Dur-aluminio
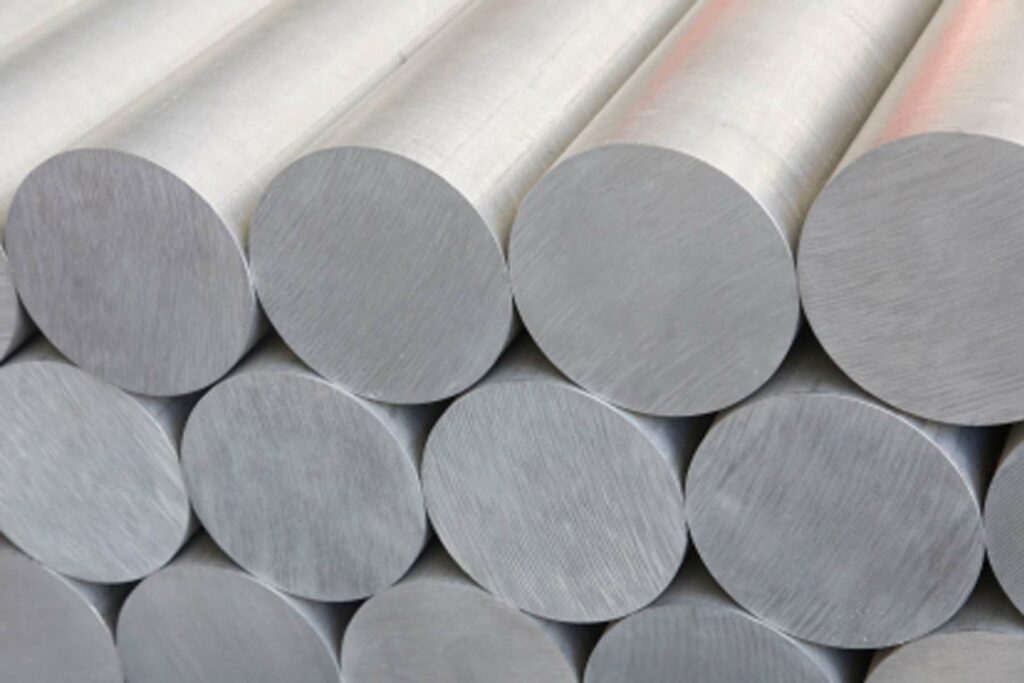
Desde el punto de vista físico, el aluminio puro posee una resistencia muy baja a la tracción y una dureza escasa. En cambio, unido en aleación con otros elementos, el aluminio adquiere características mecánicas muy superiores.
El duraluminio pertenece a la familia de aleaciones aluminio-cobre y es una de las más utilizadas, además de la más antigua. Esta aleación fue registrada en 1909 y desarrollada unos años antes, de forma accidental, por Alfred Wilm en la ciudad alemana de Düren, con el fin de mejorar las características mecánicas del aluminio.
La aleación contiene pequeñas cantidades de cobre (Cu) (3 – 5%), magnesio (Mg) (0,5 – 2%), manganeso (Mn) (0,25 – 1%) y Zinc (3,5 – 5%). Sólo se usan en la práctica materiales de aluminio que contienen otros elementos (con la excepción del aluminio purísimo Al99,99), ya que incluso en aleaciones con una pureza del 99% sus propiedades vienen determinadas en gran parte por el contenido en hierro o silicio.
Las variaciones más notorias respecto al aluminio, son:
- Mejor resistencia a la tracción y resistencia mecánica a temperatura ambiente.
- Baja resistencia a la corrosión.
- Baja soldabilidad.
- Buena mecanización.
- Mejor resistencia a la abrasión.
Aunque el duraluminio todavía es una aleación muy utilizada en la actualidad, está siendo reemplazada por aleaciones de Titanio y otros materiales compuestos.
La estructura bifásica de equilibrio a temperatura ambiente, α+θ, es frágil en relación con la forma y tamaño de la dura fase θ, ver Fig. 3. La fase θ corresponde al intermetálico CuAl2, (Al-52,5%p.Cu). Por otra parte, la fase α es una solución sólida de sustitución, de carácter metálico y, por ende, es relativamente dúctil y blanda.
En la aleación Al-4,5%p.Cu a 520°C, se tiene rápidamente la fase α de equilibrio a esa temperatura (a este tratamiento térmico se le llama solubilización). En seguida, por temple, es posible retener la fase α a temperatura ambiente, en forma metaestable, ver Fig. 4. Esta fase α está sobresaturada en Cu, respecto del Cu que debería contener la solución de estar ella al equilibrio. En tal estado metaestable, el material es dúctil y puede ser ventajosamente mecanizado por arranque de viruta y conformado plásticamente.
Después, ya trabajada la pieza, , el material puede ser endurecido a través de un tratamiento térmico denominado de “envejecimiento”. Durante este tratamiento se forman finísimas partículas de una segunda fase en la matriz α; cuando estas partículas son las adecuadas, el material endurece sin alcanzar una excesiva fragilidad. Este envejecimiento puede hacerse ya sea en forma natural (y menos controlada, p.e. poniendo el material al sol durante algunas centenas de horas), o bien en forma artificial en hornos (y controlada), p.e. a 130-230°C por algunas horas.
Si consideramos un tratamiento a 130°C. de esta manera el sistema tenderá a evolucionar desde la fase α sobre saturada, hacia las dos fases de equilibrio a esa temperatura, α + θ. Aquí́ la transformación se iniciará (nucleará́) en muchos puntos de transformación, por lo que la segunda fase aparecerá como muchas partículas finas. El proceso es complicado, pues hay varios precipitados intermedios antes de llegar al precipitado de equilibrio final que es θ. De hecho, las mejores propiedades mecánicas en términos de buen compromiso entre dureza y ductilidad, se logra con uno de los precipitados intermedios; de esta manera, cuando aparece tal precipitado, (esto es, cuando se logran las propiedades mecánicas requeridas) hay que detener el tratamiento. Si se continúa con el tratamiento térmico, el material disminuye significativamente su dureza y entonces se habla de sobreenvejecimiento.
El proceso de manufactura consiste entonces en:
- Primero, el metal se templa y luego es conformado plásticamente y/o mecanizado en el blando estado de temple, fase α metaestable .
- Después, una vez que ya se le ha dado la forma adecuada, se procede a endurecer el material por envejecimiento. Se trata de tener una estructura final de finas partículas de unprecipitado intermedio, duro, reforzando a la dúctil matriz base Al. Esa matriz es una solución sólida que contiene algo de Cu disuelto.
Para evitar que el material templado aún no trabajado endurezca en las bodegas, se procura trabajarlo poco después del temple, o bien hay que guardarlo en refrigeradores.
Las transformaciones de precipitación durante el envejecimiento son bastante complejas, pues aparece una secuencia de varios precipitados. El envejecimiento de dureza máxima y óptima corresponde a la formación de una fina fase θ ́ ́metaestable (o zonas GP2). Si el tratamiento se prolonga demasiado, indeseablemente la dureza disminuye: los precipitados de fase θ ́ ́ crecen y se transforman gradualmente primero en precipitados θ ́ y después en la fase de equilibrio θ (sobreenvejecimiento).
La secuencia de las transformaciones de precipitación a 130°C en el horno de envejecimiento es la siguiente:
- Solución sólida sobresaturada en Cu. -Zonas GP1
- Zonas GP2 o fase θ ́ ́. Son especies de discos de 1-4 nm de espesor y de 10- 100 nm de diámetro.
- Fase θ ́
- Fase de equilibrio θ (CuAl2).
Los precipitados que aparecen en estas aleaciones θ ́ ́ son muy finos como para poder observarlos por microscopía óptica. Se requiere Microscopía Electrónica de Transmisión; esta misma técnica de observación es la que permite ver los finos carburos precipitados en la martensita revenida. En la industria se evita el uso de microscopía electrónica utilizando materias primas y procesos muy controlados, además de mediciones de propiedades mecánicas y de conductividad eléctrica.
El aluminio permite ser aleado con diferentes materiales y conseguir así, diferentes características, que en función de ellas, son usadas para diferentes fines. Las principales son:
Serie | Designación | Aleante principal | Características | Aplicaciones |
1000 | 1XXX | Mínimo 99% de aluminio | Resistencia a la tracción y corrosión. Excelente maquinabilidad y elongación. | Laminados en frío, conductores eléctricos. |
2000 | 2XXX | Cobre | Alta elongación y anticorrosivo. Baja maquinabilidad. Resistencia a la tracción. | Fuselajes de aviones. |
3000 | 3XXX | Manganeso | Resistencia moderada contra los agentes atmosféricos y químicos. Ofrecen características mecánicas más altas y mejor capacidad de transformación que el aluminio puro. | Recocido, para usos que requieren buena maquinabilidad. |
4000 | 4XXX | Silicio | Bajo punto de fusión y alta resistencia a la corrosión | Arquitectura. |
5000 | 5XXX | Magnesio | Buena resistencia a la corrosión, soldadura y funcionamiento en frío | Chapas de aluminio para transporte terrestre o naval. |
6000 | 6XXX | Magnesio y Silicio | Excelente resistencia a la tracción y corrosión. Baja maquinabilidad. | Perfiles extruídos para carpinterías de fachadas. |
7000 | 7XXX | Cinc | Máximos valores de dureza y resistencia. | Estructuras y partes superiores de aviones, como las alas. |
8000 | 8XXX | Otros elementos | Mayor dureza, mejor capacidad de transformación y rigidez mejorada | Industria aeroespacial. |