleación es aumentar la dureza de la capa superficial, aquí se trata de obtener una capa protectora contra la corrosión.
Cuatro son los procedimientos de cementación más empleados:
- La sherardización.
- La cromización.
- La calorización.
- La silicación.
Sherardización
La sherardización fue ideada por Sherard Cowper Coles, en 1901. Se emplea para proteger contra la corrosión piezas pequeñas de acero de forma más o menos complicada, como cerrojos, etc., por medio de una aleación de cinc.
La operación consiste en calentar los objetos, una vez limpios y empaquetados con polvo de cinc y naftaleno, a unos 360°C. El naftaleno tiene por objeto proteger los granos de cinc de la oxidación.
Al final de la operación se forma una película de cinc puro sobre los objetos, de 0,02 a 0,05mm. de espesor, sobre una capa de una aleación hierro-cinc de un espesor de unos 0,5mm.
El recubrimiento es anódico respecto al acero, aunque de menos potencial que si el recubrimiento fuese de cinc puro; pero la protección se mantiene, aunque se produzcan grietas o poros.
Cromización
La cromización es un procedimiento caro, que se aplica sobre aceros de menos de 0,15% de carbono, y tiene como fin producir sobre las piezas una capa que contiene del 10 al 20% de cromo, es decir, una composición parecida al acero resistente a la corrosión, por difusión de cromo a través de la superficie del acero.
La operación se realiza empaquetando las piezas de acero con una mezcla de cromo y alúmina (Al20 3) finamente pulverizados, en la relación 55/34, y calentando el conjunto a unos 1.350°C durante 3 o 4 horas, en una atmósfera de hidrógeno para que no se oxide el cromo. La alúmina tiene por objeto evitar la formación de conglomerados de cromo.
Otro método para aplicar la cromización es calentar el acero entre 900° y 1.000°C, en una atmósfera de cloruro crómico gaseoso. Al cabo de 2 horas se forma una capa cromizada de unos 0,1mm. de espesor.
Se emplea la cromización principalmente para proteger los ejes de las turbinas contra la corrosión y erosión y para la protección del acero contra el ácido nítrico.
Calorización
La calorización, también denominada aluminación, tiene por objeto proteger el acero por medio del aluminio. La calorización se realiza en un horno giratorio, en el que se calientan a unos 850°C las piezas, una vez limpias y empaquetadas con una mezcla del 49% de polvo de aluminio, 49% de alúmina y 2% de cloruro amónico. Al cabo de 1 hora, aproximadamente, se habrá formado una capa de 0,1 a 1mm. de aleación hierro-aluminio, que contiene aproximadamente un 25% de aluminio, y sobre ella una capa protectora de alúmina (Al20 3), cuyo punto de fusión es muy elevado.
Las piezas calorizadas son muy resistentes a la corrosión producida por gases sulfurosos a alta temperatura, y por eso se emplea este método para la protección de crisoles para sales fundidas en los tratamientos térmicos, cajas de carburación, cubiertas de pirómetros, etc.
Silicación
La silicación consiste en la formación, en la superficie del acero, de una capa de aleación hierro-silicio, que contiene hasta un 20% de silicio, que es el porcentaje de algunas fundiciones especiales muy resistentes a la corrosión por los ácidos fuertes. Se opera calentando de 900° a 1.000°C el acero una vez limpio, empaquetado con una mezcla de carburo de silicio y ferrosilicio.
Los aceros siliciados resisten bien no sólo a la corrosión, sino también a la erosión, y por esto se aplican a la protección de los ejes de bombas de fluidos.
RECUBRIMIENTOS POR CHAPADO
El chapado o «plaqueado» consiste en superponer placas de un metal noble por una o las dos caras del metal que se desea proteger. La operación se realiza laminando las chapas de acero junto con las protectoras, produciéndose una difusión de los metales en la zona de contacto. El chapado se hace, generalmente, con láminas de cobre, latón, níquel y cuproníquel, y modernamente con chapas de acero resistentes a la corrosión. Los objetos fabricados con acero chapado tienen buenas propiedades mecánicas por el alma de acero, y excelente resistencia a la corrosión, por las láminas protectoras.
Protección por recubrimientos no metálicos
Se utilizan los siguientes procedimientos para conseguir un recubrimiento no metálico resistente a la oxidación y corrosión:
- Fosfatación.
- Oxidación superficial.
- Esmaltado.
- Pintado.
RECUBRIMIENTOS POR FOSFATACIÓN
Consiste este procedimiento en sumergir las piezas de acero en una solución acuosa de un fosfato metálico ácido, que puede ser fosfato ácido de manganeso, fosfato diácido de cinc o fosfato diácido de sodio.
La solución de fosfato diácido de manganeso se calienta a una temperatura de 100°C, sumergiendo en el baño las piezas, sobre las que se obtiene una capa de fosfato insoluble de un espesor de 0,01mm., según la reacción:
2 Mn (H2P04) + 2 Fe → Mn (P04)2 + 2 H2
Se emplea como catalizador una pequeña cantidad de sal de cobre. La protección obtenida por este procedimiento es muy eficaz, sobre todo si se completa con una impregnación de una materia grasa. La solución de fosfato diácido de cinc se calienta a unos 80° de temperatura. La pieza se sumerge solamente durante algunos minutos, siendo la operación tan rápida porque se añade a la solución un oxidante que quema hidrógeno. Esta protección es menos eficaz que la anterior, y por eso se emplea sólo como impregnación previa a una aplicación posterior de pintura o barniz. El fosfato diácido de sodio se emplea proyectando su solución sobre el acero, teniendo lugar en la capa superficial la siguiente reacción:
3 NaH2P04 + 3 Fe → Fe3(P04)2 + Na3P04 + 3 H2
La protección que se obtiene es inferior a la obtenida por los fosfatos anteriores; pero se emplea por el mejor precio de los fosfatos alcalinos.
RECUBRIMIENTO POR OXIDACIÓN SUPERFICIAL
La formación de una película superficial de óxido para proteger el metal es un medio bastante eficaz, que se emplea, sobre todo, para las aleaciones de aluminio y magnesio. La oxidación puede realizarse por:
- Oxidación por Calentamiento.
- Oxidación anódica (electrólisis).
- Oxidación química (ataque de un ácido).
Oxidación por calentamiento
La oxidación por calentamiento se emplea preferentemente para el acero. Se opera calentando las piezas de acero en un horno abierto o en un bailo de sales fundidas formadas por una mezcla de nitrato sódico y potásico a una temperatura de 260° a 400°. La película que se produce es de oxido férrico magnético Fe304′ Si se emplean sales, su color es azul y recibe el nombre de pavonado.
Otro procedimiento es el de Bower-Barff, que consiste en calentar a 650°C, durante 3 horas, las piezas de acero, una vez limpias, en un horno cerrado, en el que se desplaza el aire por medio de vapor de agua recalentado o una mezcla de vapor de agua y benceno. Al terminar la operación se deja enfriar el acero hasta 150°C y se introducen las piezas en aceite de linaza hirviendo, manteniendo la misma temperatura hasta que el aceite se ha oxidado. Con esto el óxido férrico primeramente formado se habrá reducido a la forma más resistente de óxido ferroso-férrico. La capa de óxido es negra, siendo opaca o lustrosa según el acabado previo superficial del acero.
Oxidación anódica
La oxidación anódica se aplica, sobre todo, para la protección de piezas de aluminio. Actualmente está muy en boga este procedimiento para la producción de objetos decorativos, pues la película de óxido puede teñirse con diversos pigmentos, consiguiendo piezas de bello aspecto, que permanece inalterable casi indefinidamente.
La película de óxido formada sobre aluminio y sus aleaciones, cuando se exponen al aire libre, es bastante protectora, y por eso se pensó que una película de óxido más gruesa, producida artificialmente, mejoraría la protección.
La oxidación anódica del aluminio se realiza empleando las piezas como ánodo, y como electrólito, el ácido oxálico, el ácido crómico o el ácido sulfúrico al 20%. Este es el procedimiento más empleado, con el nombre de aluminita. La oxidación la realiza el oxígeno que se desprende en el ánodo y que forma una película protectora de óxido de unos 0,02mm. Después del tratamiento se cierran los poros que contiene la capa formada, por inmersión en agua hirviendo o en vapor de agua, lo que produce una expansión de la capa por transformarse parte del óxido en la forma hidratada. A esta operación se le llama, sellado.
La oxidación anódica se aplica también para la formación de los denominados condensadores electrolíticos, utilizando como electrólitos ácido bórico y boratos, que producen recubrimientos muy delgados y sin poros y de un gran poder aislante de la electricidad en uno de los sentidos. Por eso los condensadores electrolíticos sólo se utilizan para corriente continua, pues si se invierte la polaridad se destruye la capa de óxido.
Oxidación química
La oxidación química consiste en sumergir el metal o aleación en una solución acuosa de un cuerpo capaz de reaccionar sobre el metal formando una película muy delgada de óxido o de una sal compleja insoluble. Este procedimiento se aplica a las aleaciones de magnesio, empleando soluciones de bicromato alcalino en ácido nítrico. La protección conseguida por oxidación química es inferior a la obtenida por oxidación anódica.
Existen otros tratamientos para producir pátinas, bronceados, etc., que tienen como fin producir una película de óxido por procedimientos empíricos que mejoran el aspecto del metal, pero tienen poca eficacia desde el punto de vista protector contra la oxidación.
RECUBRIMIENTOS POR ESMALTADO
Los esmaltes son esencialmente borosilicatos de calcio, de potasio y de plomo, que se aplican formando una papilla sobre el metal previamente desengrasado y decapado. Una vez secas, se introducen las piezas en un horno donde se funde el esmalte formando una capa protectora vidriada. El esmaltado se utiliza mucho para utensilios de cocina caseros y para aparatos empleados en la industria química. Los esmaltes tienen el inconveniente de que no son elásticos y saltan con facilidad si se golpean.
RECUBRIMIENTOS CON PINTURAS
Existen muchas clases de pinturas que proporcionan una protección más o menos eficaz contra la corrosión.
Las pinturas al aceite no son anticorrosivas y solamente se les asigna, desde el punto de vista de protección contra la oxidación y corrosión, una misión impermeabilizante, aparte del efecto decorativo. Normalmente deben aplicarse por lo menos dos capas, sobre una imprimación previa en el metal de un pigmento pasivador, como el minio o el cromato de cinc. Estos detienen la corrosión aun cuando se produzca algún poro en la capa de pintura que llegue hasta el metal base. Las capas de pintura al aceite evitan que el pigmento pasivador sea arrastrado por el agua de lluvia o alterado por la atmósfera viciada.
De las pinturas al aceite, las fabricadas con pigmentos de óxido férrico (Fe203), y precisamente con el denominado hierro oligisto micanio, son las que dan mejor resultado.
Las pinturas a base de purpurinas formadas por aluminio o polvo de aluminio tienen propiedades impermeabilizantes superiores a las pinturas al aceite.
También se emplean mucho actualmente pinturas de caucho dorado y poliestireno, que contienen polvo de cinc y que al secarse dan un acabado similar al galvanizado.
Las pinturas cuya base son los alquitranes procedentes de la destilación de la hulla, o los betunes naturales, se emplean también mucho para la protección, sobre todo, de tuberías enterradas. A las pinturas a base de alquitrán conviene adicionarles cal para neutralizar su acidez. Todas las pinturas de esta clase tienen el inconveniente de que se cuartean si sufren grandes variaciones de temperatura, y además fluyen en tiempo caluroso y se hacen frágiles en tiempo frío.
Toda aplicación de pintura de cualquier clase debe ir precedida de un desengrasado y decapado cuidadoso del metal para hacer desaparecer toda traza de óxido o cascarilla.
Protección por el empleo de inhibidores
Un inhibidor es una sustancia que se añade, generalmente en proporción muy pequeña, a un medio corrosivo, para detener a disminuir la velocidad de la corrosión formando un compuesto insoluble sobre la superficie del metal, bien sea catódica o anódica.
Los inhibidores se emplean mucho en el decapado ácido, para disminuir la velocidad de ataque del metal a decapar sin interferir la eliminación de la capa de óxido. Existen dos clases de inhibidores: los anódicos y los catódicos.
Inhibidores anódicos
Los inhibidores anódicos reaccionan sobre las partes anódicas del metal, formando un compuesto protector. Se emplean como inhibidores anódicos el carbonato sódico, el bicarbonato sódico, el fosfato sódico, el silicato y el cromato sódicos. También se emplea el bicromato potásico en la proporción de 0,2%.
Los inhibidores catódicos forman compuestos protectores sobre el cátodo, empleándose para este fin sulfato de magnesio, de níquel y de cinc. Los inhibidores catódicos se utilizan para evitar la corrosión del acero en aguas neutras.
Existen otros inhibidores denominados de absorción, que son sustancias coloidales que se fijan sobre el metal. Entre éstos pueden citarse la gelatina, el tanino, el agar-agar, etc.
Protección por el empleo de pasivadores
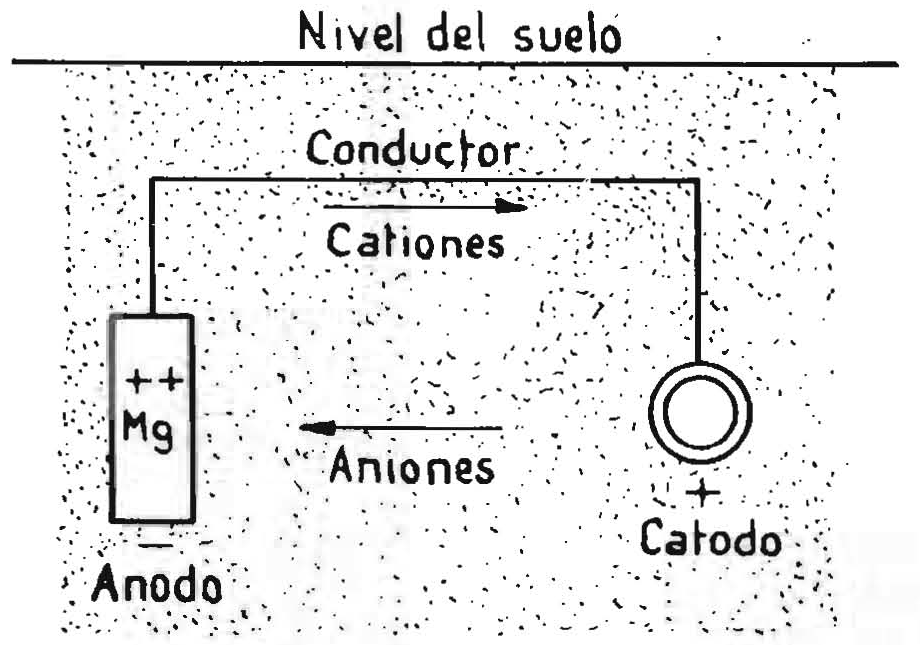
En algunos metales se forma una película en su superficie que detiene la corrosión apenas iniciada. Se dice entonces que estos metales tienen pasividad natural contra la corrosión en el medio que ocurre eso. También puede conseguirse la pasividad tratando previamente el metal. Un ejemplo de pasividad provocada es la que se obtiene sumergiendo una pieza de acero en ácido nítrico concentrado, resultando así inatacable por el ácido nítrico diluido, que sin esta pasivación lo ataca fácilmente.
No se conocen bien las causas de la pasivación, pero se atribuye, en general, o bien a la formación de películas gaseosas protectoras, generalmente de oxígeno e hidrógeno, o bien a la formación de películas sólidas, generalmente de óxidos, que protegen el metal, como ocurre con el aluminio, que posee pasividad natural.
Los pasivadores más empleados son el minio y el cromato de cinc, ambos muy usados como impregnadores de las piezas de acero antes de aplicar cualquier pintura sobre ellos. El minio es óxido de plomo (Pb304), y es quizá el pigmento pasivador más empleado. El cromato de cinc (ZnCr04) transforma los iones ferrosos generados en el agua en férricos, produciendo una capa bastante insoluble, en el ánodo, de óxido férrico.
Queremos hacer notar que la diferencia entre un pasivador como el minio, por ejemplo, y una pintura antioxidante, preparada a base de óxido férrico, es que si se hace una raya en la pintura que descubra el metal, resulta éste atacado; pero si la raya se hace en una superficie recubierta con minio, no se produce en ella ninguna corrosión.
Protección catódica contra la corrosión
La protección catódica consiste en incluir la pieza que se desea proteger en un circuito eléctrico con fuerza electromotriz exterior aplicada, o sin ella, de manera que el metal haga de cátodo.
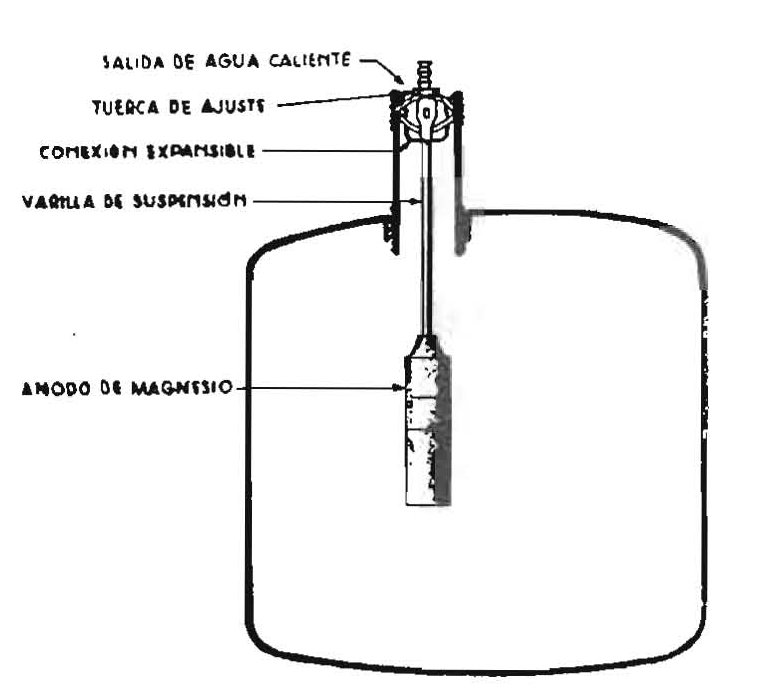
Este método se funda en el hecho comprobado de que, si se sumergen dos metales de distinto potencial galvánico, por ejemplo, cinc y hierro, unidos o puestos en contacto en una solución salina, se produce una corriente eléctrica a través del electrólito, que va del metal anódico -en este caso el cinc- al catódico, que es el hierro, que neutraliza las acciones electroquímicas locales entre distintas zonas que habría en cualquiera de los metales de haberse aislado. En este caso particular, el hierro resulta protegido a costa de consumirse el cinc.
Los ánodos más utilizados, cuando se aplica protección catódica sin suministro de energía eléctrica exterior, son de cinc, aluminio, magnesio o aleación rica en magnesio. El aluminio tiene el inconveniente de formar una capa de óxido que disminuye su acción protectora.
Los cascos de los navíos se protegen contra la corrosión galvánica producida por la acción de las hélices de bronce colocando ánodos de cinc o de magnesio en el casco, en las proximidades de la hélice.
Si la resistencia del electrólito, o sea, del medio en que está el metal (puede ser tierra húmeda, etc.) es demasiado grande y la corriente que circula entre los dos metales es demasiado débil para anular las corrientes locales, debe proveerse un suministro de corriente continua exterior para establecer una corriente eléctrica de intensidad adecuada. Naturalmente, este tipo de protección exige el sacrificio del metal que hace de ánodo.
Los ánodos utilizados cuando se emplea la protección catódica con suministro de energía eléctrica exterior pueden ser de hierro, generalmente tubos o chapas viejas, pues ya no es necesario que el metal protector tenga distinto potencial galvánico que el metal protegido. La fuente de energía eléctrica debe dar corriente continua, y generalmente se emplean rectificadores de corriente alterna o baterías de acumuladores.
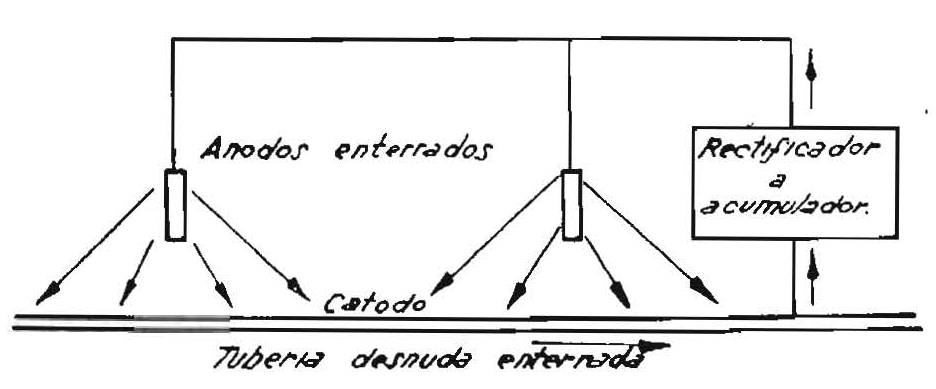
La densidad de corriente necesaria para obtener protección por cada metro cuadrado de superficie metálica podrá variar según el aislamiento de la pieza entre los límites siguientes:
- Acero sin aislamiento 5-50 A/m2
- Acero con aislamiento medio 0,5-4 A/m2
- Acero bien aislado 0,05-0,25 A/m2
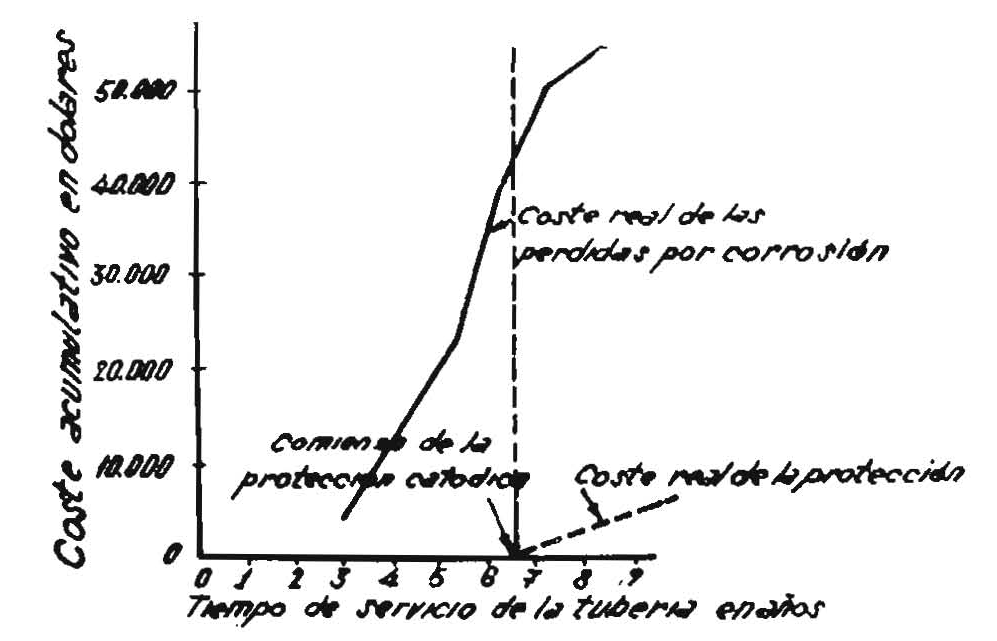
O sea, que si las piezas, tuberías, por ejemplo, tienen un buen recubrimiento protector, los gastos originados por la oxidación catódica se reducirán notablemente.
Por esto, en general, sólo se emplea la oxidación catódica con suministro de energía eléctrica en los puntos más expuestos a la corrosión, que pueden determinarse midiendo la resistencia eléctrica del terreno. Todas las zonas de menor resistencia con respecto a las vecinas son zonas de corrosión de intensidad apreciable. Únicamente se emplea la protección catódica con fuerza electromotriz exterior aplicada, para protección total de tuberías o juntas enterradas cuando están muy bien revestidas, porque entonces la densidad de corriente necesaria es muy pequeña.
Protección por el empleo de metales autoprotectores
Uno de los procedimientos más sencillos para proteger las piezas contra la oxidación y corrosión es fabricarlas con metales auto protectores, es decir, metales que tengan la suficiente resistencia contra la oxidación y corrosión que haga innecesaria la aplicación de ninguna protección adicional.
Así el cromo, el níquel, el platino, el oro, el tántalo y el wolframio, entre otros, son muy resistentes a la oxidación y corrosión atmosférica y a la acción de muchos ácidos. Pero su elevado precio impide su utilización salvo para aplicaciones científicas.
Únicamente se emplea en gran escala el plomo para muchas aplicaciones anticorrosivas, entre ellas el revestimiento de las cámaras de fabricación de ácido sulfúrico.
En cambio, se emplean mucho las aleaciones autoprotectoras, que son más económicas y además tienen, en general, mejores características que los metales puros, para muchas aplicaciones. Las aleaciones anticorrosivas que más se emplean son los aceros resistentes a la corrosión y las aleaciones de níquel.
ACEROS RESISTENTES A LA CORROSIÓN
La solución para proteger de la oxidación y corrosión a los aceros consiste generalmente en incorporar a su composición cromo en la proporción suficiente para que forme en la superficie de la pieza una capa de óxido superficialmente compacta e impermeable que proteja el resto del metal de la oxidación y corrosión. Como ya hemos podido ver en la publicación dedicada a los aceros resistentes a la corrosión, éstos pueden ser martensíticos, ferríticos o austeníticos, conteniendo estos últimos, níquel en bastante proporción para, contrapesando la acción del cromo, conseguir el estado austenítico a la temperatura ambiente. A veces contienen también los aceros resistentes a la corrosión, pequeñas cantidades de otros elementos, como wolframio, molibdeno, titanio, etc., cuya misión es aumentar la resistencia a la corrosión en ciertos casos particulares. Hay también aceros que resisten la corrosión mejor que el acero ordinario y que pudieran calificarse de semi-resistentes, como son los aceros al cobre, al níquel-cobre y también los de baja aleación de cromo (del 2 al 6%), y que se emplean mucho en la industria del petróleo. Los aceros resistentes a la corrosión pertenecen a tres grupos principales:
- Aceros al cromo.
- Aceros al cromo-níquel.
- Aceros al níquel.
Aceros al cromo
Los aceros con 12 al 15% de cromo son martensíticos después del temple al aire. Se utilizan para cuchillería, álabes de turbinas, ejes de bomba, etc. El temple y revenido les da la máxima resistencia a la corrosión y, al mismo tiempo, un excelente límite elástico. Resisten a la corrosión a temperaturas de 750°C.
Los aceros de menos del 0,12% de carbono y 15 al 30% de cromo son ferríticos y no adquieren, por tanto, temple. Se utilizan en la industria alimenticia y en la del ácido nítrico. Resisten sin oxidarse temperaturas de 850° a 1.050°C, según el contenido en cromo.
Aceros al cromo-níquel
Estos aceros son austeníticos. El acero 18-8 (18% de cromo y 8% de níquel) es el más utilizado, aunque se emplean también los de 12-12 y 25-20. El cromo le da la resistencia a la corrosión, y el níquel tiene por objeto obtener un estado austenítico homogéneo a la temperatura ambiente, en cuyo estado presenta el acero una resistencia química a la corrosión, muy elevada para numerosos reactivos. En particular resiste bien a la acción del agua del mar, aunque mejora notablemente con la adición de molibdeno. Resisten también los aceros al cromo-níquel austeníticos temperaturas de 950° a 1.150°C.
Un grave inconveniente de los aceros 18-8 con el 0,10% de carbono, como ya hemos visto en publicaciones anteriores en este blog, es que están en el límite de la austenita estable. Cuando se calientan entre 500° y 850°C, particularmente cuando se quiere soldar, se deposita (por precipitación) carburo de cromo en el contorno de los granos. El carbono y el cromo necesarios para la formación de una partícula de carburo provienen de las partes adyacentes de la austenita que quedan empobrecidas de cromo, y si este contenido queda inferior al 12%, puede sufrir corrosión intergranular.
Para remediar este inconveniente puede recurrirse a tres procedimientos:
- Disminuir la proporción de carbono del acero hasta un 0,02%, con cuyo contenido el acero 18-8 es insensible a la corrosión intergranular.
- Incorporar titanio o niobio, que son elementos muy ávidos de carbono, con el que forman carburos y dificultan la formación de carburo de cromo. e) Elevar el contenido de cromo y disminuir el de níquel para obtener una estructura mixta de austenita y ferrita. Los aceros al cromo-níquel 18-8, con un 2 a un 4% de molibdeno, resisten mejor cierta clase de corrosión química.
Aceros al níquel.
Los aceros con un 25 a un 35% de níquel y un 2% de cromo resisten mejor que los anteriores, a base de cromo y cromo-níquel, la acción del ácido clorhídrico y sulfúrico.
OTRAS ALEACIONES AUTOPROTECTORAS.
Se emplean también aleaciones autoprotectoras a base de níquel, cobre y aluminio, de las cuales podemos destacar:
- Inconel (80% de níquel, 14% de cromo, 6% de hierro), utilizada mucho en la industria lechera.
- Hastelloy B (62 % de níquel, 30 % de molibdeno y 5 % de Fe), que resiste muy bien el ácido clorhídrico.
- Monel (67 % de niquel, 30 % de cobre, 1,4 % de Fe, 1% de Mn y 0,15% de C).
- Cuproaluminios (del 6 al 12% de aluminio), muy utilizados en tubos de condensadores, monedas, etc.
Decapado
La eliminación de la capa de laminación y del orín en la superficie de las piezas de acero es absolutamente necesaria antes de aplicar un recubrimiento de cualquier clase. Esta eliminación se efectúa por medio de una operación que se denomina decapado, que puede efectuarse por procedimientos mecánicos, químicos y electrolíticos.
DECAPADO MECÁNICO
La limpieza de la superficie de las piezas puede realizarse con cepillos de alambre, que limpian bastante la cascarilla, aunque siempre dejan residuo. Aquélla queda brillante por el frotamiento del cepillo, dando apariencia de que el metal ha quedado completamente limpio.
El chorro de arena realiza una limpieza de gran calidad. Este procedimiento se ha descrito anteriormente.
También se emplea el chorro de perdigones, proyectado con una máquina especial que los recupera, y cuya acción, además, sobre la superficie de la pieza mejora su resistencia a la fatiga.
DECAPADO QUÍMICO
Sin embargo, el procedimiento más empleado, sobre todo como operación previa para el galvanizado y estañado, es la limpieza por medio de ácidos.
El decapado químico se realiza sumergiendo la pieza en ácido sulfúrico diluido al 10% a unos 80°C, durante 5 minutos, o en ácido clorhídrico en frío, al 20%, ayudando alguna vez, aunque no es frecuente, a levantar la cascarilla raspando la superficie de la pieza.
Para evitar que resulte excesivamente atacado el metal, se añaden a la solución del ácido inhibidores que retardan el ataque del metal sin interferir la eliminación de la cascarilla y el orín. Se emplean como inhibidores sustancias coloidales como la gelatina, agar-agar y tanino. Sin embargo, se suelen emplear corrientemente inhibidores más complejos, como el di-orto-tolil-tiourea o el dihidro-diorto-toluidina. La eficacia de los inhibidores disminuye a medida que se eleva la temperatura.
Las piezas decapadas en ácido clorhídrico y sulfúrico se enmohecen al exponerlas al aire. Para evitar esto, se emplea un acabado con ácido fosfórico, que les da una protección adicional, formada por una película gris de fosfato de hierro y sobre la que se aplica en muy buenas condiciones la pintura. Puede seguirse el procedimiento siguiente: se sumergen las piezas, primero, en una solución de ácido sulfúrico al 5%, a 60°C, durante 15 a 20 minutos; se lavan después con agua a 60°C, y se sumergen finalmente de 2 a 3 minutos en ácido fosfórico al 2%, a 85°C. Esta solución ha de tener además 0,3-0,5% de hierro al iniciar el tratamiento. La proporción de ácido fosfórico debe mantenerse añadiendo más a medida que se consuma.
DECAPADO ELECTROLÍTICO.
El decapado electrolítico puede realizarse haciendo actuar los objetos de acero como ánodos en una solución de ácido sulfúrico al 30% que contiene bicromato potásico. La densidad utilizada es de unos 10 amperios por dm2.